گندله آهن | فرآیند تولید، مزایا و کاربردها + قیمت روز | بازار آهن
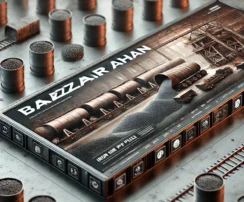
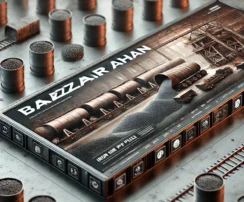
مقدمه
گندله آهن یکی از مهمترین مواد اولیه در صنعت فولاد است که به دلیل ویژگیهای منحصر به فرد خود، نقش اساسی در بهبود راندمان کورههای احیای مستقیم و کوره بلند دارد. در این مقاله، به بررسی کامل فرآیند تولید گندله، مزایا، کاربردها و تأثیر آن بر صنعت فولاد خواهیم پرداخت.
فهرست مطالب
- گندله آهن چیست؟
- فرآیند تولید گندله
- مواد اولیه مورد نیاز برای تولید گندله
- انواع روشهای گندلهسازی
- مزایای استفاده از گندله در صنعت فولاد
- تفاوت بین گندله و دیگر مواد آهندار
- کاربردهای اصلی گندله
- بازار جهانی گندله آهن
- چالشهای تولید گندله
- تاثیر گندله بر محیط زیست
- آینده گندلهسازی در ایران و جهان
- جمعبندی
گندله آهن چیست؟
گندله (Pellet) نوعی ماده اولیه آهندار است که از فرآوری سنگ آهن و افزودنیهای مختلف تولید میشود. این محصول به شکل گلولههای کروی ساخته میشود و ویژگیهایی مانند چگالی مناسب، استحکام بالا و قابلیت احیاپذیری مطلوب دارد.
فرآیند تولید گندله
فرآیند تولید گندله سنگ آهن
گندله سنگ آهن، مادهای است که در صنایع فولادسازی مورد استفاده قرار میگیرد. تولید گندله شامل مراحل زیر است:
1. آمادهسازی مواد اولیه
مواد اولیه برای تولید گندله شامل سنگ آهن (کنسانتره)، آب، بنتونیت (به عنوان چسباننده)، مواد افزودنی مانند آهک و برخی مواد بازیافتی است. این مواد در ابتدا خشک و سپس به نسبتهای معین با یکدیگر مخلوط میشوند.
2. مخلوطسازی و همگنسازی
کنسانتره سنگ آهن با مواد افزودنی مانند بنتونیت و آب در دستگاههای میکسر بهخوبی ترکیب میشود تا خواص مکانیکی و شیمیایی مناسب برای تولید گندله فراهم شود.
3. تولید گندله خام (Pelletizing)
در این مرحله، مخلوط تهیهشده وارد دیسکهای گندلهساز یا درامهای دوار میشود. این دستگاهها باعث تشکیل گلولههایی از مخلوط شده و گندله خام با اندازههای مشخص تولید میشود.
4. خشک کردن گندله خام
گندلههای خام دارای رطوبت بالایی هستند، بنابراین باید در کورههای خشککن رطوبت اضافی آنها گرفته شود. این کار از ترک خوردن و از بین رفتن گندلهها در مراحل بعدی جلوگیری میکند.
5. پخت گندله (Induration)
گندلههای خشک شده وارد کوره پخت میشوند و تحت حرارت بالا (معمولاً بین 1200 تا 1350 درجه سانتیگراد) قرار میگیرند. در این مرحله، واکنشهای فیزیکی و شیمیایی منجر به استحکام بخشی گندلهها شده و آنها را برای استفاده در کوره بلند یا احیای مستقیم آماده میکند.
6. خنکسازی و دانهبندی
پس از پخت، گندلهها باید بهتدریج خنک شوند تا از شوک حرارتی و خرد شدن آنها جلوگیری شود. سپس بر اساس اندازه، دانهبندی شده و آماده ارسال به صنایع فولادسازی میشوند.
