بررسی جامع فرآیندهای تولید آهن خام: از کوره بلند تا فناوریهای نوین سبز
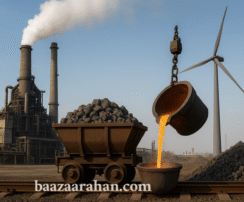
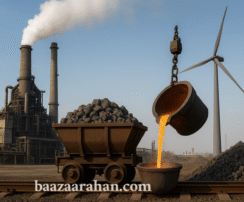
مقدمه
تولید آهن خام یکی از اساسیترین مراحل در زنجیره تأمین صنایع فولاد بهشمار میرود. این فرآیند، پایهگذار بسیاری از فعالیتهای صنعتی در جهان مدرن است. بدون آهن خام، ساختوساز، خودروسازی، صنایع سنگین و بسیاری از بخشهای دیگر اقتصاد جهانی عملاً متوقف میشوند. در واقع، تولید آهن خام نهتنها یک فرآیند فنی است، بلکه بهعنوان یک شاخص کلیدی برای ارزیابی توسعهیافتگی صنعتی کشورها نیز بهحساب میآید.
آهن بهطور طبیعی به شکل خالص در پوسته زمین یافت نمیشود، بلکه معمولاً بهصورت ترکیباتی نظیر هماتیت، مگنتیت و سیدریت وجود دارد. برای استخراج و فرآوری این منابع، نیاز به فرآیندهای دقیق، پرهزینه و فنی وجود دارد که طی آن سنگآهن به آهن خام تبدیل میشود. این عملیات بهوسیله روشهایی نظیر کوره بلند (Blast Furnace)، احیای مستقیم (Direct Reduction) و کوره قوس الکتریکی (Electric Arc Furnace) انجام میگیرد. هرکدام از این روشها مزایا، محدودیتها و تأثیرات زیستمحیطی خاص خود را دارند که در ادامه بهطور مفصل بررسی خواهند شد.
از سوی دیگر، تقاضای روزافزون جهانی برای فولاد خام، باعث شده تا تولید آهن خام بیش از پیش مورد توجه قرار گیرد. کشورهای صنعتی و در حال توسعه برای رشد اقتصادی خود نیاز به زیرساختهای قوی دارند و این زیرساختها بدون تولید آهن و فولاد میسر نمیشود. به همین دلیل، رقابت جهانی در زمینه تولید آهن خام، هم از منظر تکنولوژیکی و هم از نظر اقتصادی، شدت یافته است.
در کنار مباحث فنی و اقتصادی، موضوع پایداری محیطزیست نیز بهعنوان یکی از دغدغههای اصلی تولیدکنندگان مطرح است. صنایع فولاد و آهن بهعنوان یکی از منابع عمده انتشار گازهای گلخانهای شناخته میشوند. بنابراین، یافتن راهکارهایی برای تولید آهن خام به روشهای پاکتر و کمکربنتر به یک ضرورت تبدیل شده است.
در این مقاله، تلاش میشود تا فرآیندهای مختلف تولید آهن خام از دیدگاه فنی، اقتصادی و زیستمحیطی بهصورت جامع بررسی شوند. همچنین، با معرفی فناوریهای نوین، چالشها و فرصتهای پیشروی این صنعت نیز مورد تحلیل قرار خواهد گرفت. این بررسی میتواند دید جامعی از وضعیت فعلی و آینده پیشروی صنعت آهن و فولاد را در اختیار پژوهشگران، مهندسان و سیاستگذاران قرار دهد.
مروری بر منابع آهن و مواد اولیه مورد نیاز
تولید آهن خام به منابع معدنی و مواد اولیه مختلفی وابسته است. سنگآهن بهعنوان ماده اصلی، پایهگذار این فرآیند محسوب میشود. بدون وجود منابع کافی و باکیفیت از سنگآهن، هیچگونه توسعهای در صنعت فولاد امکانپذیر نخواهد بود. به همین دلیل، شناسایی، استخراج و فرآوری سنگآهن نقش کلیدی در زنجیره تأمین فولاد دارد.
