ریختهگری مداوم در زنجیره فولاد: تحول ساختاری در تولید صنعتی
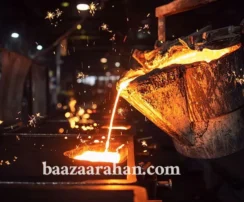
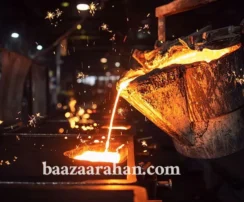
1. ریختهگری مداوم چیست و چرا اهمیت دارد؟
ریختهگری مداوم (Continuous Casting) در زنجیره فولاد فرآیندی است که در آن فولاد مذاب بهطور پیوسته به محصولی نیمهنهایی مانند شمش تبدیل میشود. این روش جایگزین ریختهگری قالبی سنتی شده است. کارخانهها با استفاده از آن، بهرهوری را افزایش میدهند و ضایعات را کاهش میدهند.در این فرآیند، اپراتورها فولاد مذاب را از کوره به تاندیش منتقل میکنند. سپس آن را وارد قالبهای آبگرد میسازند.
این قالبها با خنکسازی سریع، پوستهای جامد در اطراف مذاب ایجاد میکنند. نوار فولادی تشکیلشده، بهصورت مداوم از پایین قالب خارج میشود. در ادامه، برشگرها آن را به قطعات موردنظر تقسیم میکنند. شرکتهای فولادسازی از این فناوری برای کاهش زمان توقف، بهبود کنترل ترکیب شیمیایی، و ارتقاء یکنواختی ساختاری استفاده میکنند. بهجای انجماد در قالبهای جداگانه، مواد مستقیماً به خطوط نورد منتقل میشوند.
این اتصال پیوسته، بهرهبرداری از انرژی را بهینه میکند. اهمیت ریختهگری مداوم فقط به کاهش هزینه محدود نمیشود. این روش، دقت تولید را افزایش میدهد. همچنین کیفیت سطحی بهتر و ساختار داخلی پایدارتر فراهم میکند. بسیاری از شرکتهای پیشرو مانند ArcelorMittal، POSCO و فولاد مبارکه از این فناوری بهره میبرند. در واقع، ریختهگری مداوم در زنجیره فولاد تنها یک مرحله نیست؛ یک مزیت راهبردی است. این روش، صنعت فولاد را وارد عصر جدیدی کرده است؛ عصری که در آن تولید سریع، دقیق و بهصرفه حرف اول را میزند.
2. بررسی تاریخی تحول ریختهگری فولاد: از قالبریزی سنتی تا ریختهگری مداوم
تاریخچه ریختهگری فولاد نشان میدهد که صنعت همواره در جستجوی بهرهوری بیشتر بوده است. در گذشته، کارگاهها فولاد مذاب را در قالبهای ثابت میریختند. این روش قدیمی، کند و پرهزینه بود. قالبها بهسختی خنک میشدند و انجماد ناهمگن، نقصهایی در محصول ایجاد میکرد. در دهه ۱۹۵۰، مهندسان اروپایی و ژاپنی نخستین خطوط ریختهگری مداوم را راهاندازی کردند. شرکتهایی مثل Mannesmann (آلمان) و Nippon Steel (ژاپن) نقش کلیدی در توسعه اولیه این فناوری داشتند.
در ایران، فولاد مبارکه و ذوبآهن اصفهان از دهه ۷۰ شمسی به استفاده از این روش روی آوردند. تغییر از روش قالبی به سیستم پیوسته، انقلابی در تولید فولاد به وجود آورد. کارخانهها دیگر نیازی نداشتند که فولاد را در قالب بریزند، صبر کنند تا منجمد شود، و دوباره آن را برای نورد گرم کنند. فرآیند جدید، این گامهای جداگانه را یکی کرد. سرعت بالا رفت، مصرف انرژی پایین آمد و کیفیت بهطور محسوسی بهتر شد. بسیاری از کشورها از این نقطه، رقابت جهانی در تولید فولاد را آغاز کردند. کره جنوبی و هند با سرمایهگذاری سنگین، کارخانههای خود را به خطوط مداوم مجهز کردند. امروز، بیش از ۹۰ درصد فولاد خام جهان از طریق ریختهگری مداوم تولید میشود. تاریخ نشان داده که فناوری، موتور محرک صنعت است. ریختهگری مداوم، نمونهای روشن از این اصل است. تحولی که نهتنها روش تولید، بلکه فلسفه آن را نیز تغییر داد.
