بلوم در زنجیره تولید فولاد: فرآیندها، مشخصات، کاربردها و چالشها
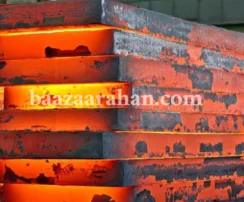
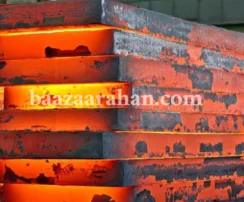
1. مقدمه
تعریف بلوم و جایگاه آن در زنجیره فولاد
بلوم (Bloom) یکی از محصولات نیمتمام در زنجیره فولاد است که به صورت مقاطع مربعی یا مستطیلی تولید میشود. این محصول در زنجیره فولاد، پس از شمش (Billet) و پیش از تولید محصولات نهایی قرار دارد. بلوم ماده اولیه مهمی برای نورد گرم و سرد محسوب میشود و به تولید انواع پروفیلها، تیرآهنها و محصولات نیمتمام کمک میکند.
اهمیت بلوم در تولید محصولات فولادی با کیفیت
کیفیت بلوم تاثیر مستقیم بر خواص مکانیکی و فیزیکی محصولات نهایی دارد. استحکام، چقرمگی و انعطافپذیری مناسب بلوم باعث میشود محصولات فولادی ساخته شده دوام و کارایی بالایی داشته باشند. همچنین، بلوم با ابعاد استاندارد، فرآیند تولید را سادهتر و هزینهها را کاهش میدهد.
هدف و دامنه بحث
هدف این مقاله، ارائه بررسی جامع درباره بلوم و نقش آن در صنعت فولاد است. دامنه بحث شامل تاریخچه تولید، انواع بلوم، مواد اولیه، فرآیندهای تولید، خواص فیزیکی و مکانیکی، کاربردها، عیوب رایج، فناوریهای نوین، مقایسه با دیگر محصولات و بررسیهای اقتصادی و زیستمحیطی میشود. این مقاله برای مهندسان، پژوهشگران و تولیدکنندگان فولاد مفید خواهد بود.
2. تاریخچه و توسعه تولید بلوم 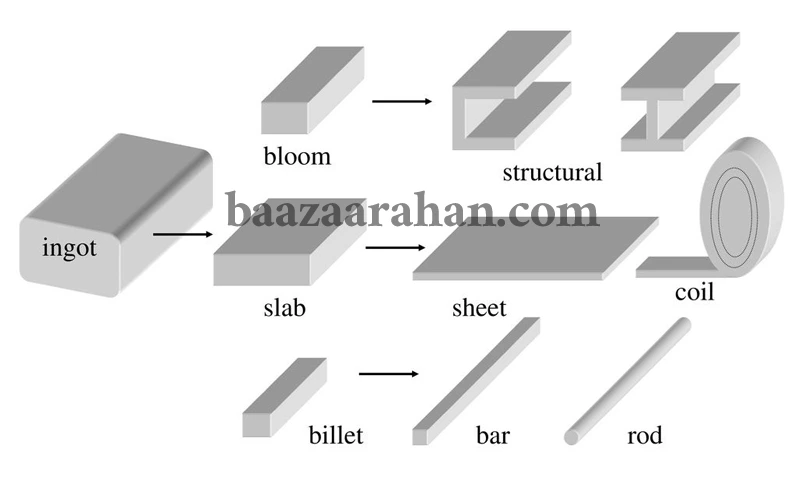
سیر تحول تولید بلوم در صنعت فولاد
تولید بلوم از دیرباز بخشی اساسی در صنعت فولاد بوده است. ابتدا بلومها به روشهای سنتی مانند ریختهگری دستی و شمشسازی تولید میشدند. این روشها زمانبر و دارای ضایعات زیاد بودند. با پیشرفت تکنولوژی، ریختهگری پیوسته (Continuous Casting) وارد صنعت شد که باعث افزایش سرعت تولید و کاهش هزینهها گردید. امروزه تولید بلوم با فناوریهای پیشرفته و کنترل دقیق کیفیت انجام میشود.
فناوریهای سنتی و مدرن در تولید بلوم
فناوریهای سنتی شامل ریختهگری دستی و نورد ساده بودند. اما فناوری مدرن شامل ریختهگری پیوسته، نورد گرم با کنترل دقیق دما و فشار، اتوماسیون خطوط تولید و استفاده از حسگرهای هوشمند است. این فناوریها باعث افزایش یکنواختی ابعاد، کاهش عیوب و بهبود خواص مکانیکی بلوم شدهاند.
