بررسی جامع کوره کنورتور اکسیژنی: فناوری کلیدی در تولید فولاد با کیفیت و بهرهوری بالا
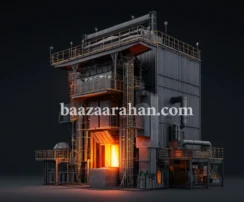
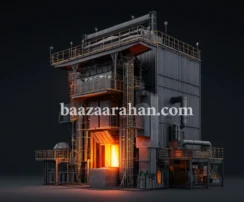
کوره کنورتور اکسیژنی چیست؟
کوره کنورتور اکسیژنی (Basic Oxygen Furnace یا BOF) یکی از مهمترین تجهیزات در صنعت فولادسازی است. این کوره وظیفه دارد چدن مذاب را به فولاد تبدیل کند. فرآیند BOF با دمیدن اکسیژن خالص به داخل چدن مذاب انجام میشود. در این فرآیند، ناخالصیهای چدن مانند کربن، سیلیس، منگنز و فسفر با اکسیژن واکنش میدهند. در نتیجه این واکنشها، این عناصر به گاز یا سرباره تبدیل میشوند و فولادی با ترکیب شیمیایی مناسب به دست میآید.
کوره BOF در دهه ۱۹۵۰ میلادی به صنعت فولاد معرفی شد. این فناوری نسبت به روشهای قدیمیتر مانند روش باز آتش بلند (Open Hearth Furnace) بسیار کارآمدتر است. امروزه بیش از ۶۰ درصد فولاد جهان به کمک کوره کنورتور اکسیژنی تولید میشود.
ساختار BOF شامل یک بدنه فولادی بزرگ با پوشش نسوز داخلی است. در بالای کوره، یک لانس یا نازل تعبیه شده که از طریق آن اکسیژن با فشار بالا به سطح چدن مذاب دمیده میشود. فرآیند دمش معمولاً بین ۱۵ تا ۲۰ دقیقه طول میکشد. در پایان این مرحله، فولاد مذاب با کیفیت مطلوب به دست میآید.
کوره کنورتور اکسیژنی مزایای فراوانی دارد. از جمله تولید سریع، مصرف انرژی پایین و امکان بازیافت قراضه فولادی. البته این فناوری چالشهایی هم دارد، مانند تولید گازهای گلخانهای. با این حال، BOF همچنان یک فناوری کلیدی در زنجیره جهانی فولادسازی به شمار میرود.
کوره BOF در زنجیره تولید فولاد
کوره کنورتور اکسیژنی (BOF) نقش کلیدی در زنجیره تولید فولاد ایفا میکند. این کوره مرحلهای حیاتی در تبدیل چدن خام به فولاد قابلاستفاده است. برای درک بهتر جایگاه BOF، ابتدا باید کل زنجیره فولادسازی را مرور کنیم.
فرآیند تولید فولاد از معدن سنگآهن آغاز میشود. سنگآهن در کوره بلند به چدن مذاب تبدیل میشود. این چدن، اگر به همان صورت استفاده شود، بسیار شکننده و دارای درصد بالای کربن است. در اینجا کوره کنورتور اکسیژنی وارد عمل میشود. چدن مذاب مستقیماً به داخل کنورتور BOF منتقل میشود. در این مرحله، اکسیژن با فشار بالا به داخل مذاب دمیده میشود. هدف این فرآیند، کاهش درصد کربن و حذف سایر ناخالصیها است.
پس از پایان این مرحله، فولاد مذاب با ترکیب شیمیایی مناسب به دست میآید. این فولاد سپس وارد فرآیند ریختهگری میشود تا به شکل شمش، اسلب یا سایر محصولات نیمهساخته درآید. در ادامه، این محصولات در واحد نورد به ورق، میلگرد یا مقاطع فولادی مختلف تبدیل میشوند.
جایگاه کوره کنورتور اکسیژنی در زنجیره تولید فولاد بسیار مهم است، زیرا کیفیت نهایی فولاد تا حد زیادی به عملکرد این کوره وابسته است. نکته جالب اینجاست که در سالهای اخیر، بسیاری از کشورها به دنبال بهینهسازی عملکرد BOF برای کاهش مصرف انرژی و کاهش انتشار CO₂ هستند.