3. زنجیره ارزش در صنعت فولاد و جایگاه راهبردی ریختهگری مداوم
زنجیره تولید فولاد شامل چند مرحله کلیدی است: احیای سنگآهن، فولادسازی، ریختهگری، نورد و در نهایت، آمادهسازی محصول نهایی. ریختهگری مداوم، نقطه اتصال میان فولادسازی و نورد است. این نقطه نهتنها عملیاتی، بلکه راهبردی است. در این مرحله، فولاد مذاب از حالت سیال به جامد تبدیل میشود.
اگر این تغییر با کنترل دقیق انجام نشود، کیفیت نهایی کل زنجیره آسیب میبیند. به همین دلیل، واحد ریختهگری مداوم قلب زنجیره ارزش بهحساب میآید. کارخانههایی که ریختهگری پیوسته دارند، میتوانند محصولات را سریعتر وارد خط نورد کنند. آنها وابستگی کمتری به ذخیرهسازی بینمرحلهای دارند. همچنین زمان انتظار مواد بین دو مرحله کاهش مییابد. این ویژگیها باعث کاهش مصرف انرژی، هزینههای نگهداری و توقف خطوط میشود. شرکتهایی مانند Tata Steel و Voestalpine با تحلیل زنجیره ارزش، سرمایهگذاریهای خود را به سمت ریختهگری متمرکز کردهاند. آنها معتقدند که افزایش کیفیت در این مرحله، هزینههای کل زنجیره را کاهش میدهد.
از منظر مهندسی سیستم، پیوستگی بین فولادسازی، ریختهگری و نورد مزایای فراوانی دارد. هماهنگی دمایی، همزمانی عملیات، و کاهش افت حرارتی از جمله این مزایا هستند. این هماهنگی، زنجیره را چابکتر و پایدارتر میسازد. در نهایت، ریختهگری مداوم فقط یک فناوری نیست؛ یک گره استراتژیک در زنجیرهای پیچیده است. گرهای که اگر درست عمل کند، جریان ارزش در کل زنجیره تقویت میشود.
4. فرآیند گامبهگام در ریختهگری مداوم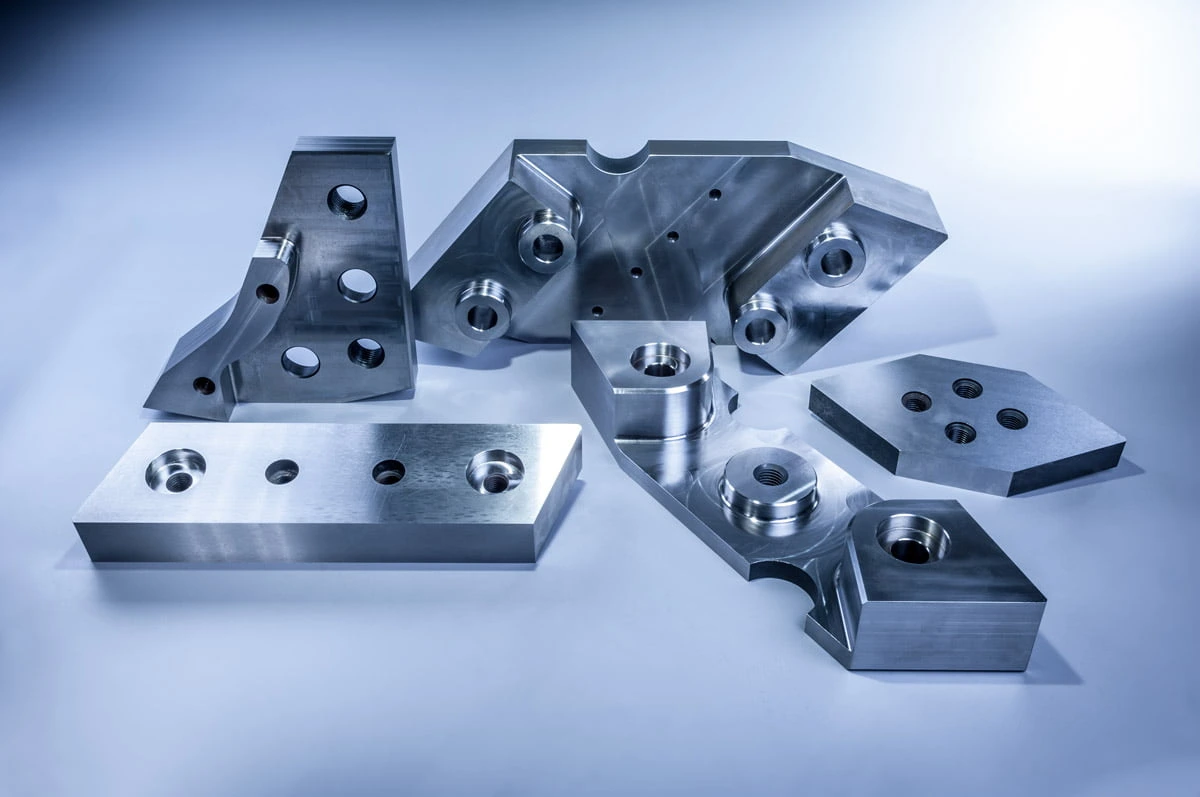
فرآیند ریختهگری مداوم شامل چند مرحله مشخص و منظم است. هر مرحله نقش کلیدی در تبدیل فولاد مذاب به محصول نیمهنهایی ایفا میکند. این مسیر با تخلیه فولاد مذاب از کوره آغاز میشود. ابتدا، اپراتورها فولاد مذاب را به تاندیش منتقل میکنند. تاندیش یک محفظه نگهدارنده بین کوره و قالب است. این مخزن وظیفه توزیع یکنواخت مذاب را بین قالبها بر عهده دارد و همچنین به کنترل دمای جریان کمک میکند.