روند جهانی و بازار بلوم
بازار جهانی بلوم به دلیل تقاضای بالا در صنایع ساختمانی، خودروسازی و ماشینآلات صنعتی رو به رشد است. کشورهایی مانند چین، هند، ژاپن و کره جنوبی پیشرو در تولید و صادرات بلوم هستند. روند جهانی تولید بلوم به سمت بهرهوری انرژی بالاتر، کاهش آلایندهها و توسعه آلیاژهای خاص متمایل شده است.
3. انواع بلوم در زنجیره فولاد
طبقهبندی بلوم بر اساس شکل و ابعاد
بلومها معمولاً به صورت مقاطع مربعی یا مستطیلی تولید میشوند. ابعاد بلومها متغیر است و بسته به نیاز تولیدکنندگان فولاد، اندازههای مختلفی دارد. چند نوع رایج شامل بلومهای با مقطع ۱۵×۱۵ سانتیمتر، ۲۰×۲۰ سانتیمتر و ۲۵×۲۵ سانتیمتر است. این تنوع در ابعاد به فرآیند نورد و تولید محصولات نهایی کمک میکند.
انواع بلوم بر اساس روش تولید
بلومها به چند دسته تقسیم میشوند که مهمترین آنها عبارتند از: بلوم ریختهگری پیوسته (Continuous Casting Bloom)، بلوم ریختهگری مداوم (Semi-Continuous Bloom) و بلوم نورد گرم (Hot Rolled Bloom). بلوم ریختهگری پیوسته امروزه رایجترین نوع است که کیفیت بالا و ضایعات کم دارد. بلوم نورد گرم بیشتر برای تغییر شکل و بهبود خواص مکانیکی استفاده میشود.
بلومهای ویژه و با کاربردهای خاص
در صنعت فولاد، بلومهای آلیاژی (Alloyed Bloom)، بلومهای ضدزنگ (Stainless Bloom) و بلومهای کمکربن (Low Carbon Bloom) کاربردهای خاصی دارند. این بلومها برای تولید قطعات با خواص ویژه مانند مقاومت به خوردگی، سختی بالا یا انعطافپذیری بیشتر طراحی شدهاند. استفاده از این انواع بلوم به بهبود کیفیت و عملکرد محصولات نهایی کمک میکند.