در مقایسه با کوره قوس الکتریکی (EAF)، BOF بیشتر برای تولید فولاد از مواد خام تازه (چدن مذاب) به کار میرود. در حالی که کوره قوس الکتریکی EAF برای ذوب قراضه فولادی مناسبتر است. با این حال، در کشورهایی با منابع غنی سنگآهن، BOF همچنان فناوری غالب است.
اجزای اصلی کوره کنورتور اکسیژنی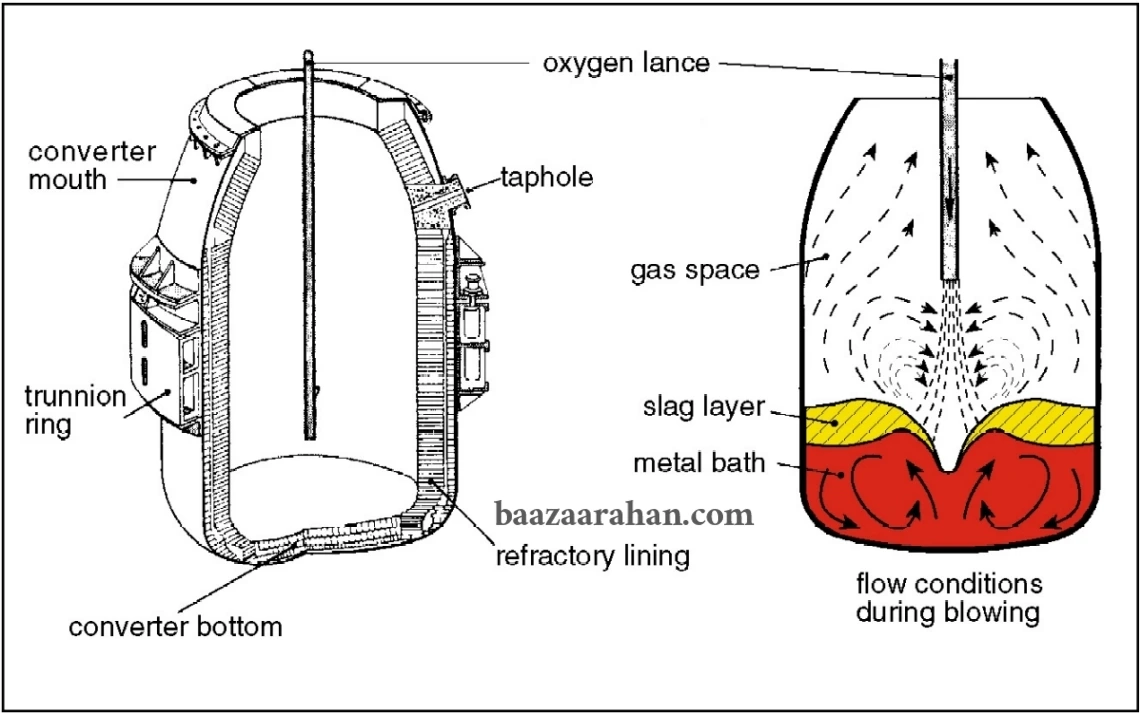
کوره کنورتور اکسیژنی (BOF) از بخشهای مختلفی تشکیل شده است که هر کدام نقش حیاتی در عملکرد آن دارند. شناخت این اجزا به درک بهتر فرآیند فولادسازی کمک میکند.
بدنه اصلی BOF از فولاد مقاوم ساخته میشود. این بدنه به شکل یک ظرف عظیم است که میتواند چرخش کند. چرخش کوره باعث میشود عملیات شارژ مواد اولیه و تخلیه فولاد مذاب بهراحتی انجام شود.
درون بدنه، آستر نسوز قرار دارد. این آستر از مواد سرامیکی خاصی ساخته میشود که در برابر دماهای بالا و واکنشهای شیمیایی مقاومت دارند. آستر نسوز بهطور منظم تعویض میشود تا از آسیب به بدنه کوره جلوگیری شود.
در بالای کوره کنورتور اکسیژنی یک لانس یا نازل تزریق اکسیژن نصب شده است. این لانس، اکسیژن خالص را با سرعت بسیار بالا به داخل چدن مذاب میدمد. طراحی دقیق لانس برای ایجاد اختلاط مناسب بین اکسیژن و مذاب بسیار مهم است.
علاوه بر لانس، سیستمهای جانبی مختلفی در BOF وجود دارند. سیستم خنککننده برای جلوگیری از داغ شدن بیش از حد لانس به کار میرود. همچنین سیستمهای کنترلی و حسگرها، پارامترهای کلیدی مانند دما، ترکیب شیمیایی و میزان اکسیژن را پایش میکنند.