7. انبارش و حملونقل
گندلههای تولید شده در انبارها ذخیره شده و بهوسیله نوار نقاله، واگن، یا کامیون به کارخانههای فولادسازی ارسال میشوند.
برای دیدن مقاله انواع مقاطع مختلف میلگرد و کاربردهای آنها کلیک کنید.
مزایای استفاده از گندله در صنعت فولاد
گندله (Pellet) یکی از مهمترین مواد اولیه مورد استفاده در تولید فولاد است که از کنسانتره سنگ آهن فرآوریشده تشکیل شده و طی فرآیند گندلهسازی، استحکام مکانیکی و خواص فیزیکی و شیمیایی مناسبی پیدا میکند. استفاده از گندله در فرآیندهای فولادسازی به دلایل مختلفی از جمله افزایش راندمان، کاهش هزینههای انرژی، بهبود کنترل فرآیند و کاهش اثرات زیستمحیطی، مزایای قابلتوجهی دارد. در ادامه این مزایا به تفصیل بررسی میشوند.
1. بهبود عملکرد ترمودینامیکی و سینتیکی فرآیند احیا
1.1. بهینهسازی جریان گاز در راکتورهای احیای مستقیم و کوره بلند
- گندلهها از نظر اندازه و شکل، یکنواخت بوده و ساختار متخلخلی دارند که موجب افزایش سطح تماس بین مواد احیاکننده (CO و H₂) و اکسیدهای آهن در فرآیند احیا میشود.
- در کوره بلند، این ویژگی باعث بهبود نفوذ گازهای کوره و افزایش نرخ انتقال جرم و حرارت میشود. در فرآیندهای احیای مستقیم مانند میدرکس (MIDREX) و HYL، تخلخل مناسب گندلهها منجر به کاهش زمان واکنش و افزایش بهرهوری گاز طبیعی میشود.
1.2. کاهش انرژی مصرفی در فرآیند احیا
- گندلهها به دلیل ترکیب شیمیایی یکنواخت، نرخ احیاپذیری بالاتری دارند و برای دستیابی به درصد احیای مشخص، نیاز به انرژی کمتری دارند.
- در مقایسه با کلوخههای سنگ آهن، گندلهها میزان FeO کمتری پس از احیا دارند، که موجب کاهش مصرف انرژی در فولادسازی میشود.
2. بهبود خصوصیات مکانیکی و فیزیکی مواد اولیه
2.1. افزایش استحکام مکانیکی (Mechanical Strength)
- استحکام فشاری سرد (Cold Crushing Strength – CCS) گندلهها معمولاً بیش از 250 کیلوگرم بر گندله است، که آنها را در برابر خرد شدن در حین حملونقل، ذخیرهسازی و بارگذاری در کوره مقاوم میکند.
- مقاومت در برابر سایش و ضربه (Tumbling & Abrasion Index): گندلههای تولیدی دارای میزان تخلخل 25 تا 30 درصد هستند که مانع از ایجاد ریزدانههای نامطلوب و گرد و غبار در کوره میشود.
2.2. پایداری حرارتی و کاهش شکستگی در دماهای بالا
- گندلهها در فرآیند پخت در دماهای بین 1200 تا 1350°C حرارت میبینند و استحکام مناسبی در برابر تنشهای حرارتی نشان میدهند.
- بر خلاف سنگ آهن دانهبندی شده که در دماهای بالا مستعد ترکخوردگی و ریزش در کوره است، گندلهها ساختار همگن و پایدارتری دارند.
3. کنترل دقیق ترکیب شیمیایی و بهبود کیفیت محصول نهایی
3.1. کاهش ناخالصیها و بهبود احیاپذیری
- فرآیند گندلهسازی امکان حذف عناصر مضر مانند گوگرد (S)، فسفر (P) و سیلیس (SiO₂) را فراهم میکند که تأثیر مستقیمی بر کیفیت فولاد تولیدی دارد.
- گندلههای آهنی معمولاً دارای عیار Fe بین 64 تا 69 درصد هستند، که بالاتر از سنگ آهن خام یا کلوخههای طبیعی است.