4. مواد اولیه و ترکیب شیمیایی بلوم 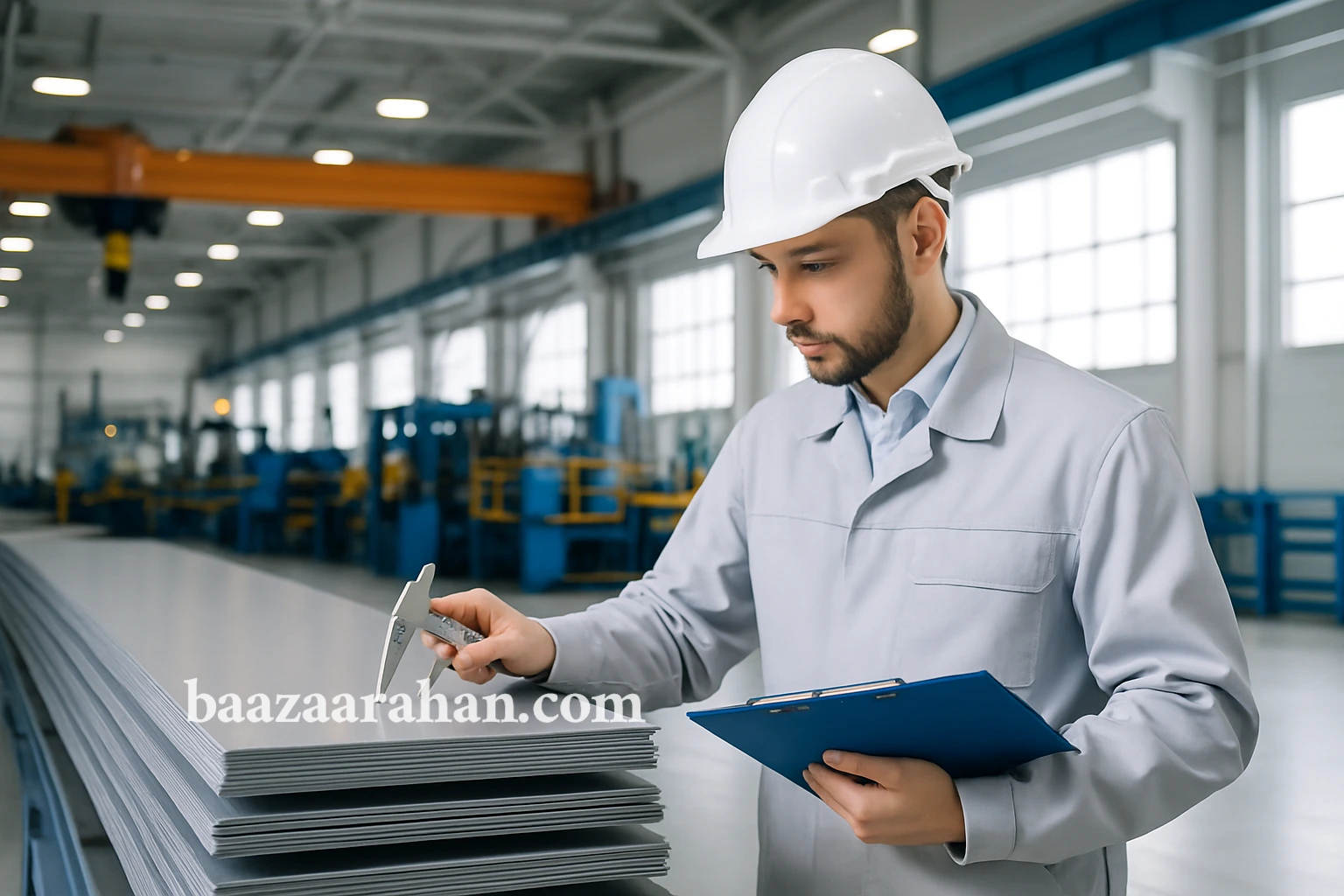
انواع مواد اولیه (شمش، اسلب، قراضه) برای تولید بلوم
تولید بلوم در زنجیره فولاد به مواد اولیه متنوعی نیاز دارد که مهمترین آنها شامل شمش (Billet)، اسلب (Slab) و قراضه (Scrap) است. شمشها عموماً به عنوان مواد پایه استفاده میشوند و کیفیت بالایی دارند. اسلبها بیشتر برای تولید محصولات تخت کاربرد دارند اما در برخی موارد در تولید بلوم هم استفاده میشوند. قراضه فولادی نیز به عنوان منبع بازیافت، بهبود هزینهها و حفظ منابع طبیعی اهمیت دارد.
تاثیر ترکیب شیمیایی بر خواص مکانیکی و فیزیکی بلوم
ترکیب شیمیایی مواد اولیه نقش تعیینکنندهای در خواص بلوم دارد. عناصر اصلی شامل کربن، منگنز، سیلیکون، فسفر و گوگرد هستند. کربن تاثیر زیادی بر سختی و مقاومت کششی بلوم دارد. منگنز باعث افزایش چقرمگی و مقاومت در برابر سایش میشود.ارزیابی دقیق این ترکیبات به تولید بلومی با خواص مکانیکی مناسب کمک میکند.
کنترل کیفیت مواد اولیه و اهمیت آن در تولید بلوم
کنترل کیفیت مواد اولیه از مرحله ورود به کارخانه تا تولید نهایی اهمیت ویژهای دارد. آزمایشهای شیمیایی، فیزیکی و مکانیکی برای اطمینان از تطابق مواد با استانداردهای تعریف شده انجام میشود. استفاده از مواد اولیه با کیفیت پایین منجر به عیوب سطحی، ترکها و کاهش دوام بلوم میشود. بنابراین، تامین مواد اولیه مرغوب بخش مهمی از فرآیند تولید بلوم است.