برخی BOFها به مشعلهای کمکی نیز مجهز هستند. این مشعلها در مراحل اولیه فرآیند به گرم نگه داشتن مذاب کمک میکنند.
به طور کلی، هماهنگی دقیق بین اجزای مختلف کوره کنورتور اکسیژنی باعث میشود این فناوری بتواند فولادی با کیفیت و در حجم بالا تولید کند. مهندسان همواره در حال بهبود طراحی این اجزا برای افزایش بهرهوری و کاهش مصرف انرژی هستند.
مواد اولیه در کوره
BOF
عملکرد موفق کوره کنورتور اکسیژنی به انتخاب و مدیریت صحیح مواد اولیه بستگی دارد. این مواد نهتنها بر کیفیت فولاد نهایی تأثیر میگذارند، بلکه بر مصرف انرژی و میزان آلایندگی هم اثر دارند.
ماده اصلی در این فرآیند چدن مذاب است. چدن از ذوب سنگآهن در کوره بلند به دست میآید. این فلز مذاب دارای درصد بالایی از کربن و سایر ناخالصیها است که باید طی فرآیند BOF حذف شوند.
علاوه بر چدن، قراضه فولادی نیز به کوره اضافه میشود. قراضهها میتوانند از منابع داخلی یا خارجی تأمین شوند. افزودن قراضه به BOF چند مزیت دارد: کاهش مصرف چدن، صرفهجویی در انرژی و کمک به بازیافت فلزات. البته کیفیت قراضه اهمیت زیادی دارد؛ قراضههای آلوده میتوانند باعث مشکلات در فرآیند شوند.
فلاکسها دسته دیگری از مواد اولیه هستند. مهمترین فلاکسها شامل آهک (CaO) و دولومیت (CaMg(CO₃)₂) هستند. این مواد در کوره به سرباره تبدیل میشوند. سرباره، ناخالصیهایی مانند سیلیس، فسفر و گوگرد را جذب میکند. کنترل ترکیب و میزان فلاکسها برای بهبود کیفیت فولاد نهایی بسیار حیاتی است.
برخی افزودنیهای دیگر نیز گاه به کوره کنورتور اکسیژنی اضافه میشوند. این افزودنیها شامل فروآلیاژها (مانند فرومنگنز یا فروسیلیکون) هستند. آنها برای تنظیم دقیق ترکیب شیمیایی فولاد استفاده میشوند.
در مجموع، مدیریت دقیق مواد اولیه در BOF یک هنر و یک علم است. مهندسان با تنظیم دقیق نسبت این مواد، میتوانند فولادی با خواص مطلوب و هزینه تولید بهینه بسازند.
فرآیند تولید فولاد در کوره BOF
فرآیند تولید فولاد در کوره کنورتور اکسیژنی (BOF) با دقت و نظم بالا انجام میشود. این فرآیند از شارژ مواد اولیه آغاز میشود و با تخلیه فولاد مذاب پایان مییابد.
ابتدا، چدن مذاب از کوره بلند به BOF منتقل میشود. همزمان، مقدار مشخصی قراضه فولادی به کوره اضافه میشود. این مرحله باعث کاهش دمای کلی و بهبود بهرهوری انرژی میشود.
پس از شارژ مواد، لانس اکسیژن به درون کوره هدایت میشود. اکسیژن خالص با فشار بسیار بالا (معمولاً بین ۱۰ تا ۱۵ بار) به سطح چدن مذاب دمیده میشود. این دمش اکسیژن باعث بروز واکنشهای شیمیایی شدید میشود. کربن با اکسیژن واکنش میدهد و به گاز CO و CO₂ تبدیل میشود. به موازات آن، عناصر دیگر مانند سیلیس، منگنز، فسفر و گوگرد نیز اکسید میشوند.
این واکنشها حرارت زیادی تولید میکنند. در نتیجه، دمای مذاب به حدود ۱۶۰۰ تا ۱۷۰۰ درجه سانتیگراد میرسد. همزمان، سرباره در سطح مذاب تشکیل میشود و ناخالصیها را به دام میاندازد.
فرآیند دمش معمولاً بین ۱۵ تا ۲۰ دقیقه طول میکشد. در طول این زمان، مهندسان با استفاده از حسگرها و نمونهگیریهای لحظهای، کیفیت فولاد در حال تولید را کنترل میکنند.