انواع سنگآهن و اهمیت خلوص
سنگآهن در طبیعت بهصورت اکسیدهای آهن وجود دارد. از جمله مهمترین انواع آن میتوان به هماتیت (Fe₂O₃)، مگنتیت (Fe₃O₄) و لیمونیت اشاره کرد. این ترکیبات آهنی با خلوصهای متفاوتی یافت میشوند.
سنگآهن با خلوص بالاتر، هزینههای تولید آهن خام را کاهش میدهد. در نتیجه، کشورهایی با منابع پرعیار، از مزیت رقابتی قابلتوجهی برخوردار هستند. ایران از نظر ذخایر سنگآهن در رتبههای برتر جهانی قرار دارد، اما چالشهایی در زمینه فرآوری، حملونقل و فناوری استخراج وجود دارد.
سایر مواد اولیه کلیدی
در کنار سنگآهن، مواد دیگری نیز در فرآیند تولید آهن خام نقش دارند:
-
زغالسنگ کُکشو: یکی از مواد ضروری در روش کوره بلند که نقش عامل کاهشدهنده (Reducer) را ایفا میکند.
-
گاز طبیعی: در روش احیای مستقیم، برای تولید ترکیبات احیایی مانند هیدروژن و مونوکسیدکربن بهکار میرود.
-
آهک: بهعنوان کمکذوب (Flux)، با ناخالصیها ترکیب شده و باعث تشکیل سرباره میشود که خلوص آهن را افزایش میدهد.
-
آب صنعتی، هوای فشرده، گاز اکسیژن و نیتروژن نیز در مراحل مختلف فرآیند بهکار میروند و نیاز به طراحی دقیق دارند.
چالشهای تأمین و زیرساخت
تأمین پایدار این مواد اولیه، نقش بسیار مهمی در کاهش هزینههای تولید آهن خام دارد. وابستگی به واردات، قیمت جهانی مواد معدنی و مشکلات زیربنایی از جمله چالشهایی هستند که بسیاری از کشورها، از جمله ایران، با آن مواجهاند.
از طرفی، توسعه زیرساختهای لجستیکی مانند خطوط ریلی، بنادر معدنی و ناوگان حمل تخصصی، برای انتقال سنگآهن از معادن به واحدهای تولیدی، اهمیت زیادی دارد و میتواند به بهینهسازی زنجیره تأمین کمک کند.
تأثیر مواد اولیه بر انتخاب فناوری تولید
در نهایت، کیفیت و نوع مواد اولیه تأثیر مستقیم بر انتخاب روش تولید دارند.
برای نمونه، در مناطقی که فاقد زغالسنگ هستند، استفاده از روش احیای مستقیم با گاز طبیعی اولویت دارد. بنابراین، شناخت منابع در دسترس و طراحی فرآیند متناسب با شرایط بومی، یکی از کلیدهای موفقیت در صنعت تولید آهن خام بهشمار میرود.
روشهای تولید آهن خام
فرآیند تولید آهن خام در جهان با استفاده از روشهای گوناگون انجام میشود. انتخاب روش به عوامل متعددی مانند نوع مواد اولیه، منابع انرژی، شرایط زیستمحیطی و هزینهها بستگی دارد. سه روش اصلی برای تولید آهن خام شامل کوره بلند (Blast Furnace)، احیای مستقیم (Direct Reduction) و کوره قوس الکتریکی (Electric Arc Furnace) هستند. در این بخش، به بررسی دقیق هر یک از این روشها پرداخته میشود.
روش کوره بلند (Blast Furnace)
کوره بلند، قدیمیترین و رایجترین روش تولید آهن خام است. در این فرآیند، سنگآهن، کک (نوعی زغالسنگ خاص) و آهک بهصورت لایهلایه از بالای کوره وارد میشوند. در دمای بالا، کک بهعنوان عامل احیاکننده، اکسیژن موجود در سنگآهن را حذف کرده و آهن مذاب تولید میشود. گازهای داغ از پایین به کوره دمیده میشوند تا واکنشهای شیمیایی بهینه انجام شوند.