5. فرآیندهای تولید بلوم 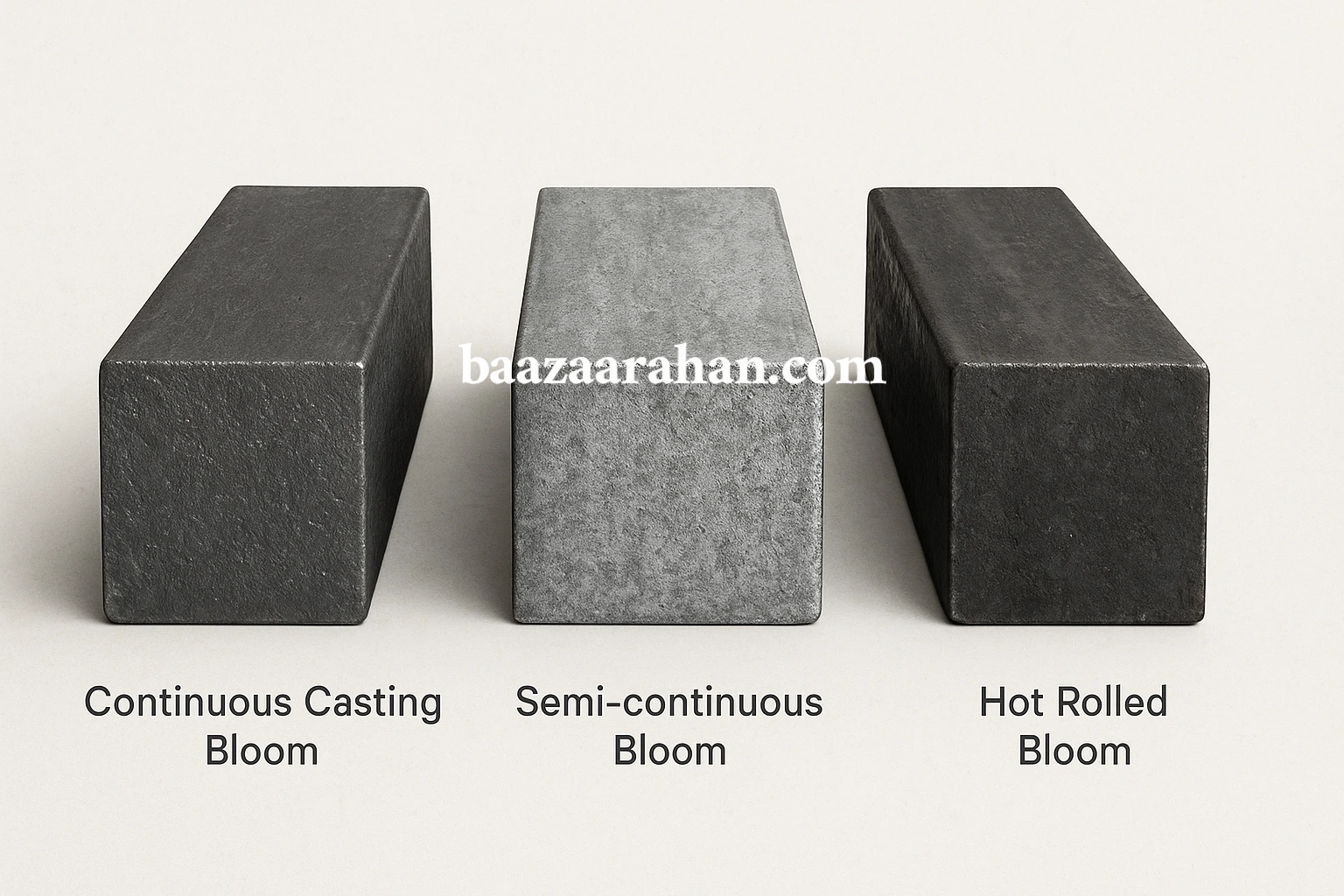
شرح کامل فرآیند ریختهگری پیوسته بلوم
ریختهگری پیوسته (Continuous Casting) اصلیترین روش تولید بلوم است. در این فرآیند، فولاد مذاب در قالبهای مخصوص ریخته شده و به شکل بلوم سرد یا گرم شده خارج میشود. این روش سرعت تولید را افزایش میدهد و ضایعات را کاهش میدهد. فولاد مذاب پس از ریختهگری به سرعت سرد میشود تا ساختار بلوم تثبیت شود.
فرآیندهای نورد گرم و سرد بر روی بلوم
پس از ریختهگری، بلومها معمولاً تحت فرآیند نورد گرم (Hot Rolling) قرار میگیرند تا ابعاد نهایی و خواص مکانیکی بهبود یابد. نورد سرد (Cold Rolling) نیز در موارد خاص برای افزایش دقت ابعاد و بهبود سطح بلوم به کار میرود. این فرآیندها ساختار فلزی را تغییر میدهند و باعث افزایش مقاومت و انعطافپذیری میشوند.