پس از تکمیل دمش، لانس اکسیژن خارج میشود. سپس کوره به آرامی چرخانده میشود تا فولاد مذاب به درون پاتیل ریخته شود. سرباره نیز بهطور جداگانه تخلیه میشود.
در نهایت، فولاد مذاب به واحد متالورژی ثانویه یا مستقیم به ریختهگری مداوم منتقل میشود. فرآیند کوره کنورتور اکسیژنی با این مرحله به پایان میرسد. این فرآیند کوتاه اما پرانرژی، ستون فقرات تولید فولاد مدرن به شمار میآید.
کنترل کیفیت در فرآیند BOF
کنترل کیفیت در کوره کنورتور اکسیژنی (BOF) نقش حیاتی در تضمین خواص مطلوب فولاد نهایی ایفا میکند. در این فرآیند پرسرعت، هر لحظه اهمیت دارد و هر خطا میتواند به کاهش کیفیت یا افزایش هزینهها منجر شود.
یکی از مهمترین فاکتورها در کنترل کیفیت، کنترل ترکیب شیمیایی فولاد مذاب است. در طول دمش اکسیژن، نمونههایی از مذاب به طور مرتب برداشته میشود. این نمونهها در آزمایشگاه آنالیز میشوند تا میزان عناصر باقیمانده مانند کربن، منگنز، فسفر و گوگرد مشخص شود. مهندسان با تنظیم پارامترهای فرآیند، ترکیب فولاد را به دقت در محدوده مورد نظر نگه میدارند.
کنترل دما نیز بسیار مهم است. دمای فولاد مذاب باید در بازهای مشخص باقی بماند تا برای فرآیندهای بعدی مناسب باشد. اگر دما بیش از حد بالا یا پایین رود، مشکلاتی در ریختهگری یا خواص مکانیکی محصول نهایی به وجود میآید. برای پایش دما از حسگرهای حرارتی دقیق استفاده میشود.
علاوه بر این، کنترل سرباره بخش مهمی از تضمین کیفیت است. سرباره باید به طور کامل ناخالصیها را جذب کند. ترکیب، دما و ویسکوزیته سرباره به دقت کنترل میشود تا به حداکثر کارایی برسد.
امروزه در بسیاری از کارخانهها، سیستمهای اتوماسیون پیشرفته به BOF افزوده شدهاند. این سیستمها با استفاده از هوش مصنوعی، فرآیند را بهینهسازی میکنند. آنها دادههای لحظهای را تحلیل میکنند و به اپراتورها کمک میکنند تصمیمهای دقیقتری بگیرند.
به طور کلی، کوره کنورتور اکسیژنی با فرآیند کنترل کیفیت دقیق، میتواند فولادی با خواص فیزیکی و شیمیایی یکنواخت تولید کند. این امر برای صنایع حساس مانند خودروسازی و ساختمانسازی اهمیت ویژهای دارد.
مزایا و معایب استفاده از BOF
کوره کنورتور اکسیژنی (BOF) همچنان یکی از فناوریهای اصلی در صنعت فولادسازی است. این فناوری مزایای قابلتوجهی دارد اما بدون چالش هم نیست. شناخت دقیق این مزایا و معایب، به مدیران و مهندسان کمک میکند تصمیمات بهتری بگیرند.
مزایا:
۱. ظرفیت تولید بالا
BOF میتواند در هر بار فرآیند، بین ۱۰۰ تا ۳۰۰ تن فولاد مذاب تولید کند. این حجم بالا، آن را برای تولید انبوه مناسب میسازد.
-
زمان فرآیند کوتاه
کل فرآیند در BOF، از شارژ تا تخلیه، معمولاً بین ۳۰ تا ۴۵ دقیقه طول میکشد. این سرعت بالا، بهرهوری خطوط تولید را افزایش میدهد. -
بهرهوری انرژی
واکنشهای اکسایش در BOF حرارت زیادی تولید میکنند که به ادامه فرآیند کمک میکند. در نتیجه، مصرف سوختهای کمکی نسبتاً پایین است. -
امکان استفاده از قراضه
BOF بهخوبی با قراضه فولادی کار میکند. این موضوع به صرفهجویی در منابع طبیعی و انرژی کمک میکند.