این روش بازدهی بالایی دارد و قابلیت تولید انبوه را فراهم میکند. اما یکی از نقاط ضعف آن، مصرف بالای انرژی و انتشار زیاد گازهای گلخانهای است. به همین دلیل، بسیاری از کشورها در تلاش هستند تا وابستگی خود به این روش را کاهش دهند.
روش احیای مستقیم (Direct Reduction)
در این روش، سنگآهن بهجای ذوب شدن، در حالت جامد و در دمای نسبتاً پایینتر با گاز طبیعی یا گازهای احیایی مورد فرآوری قرار میگیرد. خروجی این روش، آهن اسفنجی (DRI) است که در مراحل بعدی به فولاد تبدیل میشود. روش احیای مستقیم از نظر زیستمحیطی نسبت به کوره بلند برتری دارد، زیرا گازهای گلخانهای کمتری تولید میکند و مصرف انرژی آن نیز کمتر است.
در ایران، بهدلیل دسترسی گسترده به گاز طبیعی، روش DRI یکی از رایجترین روشهای تولید آهن خام محسوب میشود. این روش همچنین برای مقیاسهای متوسط مناسب بوده و نیاز به سرمایهگذاری کمتری نسبت به کوره بلند دارد.
روش کوره قوس الکتریکی (Electric Arc Furnace)
کوره قوس الکتریکی، عمدتاً برای ذوب ضایعات آهن و فولاد استفاده میشود، اما در برخی موارد از آهن اسفنجی نیز استفاده میکند. در این روش، از انرژی الکتریکی برای ذوب مواد استفاده میشود. یکی از مزایای اصلی این روش، کاهش چشمگیر آلایندهها و مصرف کمتر منابع طبیعی است.
EAF بهویژه در کشورهای پیشرفته و مناطقی با زیرساخت قوی برق، محبوبیت بالایی دارد. همچنین این روش امکان انعطافپذیری در تولید و تنظیم کیفیت محصول نهایی را فراهم میکند.
فناوریهای نوین و ترکیبی
علاوه بر روشهای کلاسیک، در سالهای اخیر فناوریهای جدیدی نظیر HIsmelt، FINEX، Corex و HYBRIT معرفی شدهاند. این روشها با هدف کاهش مصرف زغالسنگ و کربنزدایی از فرآیند تولید آهن خام طراحی شدهاند. برخی از این روشها، از هیدروژن بهعنوان عامل احیاکننده استفاده میکنند و از نظر زیستمحیطی بسیار پاکتر هستند.
در مجموع، انتخاب روش مناسب برای تولید آهن خام نیازمند تحلیل دقیق منابع در دسترس، اهداف اقتصادی و الزامات زیستمحیطی است. هر روش مزایا و محدودیتهای خاص خود را دارد و صنایع فولاد با توجه به شرایط منطقهای، یکی یا ترکیبی از این روشها را انتخاب میکنند.
مقایسه فنی فرآیندهای تولید آهن خام
انتخاب روش مناسب برای تولید آهن خام به تحلیل دقیق ویژگیهای فنی هر فرآیند وابسته است. این مقایسه شامل عوامل کلیدی مانند بازده انرژی، راندمان حرارتی، مصرف مواد اولیه، کیفیت آهن تولیدی و قابلیت مقیاسپذیری است. بررسی این شاخصها به مهندسان و تصمیمگیران کمک میکند تا کاراترین و بهصرفهترین روش را برای واحد تولیدی خود انتخاب کنند.