تجهیزات و ماشینآلات اصلی در تولید بلوم
خط تولید بلوم شامل کورههای پیشگرم، قالبهای ریختهگری، دستگاههای نورد گرم و سرد، و سیستمهای کنترل کیفیت است. این تجهیزات باید با دقت بالا کار کنند تا بلوم با مشخصات دقیق تولید شود. اتوماسیون و حسگرهای هوشمند در این ماشینآلات نقش مهمی در بهبود کیفیت و کاهش ضایعات دارند.
کنترل فرآیند و فناوریهای بهبود کیفیت تولید
کنترل دقیق دما، سرعت نورد و ترکیب شیمیایی فولاد از عوامل حیاتی در کیفیت بلوم است. فناوریهای نوین مانند سیستمهای اتوماسیون پیشرفته و کنترل هوشمند فرآیند به تولید یکنواخت و با کیفیت کمک میکنند. همچنین، آزمایشهای غیرمخرب و بررسیهای متالوگرافی برای تشخیص عیوب و تضمین کیفیت بلوم به کار میروند.
6. خواص فیزیکی و مکانیکی بلوم
مشخصات هندسی و ابعادی بلوم
بلومها عموماً در اندازههای استانداردی مثل ۱۵×۱۵، ۲۰×۲۰ یا ۲۵×۲۵ سانتیمتر تولید میشوند. طول معمول آنها نیز بین ۶ تا ۱۲ متر است. این ابعاد برای فرآیندهای بعدی مانند نورد و شکلدهی بهینه شدهاند. دقت در ابعاد بلوم باعث کاهش ضایعات و بهبود کیفیت محصولات نهایی میشود.
خواص مکانیکی: مقاومت کششی، سختی، چقرمگی، انعطافپذیری
بلومها باید مقاومت کششی بالا، سختی کافی، چقرمگی مناسب و انعطافپذیری قابل قبول داشته باشند. این خواص به نوع آلیاژ، ترکیب شیمیایی و فرآیند تولید بستگی دارد. مقاومت کششی بلومها معمولاً بین ۴۰۰ تا ۶۰۰ مگاپاسکال است. چقرمگی و انعطافپذیری آنها تضمین میکند که در مراحل نورد و شکلدهی ترک بر ندارند.
تاثیر فرآیند تولید بر خواص نهایی بلوم
فرآیند ریختهگری، نورد گرم و سرد، دماهای کنترل شده و سرعت تولید نقش مهمی در تعیین خواص نهایی بلوم دارند. نورد گرم باعث افزایش دانهبندی ریز و یکنواخت میشود که به بهبود خواص مکانیکی کمک میکند. کنترل دقیق دما و زمان سرد شدن نیز از ایجاد تنشهای داخلی و ترک جلوگیری میکند.
استانداردهای ملی و بینالمللی مربوط به بلوم
استانداردهای مهمی مانند ASTM A6، EN 10079 و JIS G4051 معیارهای مشخصی برای ابعاد، خواص مکانیکی و ترکیب شیمیایی بلوم تعیین میکنند. رعایت این استانداردها برای تضمین کیفیت، قابلیت اطمینان و تطابق با نیازهای صنایع مختلف ضروری است.
7. کاربردهای بلوم در صنعت فولاد 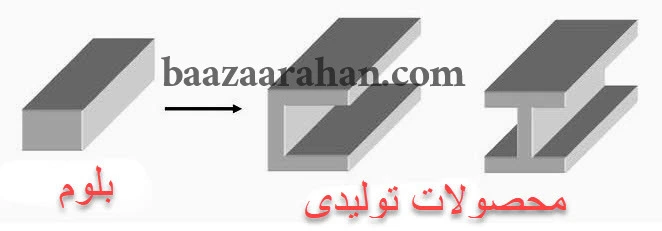
نقش اصلی بلوم در نورد و تولید محصولات فولادی
بلوم به عنوان ماده اولیه اصلی در فرآیند نورد گرم و سرد استفاده میشود. این محصول نیمتمام فولادی با شکل و ابعاد مشخص، به کارخانههای تولید تیرآهن، میلگرد، پروفیل و سایر محصولات نیمتمام ارسال میشود. بلومها باعث تسهیل فرآیند تولید و افزایش دقت ابعادی محصولات نهایی میشوند.
نقش بلوم در تولید تیرآهن، میلگرد، پروفیل و دیگر محصولات نیمتمام
در تولید تیرآهن، میلگرد و پروفیل، بلومها به نوردخانهها فرستاده شده و تحت فرآیندهای شکلدهی و نورد قرار میگیرند. این فرآیندها خواص مکانیکی مطلوب مانند مقاومت کششی و چقرمگی را به محصولات نهایی میبخشند. بلومها به دلیل کیفیت و ابعاد مناسب، نقش کلیدی در حفظ استانداردهای محصولات نیمتمام دارند.