در مرحله دوم، فولاد مذاب از تاندیش وارد قالب مسی آبگرد میشود. این قالب با سیستم خنککننده قوی، پوسته اولیه جامد را تشکیل میدهد. سطح فولاد در تماس با دیواره قالب منجمد میشود، در حالیکه مرکز آن هنوز مذاب باقی میماند. مرحله سوم، عبور از ناحیه غلتکهای خنککننده است. این غلتکها جریان مذاب را هدایت میکنند و همزمان به انجماد کامل آن کمک مینمایند. حسگرهای متعدد در این بخش، دمای نقاط مختلف را کنترل میکنند تا محصول نهایی کیفیت یکدست داشته باشد.
در گام آخر، تیغههای برش (Shear Blades) نوار جامدشده را به طولهای مشخص برش میزنند. محصولات نهایی شامل بیلت (Billet)، بلوم (Bloom) یا اسلب (Slab) هستند. هر نوع برای کاربردهای خاص در نورد گرم یا سرد استفاده میشود. این فرآیند پیوسته، با دقت بالا و اتوماسیون گسترده انجام میگیرد. کارخانههایی که این فناوری را اجرا کردهاند، بهرهوری را بهطور محسوسی افزایش دادهاند. کنترل دقیق، سرعت بالا و کیفیت پایدار، از ویژگیهای بارز این
روش محسوب میشود .
5. مزایا و چالشهای عملیاتی ریختهگری مداوم
استفاده از ریختهگری مداوم مزایای متعددی دارد که آن را به گزینهای بهینه برای تولید انبوه تبدیل کرده است:
- افزایش بهرهوری: خطوط پیوسته میتوانند بهصورت ۲۴ ساعته کار کنند و توقفهای مکرر ندارند.
- کاهش مصرف انرژی: خنکسازی سریع و انتقال مستقیم به نورد، نیاز به حرارتدهی مجدد را کاهش میدهد.
- کیفیت سطح بالا: تماس کنترلشده با قالب باعث کاهش عیوب سطحی میشود.
- پایداری ساختاری: انجماد یکنواخت، ترکهای داخلی را به حداقل میرساند.
- کاهش ضایعات: فرآیند دقیق و پیوسته باعث کاهش پرت مواد میشود.
اما این فناوری بدون چالش نیست. راهاندازی اولیه تجهیزات هزینهبر است. سیستمهای خنککاری نیاز به نگهداری دقیق دارند. کنترل دمای مذاب در طول مسیر نیز حساس و بحرانی است. بهعنوان مثال، در صورت ناهماهنگی بین سرعت قالب و انجماد، مشکلاتی مانند ترکهای عرضی، ناپایداری پوسته و حتی شکست در خروجی ایجاد میشود. همچنین در مواقعی که کیفیت شارژ اولیه (فولاد مذاب) پایین باشد، تمام فرآیند تحت تأثیر قرار میگیرد.
علاوه بر این:
- تجهیزات اتوماسیون نیاز به کالیبراسیون دقیق دارند.