راندمان انرژی و حرارتی
کوره بلند به دلیل استفاده از سوخت فسیلی مانند کک، مصرف انرژی بسیار بالایی دارد. با این حال، راندمان حرارتی این سیستم بالا بوده و قابلیت تولید پیوسته دارد. در مقابل، روش احیای مستقیم با گاز طبیعی، مصرف انرژی کمتری نسبت به کوره بلند دارد و بهویژه در مناطقی با منابع گاز فراوان، اقتصادیتر محسوب میشود.
کوره قوس الکتریکی (EAF) از برق برای ذوب آهن استفاده میکند. این روش در صورت تأمین انرژی از منابع تجدیدپذیر، گزینهای پایدار و پاک محسوب میشود. EAF برای بازیافت ضایعات آهن ایدهآل است و نیاز به مصرف سنگآهن خام ندارد، که این مسئله مصرف انرژی و منابع طبیعی را کاهش میدهد.
مصرف و نوع مواد اولیه
در روش کوره بلند، استفاده از سنگآهن دانهبندیشده، کک و آهک ضروری است. این ترکیب سبب پیچیدگی در آمادهسازی مواد اولیه میشود. در مقابل، روش احیای مستقیم معمولاً از گندله سنگآهن (Pellet) استفاده میکند که نیازمند فرآوری اولیه است اما در نهایت مصرف کک را حذف میکند.
روش EAF بیشتر بر پایه ضایعات فلزی استوار است. البته در ایران و برخی کشورهای دیگر، آهن اسفنجی نیز به عنوان خوراک در EAF بهکار میرود. استفاده از DRI در EAF میتواند کیفیت فولاد تولیدی را افزایش دهد.
کیفیت محصول نهایی
محصول خروجی از کوره بلند معمولاً آهن مذاب با خلوص بالا است. این ماده در فرآیند کنورتور تبدیل به فولاد میشود. آهن اسفنجی تولید شده در روش DRI، بهدلیل حضور مقداری ناخالصی، نیازمند پالایش در کوره قوس الکتریکی یا کوره القایی است. با این حال، ترکیب مناسب DRI با ضایعات فلزی، کیفیت خوبی از فولاد را حاصل میکند.
EAF بهتنهایی توانایی تنظیم دقیق ترکیب شیمیایی فولاد را دارد. به همین دلیل، برای تولید فولادهای آلیاژی و خاص نیز مناسب است.
مقیاسپذیری و انعطاف در تولید
کوره بلند معمولاً نیازمند سرمایهگذاری سنگین و زیرساختهای صنعتی بزرگ است. راهاندازی این نوع واحدها زمانبر بوده و انعطافپذیری کمتری نسبت به سایر روشها دارد. در مقابل، DRI و EAF قابلیت اجرا در مقیاسهای کوچکتر و با هزینه کمتر را دارند. این ویژگی، روشهای نوین را برای کشورهایی با منابع محدودتر جذاب میکند.
در جمعبندی این بخش، میتوان گفت هر یک از روشهای تولید آهن خام ویژگیهای فنی خاص خود را دارند. کوره بلند مناسب تولید انبوه، DRI مناسب مناطق دارای گاز، و EAF گزینهای مطلوب برای بازیافت و تولید انعطافپذیر است. با توجه به پیشرفت فناوری، ترکیب هوشمندانه این روشها، میتواند به بهرهوری بیشتر، کاهش آلایندهها و تولید پایدارتر منجر شود.