مزایای استفاده از بلوم نسبت به اسلب و بیلت
بلوم نسبت به اسلب و بیلت، شکل هندسی مناسبتر و ابعاد بهینهتری دارد. این ویژگیها باعث میشود فرآیند نورد با دقت و سرعت بالاتری انجام شود. همچنین، بلومها به دلیل استحکام و یکدستی ساختاری بهتر، کیفیت محصولات نهایی را افزایش میدهند و ضایعات کمتری ایجاد میکنند.
موارد خاص استفاده بلوم در صنایع خودروسازی، ساختمانی و کشتیسازی
بلوم در صنایع خودروسازی برای تولید قطعات مقاوم و سبک کاربرد دارد. در صنعت ساختمان، بلوم پایه تولید تیرآهن و ستونهای ساختمانی است. همچنین، در کشتیسازی، بلومهای آلیاژی و ضدزنگ برای ساخت بدنه و قطعات مقاوم در برابر خوردگی استفاده میشوند. این کاربردهای متنوع اهمیت بلوم را در زنجیره فولاد نشان میدهد.
7. عیوب و مشکلات رایج در تولید و استفاده از بلوم
انواع عیوب سطحی و داخلی (ترکها، حفرات، ناخالصیها)
در تولید بلوم در زنجیره فولاد ممکن است انواع عیوب سطحی مانند ترکهای ریز، حفرات یا ناخالصیهای فلزی ظاهر شوند. این مشکلات همچنین شامل عیوب داخلی مثل تخلخلها و ترکهای ناشی از تنشهای حرارتی هستند. این عیوب به طور مستقیم کیفیت و عملکرد بلوم را کاهش میدهند و باید به دقت کنترل شوند.
علل پیدایش عیوب در فرآیند تولید
علل اصلی بروز عیوب شامل کنترل نامناسب دما در ریختهگری، سرعت نورد غیر یکنواخت، ترکیب شیمیایی نامطلوب مواد اولیه، و نقص در تجهیزات تولید است. هرکدام از این عوامل میتواند باعث ایجاد مشکلاتی مانند ترکهای حرارتی، ناپیوستگی فلز و حفرات شود که کیفیت بلوم را تهدید میکند.
اثرات عیوب بر کیفیت محصول نهایی
عیوب در بلوم منجر به کاهش مقاومت مکانیکی، کاهش طول عمر قطعات نهایی و افزایش ریسک شکست در هنگام استفاده میشود. همچنین، عیوب سطحی باعث ایجاد مشکلات در فرآیندهای نورد و شکلدهی شده و میتوانند ضایعات و هزینههای اضافی تولید را افزایش دهند.
روشهای تشخیص و آزمونهای کنترل کیفیت (آزمایشهای غیرمخرب، متالوگرافی و غیره)
برای شناسایی عیوب، روشهای مختلفی استفاده میشود. آزمایشهای غیرمخرب مانند اولتراسونیک، رادیوگرافی و تست مایع نافذ به بررسی داخلی و سطحی بلوم کمک میکنند. متالوگرافی نیز ساختار داخلی بلوم را تحلیل کرده و عیوب میکروسکوپی را نشان میدهد. این روشها به حفظ کیفیت و تضمین عملکرد بهتر محصولات نهایی کمک میکنند.
8. فناوریهای نوین و پیشرفتهای تحقیقاتی
استفاده از فناوریهای نوین در بهبود تولید بلوم (اتوماسیون، کنترل هوشمند فرآیند)
امروزه کارخانههای فولادسازی با استفاده از اتوماسیون پیشرفته و سیستمهای کنترل هوشمند، فرآیند تولید بلوم را بهینه میکنند. این فناوریها شامل حسگرهای دقیق، نرمافزارهای مدیریت تولید و کنترل لحظهای دما و سرعت نورد هستند. این امکانات باعث افزایش یکنواختی کیفیت بلوم و کاهش ضایعات میشوند.
متدهای جدید برای افزایش کیفیت و کاهش ضایعات
روشهای نوین مانند استفاده از تکنولوژیهای ریختهگری خلأ، کنترل بهینه ترکیب شیمیایی و استفاده از آلیاژهای پیشرفته، کیفیت بلوم را بهبود میبخشند. همچنین، به کارگیری فرآیندهای بهبود پس از تولید مانند نورد سرد و عملیات حرارتی باعث کاهش عیوب و افزایش دوام محصول میشود.