- بهرهبرداری نادرست میتواند باعث توقف خط شود.
- آلودگی محیطی در برخی بخشها هنوز چالشبرانگیز است.
در مجموع، موفقیت در بهرهبرداری از ریختهگری مداوم نیازمند آموزش نیروی انسانی، پایش مداوم و سرمایهگذاری هوشمندانه است. این فرآیند اگرچه پیچیده است، اما سوددهی آن در بلندمدت اثباتشده است.
6. تجهیزات کلیدی در واحد ریختهگری مداوم
در هر خط ریختهگری مداوم، مجموعهای از تجهیزات تخصصی با نقشهای مشخص فعالیت میکنند. شناخت این تجهیزات برای درک عملکرد سیستم ضروری است.
در یک نگاه، تجهیزات اصلی عبارتاند از:
-
تاندیش (Tundish): مخزن میانی که فولاد مذاب را از پاتیل به قالب منتقل میکند. عملکرد آن توزیع یکنواخت، همگنسازی دما و حذف ناخالصیهاست.
-
قالب آبگرد (Mold): بخش آغازگر انجماد. جنس آن از مس است و با آب خنک میشود. قالب شکل اولیه محصول (بیلت، بلوم یا اسلب) را تعیین میکند.
-
غلتکهای هدایت و پشتیبانی: این غلتکها مسیر حرکت نوار مذاب را تثبیت میکنند. همزمان به انجماد یکنواخت کمک مینمایند.
-
سیستم خنککاری ثانویه: با استفاده از اسپریهای آب، دمای فولاد در حال جامد شدن را کنترل میکند. این سیستم برای جلوگیری از ترکهای حرارتی حیاتی است.
-
تیغههای برش (Shear Blades): نوار جامدشده را به طولهای مشخص برش میدهند. سرعت و دقت عملکرد آنها بر کیفیت محصول اثر مستقیم دارد.
بهعنوان نمونه، در فولاد مبارکه، استفاده از قالبهایی با خنککاری هوشمند باعث بهبود یکنواختی پوسته شده است. همچنین استفاده از حسگرهای دمایی در ناحیه غلتکها، کنترل فرآیند را بهمراتب دقیقتر کرده است. نکته مهم این است که هر یک از این اجزا باید هماهنگ با سایر بخشها عمل کند. کوچکترین اختلال در یک بخش، میتواند کل خط را متوقف کند. به همین دلیل، اتوماسیون، مانیتورینگ پیوسته و نگهداری پیشگیرانه نقش حیاتی دارند. در نتیجه، تجهیزات ریختهگری مداوم فقط ابزار مکانیکی نیستند. آنها اجزای یک سیستم دقیق، هوشمند و بههمپیوسته هستند که موفقیت تولید فولاد به عملکرد درست آنها وابسته است.