تحلیل اقتصادی تولید آهن خام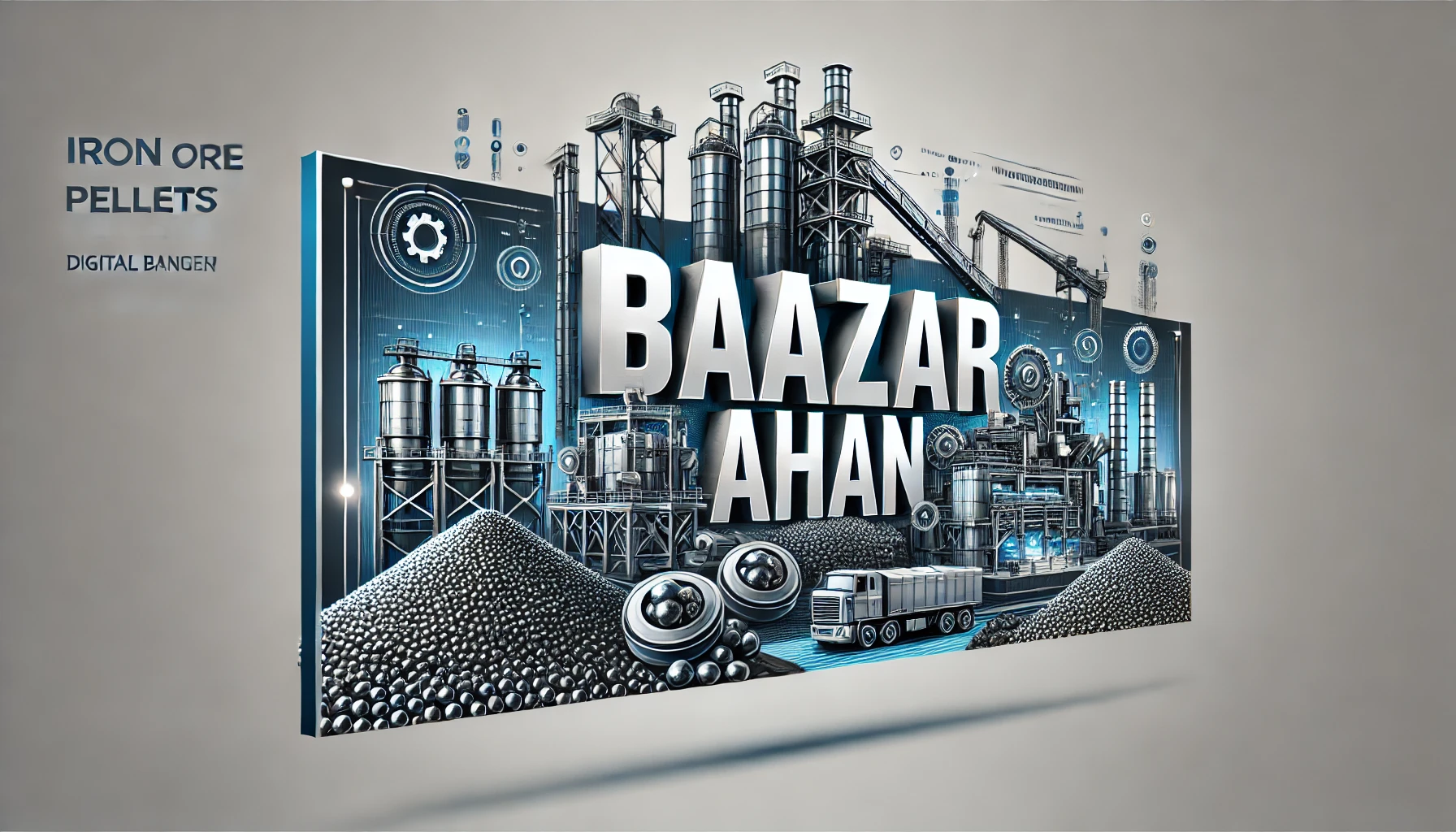
تولید آهن خام، علاوه بر جنبههای فنی، بهشدت تحت تأثیر عوامل اقتصادی قرار دارد. این فرآیند، بهدلیل مصرف بالا از انرژی، مواد اولیه و زیرساختهای صنعتی، هزینهبر است و باید همواره از نظر صرفه اقتصادی مورد ارزیابی دقیق قرار گیرد. کشورها برای باقیماندن در رقابت جهانی، نیاز دارند روشهای تولید خود را با حداقل هزینه و حداکثر بازده اقتصادی اجرا کنند.