تحقیق و توسعه در زمینه آلیاژهای جدید برای بلوم
پژوهشهای اخیر روی توسعه آلیاژهای خاص مانند فولادهای آلیاژی با مقاومت بالا، ضدزنگ و کمکربن متمرکز شده است. این آلیاژها خواص مکانیکی بهتر، مقاومت بیشتر در برابر خوردگی و بهبود انعطافپذیری بلومها را فراهم میکنند و باعث تنوع کاربردهای صنعتی میشوند.
چشمانداز آینده تولید بلوم در صنعت فولاد
با پیشرفت فناوریهای نوین و تحقیقات گسترده، انتظار میرود تولید بلوم به سمت افزایش بهرهوری، کاهش هزینهها و بهبود کیفیت پیش برود. استفاده از هوش مصنوعی و یادگیری ماشین برای کنترل فرآیند، همچنین توسعه آلیاژهای هوشمند، آیندهای روشن برای صنعت بلوم رقم میزند.
9. مقایسه بلوم با دیگر محصولات نیمسخت 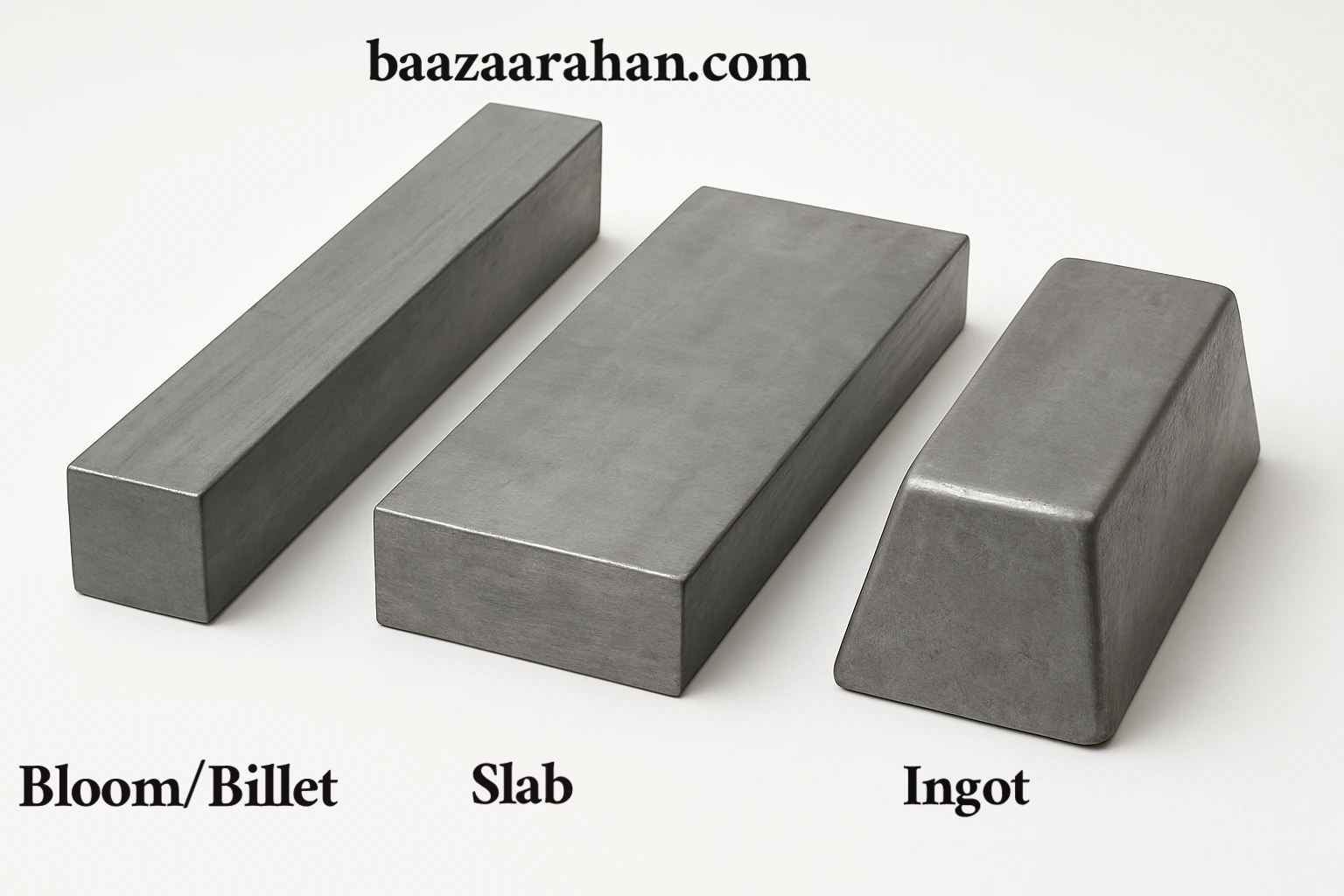
تفاوتهای تکنیکی و کاربردی بین بلوم، بیلت و اسلب
بلوم (Bloom)، بیلت (Billet) و اسلب (Slab) هر کدام شکل و کاربردهای متفاوتی دارند. بلومها معمولاً مقاطع مربع یا مستطیل با ابعاد متوسط دارند و در تولید محصولات طولی مثل تیرآهن و میلگرد کاربرد دارند. بیلتها ابعاد کوچکتری دارند و بیشتر برای قطعات خاص یا نوردهای ظریف استفاده میشوند. اسلبها ضخامت بیشتری دارند و اغلب در تولید ورق و محصولات تخت کاربرد دارند.