7. انواع محصولات خروجی از ریختهگری مداوم و کاربردهای آنها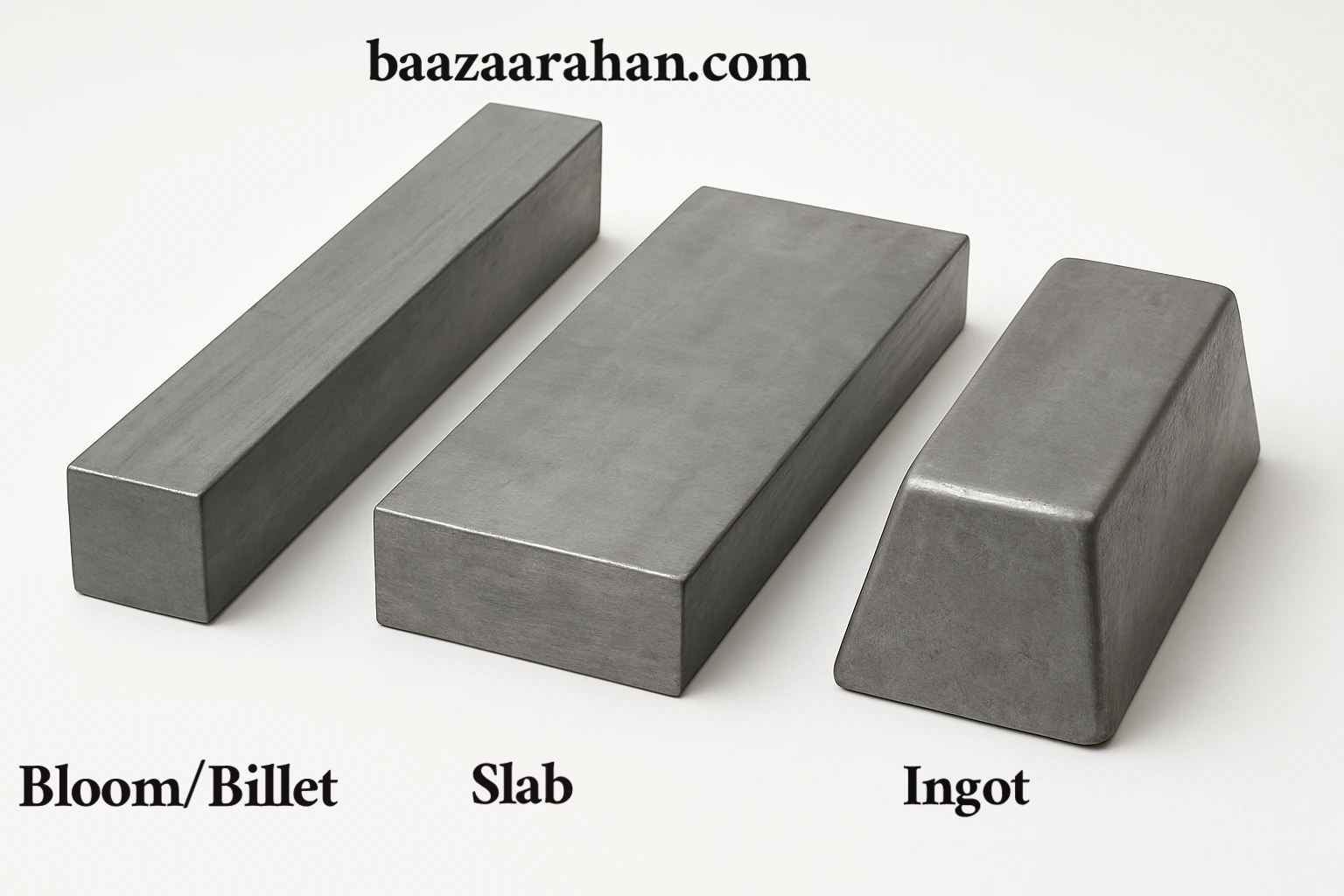
ریختهگری مداوم، فولاد مذاب را به محصولات نیمهنهایی مختلفی تبدیل میکند. هر یک از این محصولات، ویژگیهای فیزیکی و هندسی خاص خود را دارند و برای مصارف متنوعی در صنایع پاییندستی به کار میروند.
انواع خروجی اصلی در ریختهگری مداوم شامل موارد زیر است:
-
بیلت (Billet): مقطع مربع یا دایره دارد و معمولاً برای ساخت میلگرد، مفتول، پیچ و مهره استفاده میشود.
-
بلوم (Bloom): ابعادی بزرگتر از بیلت دارد و در تولید ریل، سپری، ناودانی، و تیرآهن بهکار میرود.
-
اسلب (Slab): مقطع مستطیلی و پهن دارد. این محصول در نورد گرم تبدیل به ورق، کویل و محصولات تخت میشود.
در خطوط ریختهگری، قالب انتخابشده و ابعاد نهایی نوار، تعیینکننده نوع محصول هستند. بهعنوان مثال، در فولاد مبارکه، تمرکز بر تولید اسلبهایی با ضخامت یکنواخت و کیفیت سطحی بالا برای بازار ورق است. در مقابل، ذوبآهن اصفهان ظرفیت بالایی در تولید بلوم دارد که به صنایع ساختمانی خدمات میدهد.
کاربردهای محصولات نیمهنهایی بر اساس شکل و خواص مکانیکی آنها تعریف میشود:
-
بیلت: صنایع سیم و کابل، قطعات ماشینابزار، فنرهای فولادی.
-
بلوم: سازههای فلزی، خطوط راهآهن، پلها.
-
اسلب: خودروسازی، لوازم خانگی، تانکرها، کشتیسازی.
در کنار این سه نوع، برخی کارخانهها توانایی تولید Near Net Shape نیز دارند. در این روش، مقاطع نزدیک به شکل نهایی تولید میشوند و به فرآیند نورد حداقلی نیاز دارند. این روش در کاهش انرژی و زمان بسیار مؤثر است. در مجموع، تنوع خروجی در ریختهگری مداوم به کارخانهها امکان میدهد تا پاسخگوی نیازهای گوناگون بازار باشند. تطبیقپذیری این فناوری، آن را به ستون فقرات زنجیره تامین فولاد تبدیل کرده است.