هزینه سرمایهگذاری اولیه
یکی از مهمترین معیارهای اقتصادی در تولید آهن خام، میزان سرمایهگذاری اولیه برای احداث واحدهای تولیدی است. روش کوره بلند نیاز به تأسیسات عظیم، تجهیزات پیشرفته و خطوط پیوسته دارد. ساخت یک واحد کوره بلند ممکن است میلیاردها دلار هزینه داشته باشد و زمان راهاندازی آن نیز چندین سال طول بکشد.
در مقابل، احداث واحدهای احیای مستقیم و کوره قوس الکتریکی، سرمایهگذاری کمتری میطلبد. این واحدها در مقیاسهای کوچک و متوسط نیز قابلاجرا هستند و زمان راهاندازی آنها کوتاهتر است. از این رو، کشورهایی با منابع محدودتر یا اهداف توسعهای سریعتر، ترجیح میدهند از روشهای احیای مستقیم و قوس الکتریکی استفاده کنند.
هزینههای عملیاتی و بهرهبرداری
در تولید آهن خام، هزینههای جاری از جمله مصرف انرژی، قیمت مواد اولیه، هزینه نیروی انسانی و نگهداری تجهیزات بسیار حائز اهمیت است. در روش کوره بلند، هزینه تأمین کک، انرژی گرمایی و تعمیرات بالا است. همچنین، به نیروی انسانی متخصص و گستردهای نیاز دارد.
در روش DRI، گاز طبیعی بهعنوان عامل احیاکننده استفاده میشود که در کشورهایی با دسترسی به گاز ارزان، مانند ایران، مزیت اقتصادی محسوب میشود. اما در مناطق فاقد منابع گازی، این روش از نظر اقتصادی مقرونبهصرفه نیست.
روش EAF اگرچه در مصرف انرژی برق بسیار وابسته است، اما با بهرهگیری از ضایعات فلزی، هزینه مواد اولیه را بهشدت کاهش میدهد. همچنین، امکان بهرهگیری از برق ارزان تولیدشده از منابع تجدیدپذیر، جذابیت اقتصادی این روش را در آینده افزایش میدهد.
تحلیل بازار و قیمتگذاری
قیمت جهانی آهن خام و فولاد، تحت تأثیر عوامل بینالمللی مانند قیمت سنگآهن، زغالسنگ، نرخ ارز، تعرفهها و تحریمها قرار دارد. کشورهایی که قادر به صادرات فولاد با قیمت رقابتی هستند، معمولاً از نظر ساختار هزینهای بهینه عمل کردهاند.
همچنین، ثبات سیاسی، دسترسی به بنادر صادراتی، تسهیلات مالی و سیاستهای حمایتی دولت از جمله فاکتورهایی هستند که بر هزینه نهایی تولید آهن خام تأثیر میگذارند. ایران با وجود دارا بودن ذخایر سنگآهن و انرژی ارزان، هنوز با چالشهایی مانند ضعف در لجستیک صادرات و نوسانات ارزی مواجه است.
بازگشت سرمایه و پایداری مالی
برای تولیدکنندگان آهن خام، نرخ بازگشت سرمایه (ROI) یکی از شاخصهای مهم است. اگرچه سرمایهگذاری اولیه در برخی روشها سنگین است، اما تولید پایدار و با تیراژ بالا میتواند به بازگشت سرمایه مناسب منجر شود. استفاده بهینه از فناوری، کاهش اتلاف انرژی و بهرهوری عملیاتی، ابزارهایی هستند که به بهبود وضعیت مالی کارخانهها کمک میکنند.
در نهایت، تحلیل اقتصادی تولید آهن خام باید همزمان عوامل هزینه، ظرفیت تولید، منابع انرژی، بازار فروش و سیاستگذاریهای کلان را در نظر بگیرد. بدون ارزیابی دقیق اقتصادی، هیچ روش تولیدی نمیتواند پایدار بماند، حتی اگر از نظر فنی برتر باشد.