مزایا و معایب هر محصول در زنجیره تولید فولاد
بلوم به دلیل شکل و ابعاد مناسب، فرآیند نورد را سادهتر و کمهزینهتر میکند. بیلتها بیشتر برای کاربردهای دقیق و با اندازه کوچک مناسباند ولی هزینه تولید و فرآوری آنها بالاتر است. اسلبها برای تولید ورقهای فولادی ایدهآل هستند اما استفاده آنها در نورد محصولات طولی کمتر رایج است.
انتخاب بهینه بر اساس نوع محصول نهایی
انتخاب بین بلوم، بیلت و اسلب به نوع محصول نهایی بستگی دارد. برای تولید میلگرد، تیرآهن و پروفیل بلوم گزینه بهتری است. برای قطعات کوچکتر و خاص بیلت ترجیح داده میشود. اسلب بیشتر در صنایع ورقسازی و تولید محصولات تخت کاربرد دارد. این انتخاب بهینه باعث کاهش هزینه و بهبود کیفیت محصول نهایی میشود.
10. بررسی اقتصادی و زیستمحیطی تولید بلوم
تحلیل هزینههای تولید بلوم
هزینههای تولید بلوم شامل مواد اولیه، انرژی، نیروی انسانی و نگهداری تجهیزات است. مواد اولیه مانند شمش، قراضه و اسلب بخش عمده هزینه را تشکیل میدهند. همچنین مصرف انرژی در کورهها و خطوط نورد، تاثیر مستقیم بر هزینهها دارد. کاهش ضایعات و بهبود بهرهوری میتواند هزینهها را به شکل قابل توجهی کاهش دهد.
تاثیر فرآیند تولید بلوم بر محیط زیست
تولید بلوم باعث انتشار گازهای گلخانهای، مصرف آب و تولید ضایعات فلزی میشود. آلایندههای هوا شامل دیاکسید کربن، اکسیدهای نیتروژن و ذرات معلق هستند که اثرات منفی بر کیفیت هوا دارند. مدیریت صحیح ضایعات و بهینهسازی مصرف انرژی در کاهش اثرات زیستمحیطی نقش کلیدی دارند.
راهکارهای کاهش مصرف انرژی و آلایندهها
استفاده از فناوریهای نوین مانند بازیافت گرما، بهینهسازی فرآیندهای کوره و استفاده از منابع انرژی پاک به کاهش مصرف انرژی کمک میکند. همچنین، نصب سیستمهای تصفیه گازهای خروجی و مدیریت ضایعات باعث کاهش آلودگی میشود. افزایش بهرهوری تجهیزات نیز به کاهش مصرف انرژی و هزینهها کمک میکند.
اهمیت بازیافت و استفاده مجدد بلوم در زنجیره فولاد
بازیافت قراضههای فولادی و استفاده مجدد مواد اولیه تاثیر زیادی در کاهش هزینهها و حفاظت از منابع طبیعی دارد. این رویکرد به کاهش نیاز به استخراج مواد معدنی جدید و کاهش انتشار گازهای گلخانهای کمک میکند. استفاده بهینه از منابع و بازیافت بخش مهمی از توسعه پایدار در صنعت فولاد است