8. کنترل کیفیت در ریختهگری مداوم: ابزارها، روشها و عوامل کلیدی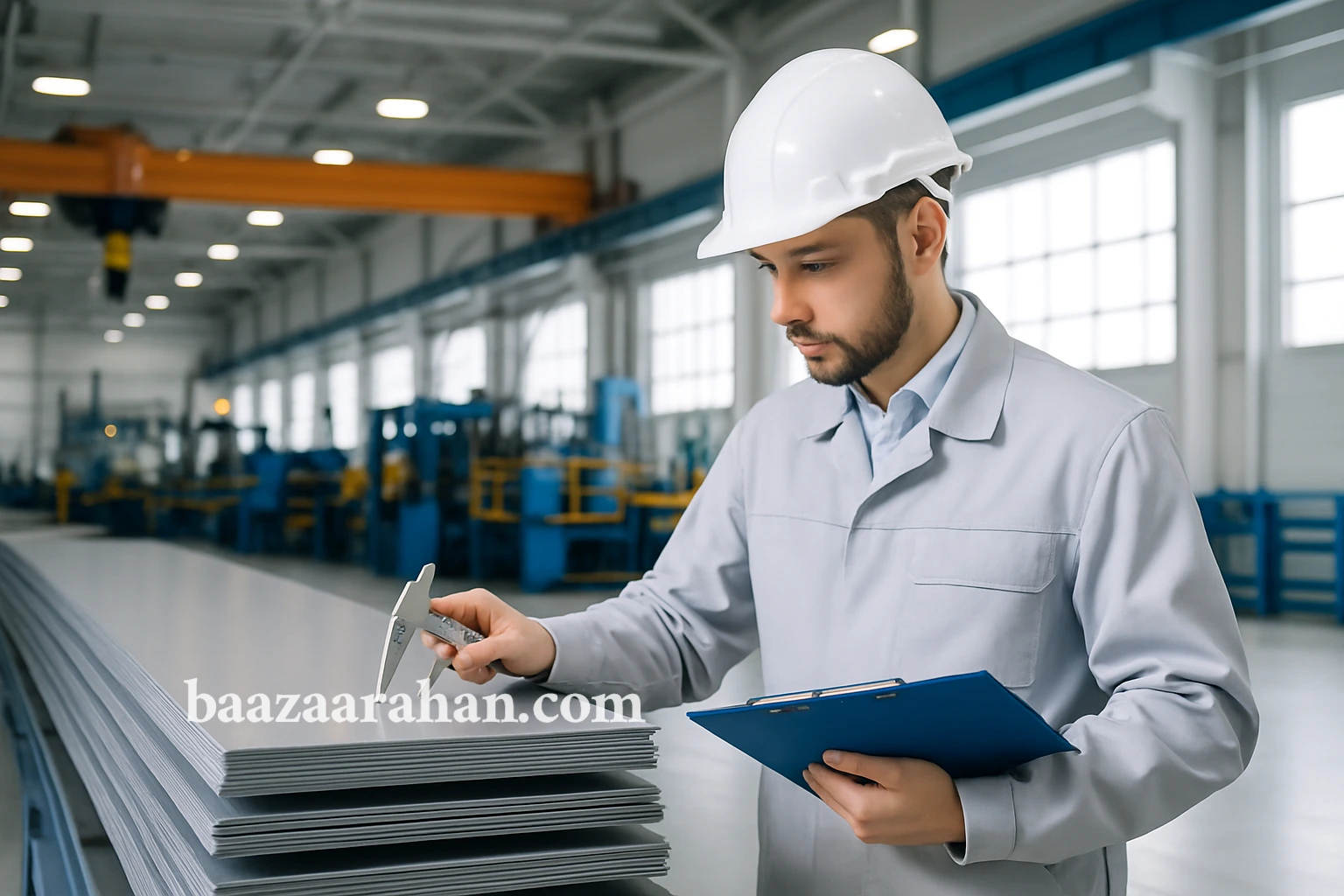
این قسمت در ریختهگری مداوم اهمیت بالایی دارد. هر نوسان کوچک در دما، ترکیب یا سرعت میتواند عیوبی جدی در محصول نهایی ایجاد کند. به همین دلیل، کارخانهها از ترکیبی از تجهیزات مدرن، پایش لحظهای و اقدامات اصلاحی سریع استفاده میکنند.