تحلیل زیستمحیطی فرآیندهای تولید آهن خام
تولید آهن خام از جمله صنایعی است که تأثیر چشمگیری بر محیط زیست دارد. انتشار گازهای گلخانهای، مصرف بالای انرژی، تولید پسماندهای صنعتی و تخریب منابع طبیعی، تنها بخشی از پیامدهای این صنعت هستند. با توجه به بحرانهای زیستمحیطی در سطح جهان، ارزیابی دقیق اثرات فرآیندهای مختلف تولید آهن خام ضروری است.
انتشار گازهای گلخانهای
روش کوره بلند بیشترین میزان انتشار CO₂ را در بین روشهای تولید آهن خام دارد. در این فرآیند، سوزاندن کک و واکنشهای شیمیایی با سنگآهن باعث تولید حجم بالایی از دیاکسیدکربن میشود. بر اساس آمار بینالمللی، بیش از ۷۰٪ از کل گازهای گلخانهای صنعت فولاد از کورههای بلند ناشی میشوند.
در مقابل، روش احیای مستقیم، بهویژه با گاز طبیعی، انتشار کربن کمتری دارد. در این روش، هیدروژن و مونوکسیدکربن موجود در گاز طبیعی نقش احیاکننده دارند و میزان گازهای آلاینده نسبت به کوره بلند کمتر است. با این حال، اگر گاز طبیعی از منابع فسیلی تأمین شود، همچنان اثر زیستمحیطی قابل توجهی دارد.
کوره قوس الکتریکی نیز بهخودیخود آلایندگی مستقیم ندارد، اما میزان پاکی آن به منبع تولید برق وابسته است. در صورتی که برق از نیروگاههای زغالسوز تأمین شود، ردپای کربن این روش نیز افزایش مییابد. با این حال، استفاده از برق تجدیدپذیر، این روش را به یکی از پاکترین گزینهها در تولید آهن خام تبدیل میکند.
مصرف منابع طبیعی و آب
کوره بلند نیاز به منابع عظیمی از زغالسنگ، سنگآهن و آهک دارد. استخراج این مواد، به تخریب منابع طبیعی و فرسایش زمین منجر میشود. همچنین، این فرآیند مصرف بالای آب صنعتی دارد. خنکسازی کورهها، شستوشوی گازها و مدیریت سرباره، همگی نیازمند آب با کیفیت صنعتی هستند.
روشهای DRI و EAF در مقایسه با کوره بلند، مصرف آب و منابع طبیعی کمتری دارند. بهویژه، در روش قوس الکتریکی، با استفاده از ضایعات فلزی، از نیاز به استخراج سنگآهن جدید کاسته میشود. این موضوع به کاهش فشار بر منابع طبیعی کمک میکند.
مدیریت پسماندهای صنعتی
در فرآیند تولید آهن خام، پسماندهایی مانند گرد و غبار کوره، گلهای اسیدی، سرباره و گازهای سمی تولید میشوند. اگر این پسماندها بهدرستی مدیریت نشوند، میتوانند به خاک، هوا و منابع آب آسیب جدی وارد کنند. در روش کوره بلند، سرباره حجم بالایی دارد که باید بازیافت یا دفن شود.
روش DRI و EAF پسماند کمتری تولید میکنند و مدیریت آن سادهتر است. برخی کشورها از سرباره و پسماندها در صنعت سیمان و راهسازی استفاده میکنند. این کار، علاوه بر کاهش آلودگی، به صرفهجویی در منابع معدنی نیز کمک میکند.
فناوریهای سبز و آینده پایدار
در سالهای اخیر، سرمایهگذاری در فناوریهای پاک در صنعت تولید آهن خام افزایش یافته است. پروژههایی مانند HYBRIT در سوئد، با استفاده از هیدروژن بهعنوان احیاکننده، تولید آهن بدون کربن را ممکن کردهاند. همچنین، فناوریهایی نظیر FINEX و COREX بهدنبال حذف کامل کوره بلند از زنجیره تولید هستند.