معایب:
-
انتشار CO₂ بالا
فرآیند BOF مقدار قابلتوجهی دیاکسید کربن تولید میکند. این مسأله با اهداف جهانی کاهش گازهای گلخانهای در تضاد است. -
نیاز به چدن مذاب
BOF برای کارکرد به چدن مذاب از کوره بلند نیاز دارد. این وابستگی، انعطافپذیری فرآیند را کاهش میدهد. -
نیاز به سرمایهگذاری بالا
ساخت و نگهداری BOF پرهزینه است. همچنین زیرساختهای جانبی (کوره بلند، تأسیسات اکسیژن و…) ضروری هستند. -
محدودیت در استفاده از قراضه زیاد
در مقایسه با کوره قوس الکتریکی (EAF)، BOF نمیتواند درصد بسیار بالایی از قراضه را استفاده کند.
با این وجود، کوره کنورتور اکسیژنی همچنان در بسیاری از کشورها، بهویژه در تولید فولادهای اولیه و با حجم بالا، یک فناوری استاندارد محسوب میشود.
آینده کورههای کنورتور اکسیژنی در صنعت فولاد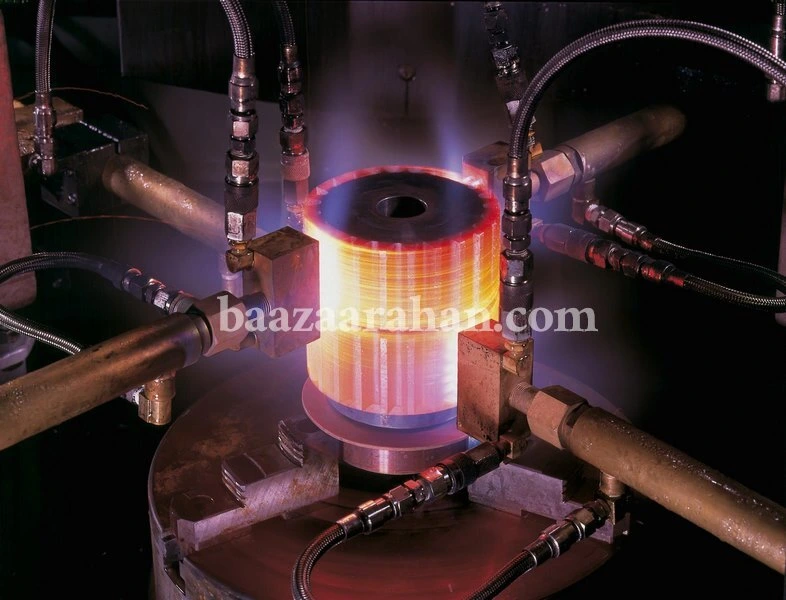
کوره کنورتور اکسیژنی یا BOF همچنان یکی از پایههای اصلی تولید فولاد در جهان است. اما با توجه به چالشهای زیستمحیطی و نیاز به افزایش بهرهوری، آینده این فناوری با تغییرات مهمی همراه خواهد بود.
یکی از محورهای اصلی تحقیق و توسعه در این حوزه، کاهش انتشار گازهای گلخانهای است. شرکتهای بزرگی مثل ArcelorMittal و Tata Steel پروژههایی برای بهبود کارایی BOF و کاهش دیاکسید کربن آغاز کردهاند. این پروژهها شامل بهکارگیری فناوریهای جدید مثل دمش اکسیژن بهینه، بازیابی حرارت و استفاده از انرژیهای تجدیدپذیر در تأسیسات هستند.
از طرف دیگر، تکنولوژیهای مکمل مانند کوره قوس الکتریکی (EAF) و فرآیندهای تولید فولاد بدون کربن (مثل استفاده از هیدروژن به جای کربن) به تدریج در حال رشداند. اما BOF به دلیل ظرفیت تولید بالا و هزینههای نسبی پایین، هنوز نقش مهمی در زنجیره فولاد دارد.
کشورهایی مانند چین، هند و کره جنوبی که تولید فولاد بسیار بالایی دارند، همچنان سرمایهگذاری گستردهای در بهبود BOF انجام میدهند. در عین حال، استانداردهای زیستمحیطی سختگیرانهتر، فشار بر بهبود این فناوری را افزایش میدهد.
در نهایت، آینده کوره کنورتور اکسیژنی به تعامل میان نوآوریهای فناوری، مقررات زیستمحیطی و نیازهای بازار بستگی دارد. با وجود چالشها، BOF هنوز یک ستون کلیدی در صنعت فولادسازی باقی خواهد ماند.