ابزارهای رایج برای پایش و کنترل کیفیت شامل موارد زیر است:
-
حسگرهای دمایی (Thermocouples): در نقاط کلیدی مثل تاندیش، قالب و خروجی نصب میشوند. این حسگرها تغییرات دما را لحظهبهلحظه ثبت میکنند.
-
سیستمهای سطحسنج (Mold Level Controllers): ارتفاع مذاب در قالب را پایدار نگه میدارند. نوسانات سطح باعث ایجاد ترک یا ناپایداری پوسته میشود.
-
دوربینهای حرارتی (Thermal Cameras): نقشه حرارتی سطح فولاد را ثبت میکنند. این تصاویر، نقصهای حرارتی پنهان را آشکار میسازند.
-
سیستمهای تحلیل سرعت و کشش (Tension-Speed Monitors): کشش بیشازحد یا تغییر ناگهانی در سرعت، به پوسته نیمهجامد آسیب میزند.
در کنار تجهیزات، استانداردهای داخلی کارخانهها نیز نقش دارند. برای مثال، محدوده مجاز دمای ورود به قالب یا نرخ خنککاری ثانویه در چکلیستهای روزانه ثبت میشود. اگر پارامترها از این محدوده خارج شوند، سیستم هشدار داده و اپراتورها مداخله میکنند.
از منظر عملیاتی، کنترل کیفیت به سه مرحله اصلی تقسیم میشود:
-
پیشگیرانه: تنظیم دقیق پارامترها قبل از شروع ریختهگری.
-
حین تولید: پایش مداوم و واکنش سریع به تغییرات.
-
پس از تولید: بررسی سطح، ساختار داخلی و ابعاد محصول خروجی.
برای مثال، فولاد مبارکه با استفاده از سیستم هوش مصنوعی، توانسته نرخ بروز ترکهای سطحی را تا ۳۰ درصد کاهش دهد. یا در شرکت POSCO، دادههای بهدستآمده از دوربینهای حرارتی به الگوریتمهای یادگیری ماشین منتقل میشوند تا خطاهای احتمالی پیشبینی شوند. در نهایت، ریختهگری مداوم بدون کنترل کیفیت دقیق، بهسرعت از مدار بهرهوری خارج میشود. ترکیب فناوری، تجربه انسانی و تحلیل داده، سه ستون اصلی تضمین کیفیت در این فرآیند پیچیده هستند.
9. نوآوریها و روندهای نوین در فناوری ریختهگری مداوم در فولاد
فناوری ریختهگری مداوم در سالهای اخیر بهسرعت پیشرفت کرده است. رقابت جهانی و نیاز به کاهش هزینهها، کارخانهها را به سمت نوآوریهای مستمر سوق داده است. امروز، این فرآیند دیگر فقط یک عملیات حرارتی-مکانیکی نیست؛ ترکیبی از اتوماسیون پیشرفته، هوش مصنوعی، و مواد نوین است.
برخی از مهمترین نوآوریها در ریختهگری مداوم عبارتاند از:
-
ریختهگری نازک (Thin Slab Casting): این فناوری، اسلبهایی با ضخامت کمتر از 100 میلیمتر تولید میکند. کاهش ضخامت باعث کاهش مراحل نورد و صرفهجویی در انرژی میشود.
-
سیستمهای هوشمند کنترل قالب: قالبها به حسگرهای داخلی مجهز شدهاند که دادههایی مانند دما، فشار، و نرخ خنککاری را ثبت میکنند. این اطلاعات در لحظه به سامانه مرکزی منتقل میشود.
-
یکپارچهسازی با نرمافزارهای MES و ERP: هماهنگی کامل بین خط تولید، مدیریت موجودی و برنامهریزی تولید. این پیوندها، تلفات را کاهش داده و تولید را منعطفتر میکنند.
-
کاربرد هوش مصنوعی (AI) و یادگیری ماشین (ML): سیستمها با بررسی دادههای تولیدی، الگوهای بروز نقص را شناسایی میکنند و حتی پیش از وقوع مشکل، هشدار میدهند.
در فولاد مبارکه، پیادهسازی سیستم کنترل هوشمند برای قالبهای آبگرد باعث کاهش دمای بیشازحد در ناحیه پوسته شده است. همچنین شرکت ArcelorMittal پروژههایی برای توسعه قالبهای خودتنظیم (Self-Adjusting Molds) اجرا کرده است که خودشان خنککاری را بهصورت بلادرنگ تنظیم میکنند.