در کنار آن، مفاهیم اقتصاد چرخشی (Circular Economy) و بازیافت ضایعات آهن، نقش مهمی در کاهش اثرات زیستمحیطی دارند. استفاده دوباره از فلزات، انرژی و پسماندها میتواند مسیر تولید آهن خام را به سمت پایداری سوق دهد.
در نهایت، باید گفت که پایداری زیستمحیطی در تولید آهن خام تنها از طریق تغییر در فناوری و الگوی مصرف منابع قابل دستیابی است. کشورهای پیشرو، همزمان با رشد اقتصادی، به سمت کاهش اثرات منفی زیستمحیطی حرکت کردهاند. آینده این صنعت، در گرو ترکیب کارایی فنی و حساسیت زیستمحیطی خواهد بود.
جمعبندی و چشمانداز آینده تولید آهن خام
تولید آهن خام، یکی از پایههای کلیدی در زنجیره ارزش صنایع فلزی و فولادی محسوب میشود. این فرآیند، نقش حیاتی در توسعه اقتصادی، صنعتی و زیرساختی کشورها دارد. با این حال، چالشهایی نظیر مصرف بالای انرژی، انتشار آلایندههای زیستمحیطی و نوسانات بازار جهانی، صنایع فولاد را وادار به تحول اساسی کردهاند.
مقایسه روشهای تولید
در طول این مقاله، سه روش اصلی تولید آهن خام شامل کوره بلند، احیای مستقیم و کوره قوس الکتریکی بررسی شدند. هر یک از این روشها نقاط قوت و ضعف خاص خود را دارند:
-
کوره بلند برای تولید انبوه با راندمان بالا مناسب است، اما آلودگی زیادی تولید میکند.
-
در مقابل، احیای مستقیم و EAF، روشهایی نوینتر، کممصرفتر و با تأثیرات زیستمحیطی کمتر هستند.
-
بهویژه، ترکیب DRI و قوس الکتریکی، مسیر غالب آینده برای تولید پایدارتر آهن خام به شمار میآید.
عوامل اقتصادی تأثیرگذار
از منظر اقتصادی، کشورهای موفق در تولید آهن خام، آنهایی هستند که توانستهاند بین سرمایهگذاری اولیه، هزینههای عملیاتی و ظرفیت صادرات توازن برقرار کنند. استفاده از منابع انرژی بومی، توسعه زیرساختها، و دسترسی به فناوریهای نوین از مهمترین عوامل مزیت رقابتی در این حوزه به شمار میروند.
حرکت به سمت تولید سبز
از نظر زیستمحیطی، فشار نهادهای بینالمللی، قوانین سختگیرانه و آگاهی عمومی باعث شده تولیدکنندگان به سمت روشهای سبز حرکت کنند. پروژههای نوآورانه با محوریت هیدروژن، انرژی تجدیدپذیر و اقتصاد چرخشی، آیندهای کمکربن را برای صنعت آهن و فولاد ترسیم میکنند.
آینده صنعت آهن خام
در افق آینده، ترکیبی از فناوریهای پاک، دیجیتالسازی، هوش مصنوعی در کنترل فرآیندها، و سیاستگذاری هوشمندانه میتواند صنعت تولید آهن خام را به مرحلهای تازه برساند. کشورهایی که بتوانند زودتر خود را با این تغییرات همراستا کنند، در بازار جهانی جایگاه مستحکمی خواهند داشت.
نتیجهگیری نهایی
میتوان نتیجه گرفت که موفقیت در تولید آهن خام، نیازمند نگاه جامع است. این موفقیت نه تنها به انتخاب فناوری مناسب، بلکه به مدیریت صحیح منابع، بهرهوری اقتصادی و تعهد به اصول توسعه پایدار بستگی دارد. آینده این صنعت به تصمیمهای امروز وابسته است، تصمیمهایی که میتوانند نسلهای آینده را از نظر اقتصادی، زیستمحیطی و صنعتی بیمه کنند.