جمعبندی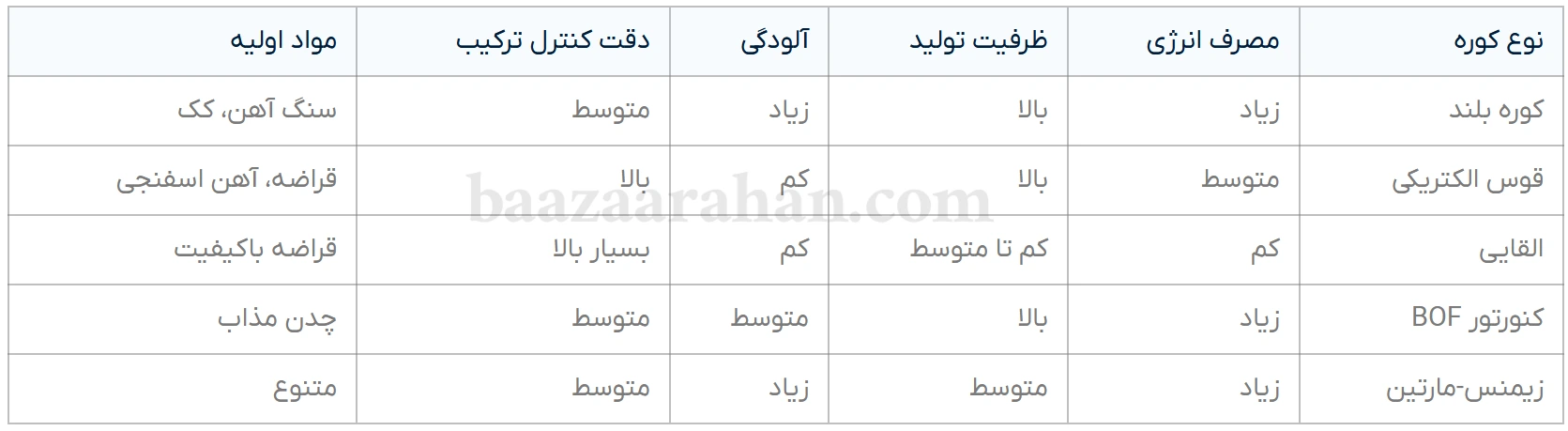
کوره کنورتور اکسیژنی (BOF) یکی از مهمترین و پرکاربردترین فناوریها در صنعت فولادسازی است. این کوره با دمیدن اکسیژن خالص به چدن مذاب، ناخالصیها را حذف کرده و فولادی با کیفیت بالا تولید میکند. ساختار خاص و اجزای کلیدی مانند لانس اکسیژن، بدنه چرخان و آستر نسوز، عملکرد بهینه این کوره را تضمین میکنند.
در زنجیره تولید فولاد، BOF نقش مرکزی دارد و با توجه به ظرفیت بالا و سرعت تولید، گزینهای اقتصادی برای تولید انبوه فولاد است. مواد اولیه اصلی شامل چدن مذاب، قراضه فولادی و فلاکسهایی مانند آهک هستند که کیفیت فولاد نهایی را شکل میدهند.
فرآیند تولید فولاد در BOF دقیق و کنترل شده است. پارامترهایی مانند ترکیب شیمیایی، دما و کیفیت سرباره به دقت پایش میشوند تا فولادی یکنواخت و با خواص مکانیکی مطلوب حاصل شود. این کنترل کیفیت، اهمیت ویژهای در صنایع حساس مانند خودروسازی و ساختمانسازی دارد.
با وجود مزایایی چون بهرهوری انرژی و سرعت بالا، BOF معایبی مانند انتشار گازهای گلخانهای و نیاز به چدن مذاب دارد. اما با پیشرفتهای فناوری و پروژههای تحقیقاتی شرکتهای بزرگ مانند ArcelorMittal و Tata Steel، آینده این فناوری روشن است و مسیر بهبود آن هموار میشود.
در نهایت، کوره کنورتور اکسیژنی به عنوان یکی از ستونهای صنعت فولاد، با نوآوریهای مستمر و تطبیق با استانداردهای زیستمحیطی، نقش کلیدی خود را در تولید فولاد پایدار و با کیفیت حفظ خواهد کرد.