علاوه بر این، روندهای جدیدی مانند:
-
استفاده از مواد پوششی مقاومتر برای افزایش عمر قالبها
-
توسعه سیستمهای بدون نیاز به روانکار سنتی (Dry Casting)
-
کاربرد پهپادها برای پایش بصری خطوط ریختهگری
نیز در حال شکلگیریاند.
در یک نگاه کلی، ریختهگری مداوم از یک فرآیند صنعتی سنتی، به یک اکوسیستم دیجیتال و پویا تبدیل شده است. آینده این حوزه در گروی پیوند هوشمند بین مهندسی، داده و فناوری است.
10. جمعبندی و چشمانداز آینده ریختهگری مداوم در صنعت فولاد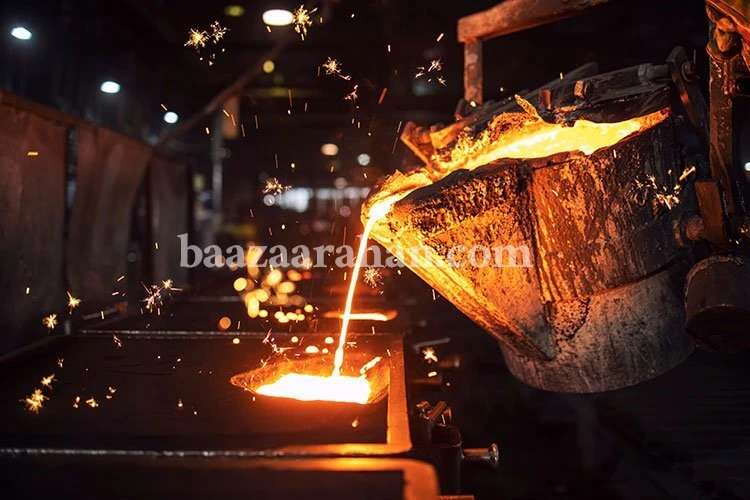
ریختهگری مداوم، قلب تپندهی تولید مدرن فولاد است. این فناوری نهتنها جایگزین روشهای قدیمی شده، بلکه به نیروی محرکهای برای تحول در زنجیره ارزش تبدیل گشته است. کارخانههایی که در این حوزه سرمایهگذاری کردهاند، از بهرهوری، کیفیت و پایداری بیشتری برخوردارند. در این مقاله، به ابعاد مختلف این فناوری پرداختیم؛ از تعریف پایه، تاریخچه، مراحل اجرایی، مزایا، چالشها و کنترل کیفیت گرفته تا نوآوریها و ترندهای جهانی. این گستردگی نشان میدهد که ریختهگری مداوم صرفاً یک فرآیند نیست؛ بلکه یک بستر تحولساز است.
نکات کلیدی که باید در آینده مدنظر قرار گیرد:
-
دیجیتالیسازی فرآیند: استفاده از هوش مصنوعی، یادگیری ماشین و پایش ابری برای تصمیمگیری لحظهای.
-
پایداری زیستمحیطی: کاهش مصرف آب، کنترل دقیق گازهای خروجی و استفاده از انرژیهای جایگزین در بخش خنککاری.
-
افزایش انعطافپذیری خطوط: طراحی خطوطی که بتوانند بهراحتی بین تولید اسلب، بلوم و بیلت جابجا شوند.
-
آموزش نیروی انسانی: مهارتهای دیجیتال و دادهمحور باید جایگزین رویکردهای صرفاً عملیاتی شوند.
شرکتهایی مانند POSCO و SSAB با تکیه بر این اصول، خطوط ریختهگری نسل آینده را طراحی کردهاند. در ایران نیز گامهای خوبی برداشته شده، اما توسعه زیرساختهای نرمافزاری، آموزش تخصصی و نوسازی تجهیزات از ملزومات دوره پیشروست. چشمانداز آینده، خطوطی خواهد بود که نهتنها بدون نقص و پایدار تولید میکنند، بلکه خود یاد میگیرند، تنظیم میکنند و بهینهسازی را در لحظه انجام میدهند. در این چشمانداز، مهندس ریختهگری نه اپراتور دستگاه، بلکه تحلیلگر دادههای فرآیندی است. در پایان، باید گفت: ریختهگری مداوم در فولاد ، تنها پیوند بین فولاد مذاب و محصول جامد نیست؛ بلکه پلی است میان گذشتهی صنعتی و آیندهی هوشمند صنعت فولاد.