3.2. امکان تنظیم ترکیب شیمیایی متناسب با فرآیندهای مختلف فولادسازی
- در فرآیندهای احیای مستقیم، نسبت FeO/Fe₂O₃ گندلهها قابل کنترل است، که باعث بهینهسازی راندمان احیا و کاهش مصرف انرژی میشود.
- افزودنیهای مناسب مانند آهک (CaO) و دولومیت (MgO) به گندلهها اضافه میشود تا ترکیب سرباره کنترل شود و خواص متالورژیکی بهبود یابد.
4. افزایش راندمان فرآیند تولید فولاد و کاهش هزینههای تولید
4.1. کاهش مصرف کک و گاز طبیعی
- گندلهها نسبت به سنگ آهن دانهبندی شده، انرژی کمتری برای احیا نیاز دارند که موجب کاهش مصرف کک در کوره بلند و کاهش گاز طبیعی در احیای مستقیم میشود.
- نسبت مصرف انرژی در گندلهسازی و احیا در فرآیند میدرکس حدود 2.4 تا 2.7 گیگاژول بر تن آهن احیا شده (GJ/t DRI) است که در مقایسه با استفاده از سنگ آهن دانهبندی شده، بهرهوری بهتری دارد.
4.2. افزایش بازده تولید فولاد
- استفاده از گندله با ترکیب شیمیایی بهینه باعث افزایش بازدهی تبدیل آهن به فولاد شده و میزان نسبت چدن به سرباره در کوره بلند را کاهش میدهد.
- در فرآیندهای احیای مستقیم، استفاده از گندله با تخلخل مناسب باعث کاهش مصرف آهک و سایر مواد سربارهساز میشود.
5. کاهش اثرات زیستمحیطی و بهبود ایمنی
5.1. کاهش انتشار CO₂ و گازهای آلاینده
- مصرف کمتر کک و گاز طبیعی باعث کاهش انتشار CO₂ و SO₂ شده و تأثیرات زیستمحیطی فرآیند فولادسازی را کاهش میدهد.
- در فرآیند گندلهسازی، با استفاده از فیلترهای الکترواستاتیکی و غبارگیرها، انتشار گرد و غبار تا حد زیادی کنترل میشود.
5.2. کاهش هدررفت مواد و بازیافت مواد معدنی
- گندلهها به دلیل استحکام بالاتر، هدررفت کمتری در هنگام حملونقل و بارگیری دارند، درحالیکه سنگ آهن دانهبندیشده مستعد شکستگی و ایجاد ضایعات است.
- با استفاده از بازیافت نرمههای آهندار در فرآیند گندلهسازی، میتوان میزان بهرهوری مواد خام را افزایش داد.
تفاوت بین گندله و دیگر مواد آهندار
ویژگی | گندله | کلوخه | نرمه سنگ آهن |
---|---|---|---|
شکل | کروی | نامنظم | پودری |
درصد آهن | بالا | متوسط | کم |
میزان احیاپذیری | بالا | متوسط | کم |
قابلیت حمل و نقل | بالا | متوسط | پایین |
کاربردهای اصلی گندله
گندله، مادهای فرآوریشده از سنگ آهن است که در صنایع مختلف، بهویژه فولادسازی، مورد استفاده قرار میگیرد. این ماده به دلیل شکل کروی، ترکیب شیمیایی یکنواخت و استحکام بالا، مزایای متعددی در فرآیندهای تولید آهن و فولاد دارد. در ادامه، کاربردهای اصلی گندله بررسی میشود.
1. استفاده در کوره بلند (Blast Furnace)
ویژگیها و مزایا:
- بهبود عملکرد کوره بلند: گندلهها به دلیل تخلخل و یکنواختی در اندازه، موجب بهبود نفوذ گازهای احیاکننده در کوره میشوند.
- کاهش مصرف کک: استفاده از گندله باعث کاهش میزان کک مصرفی در فرآیند احیا شده و راندمان کلی کوره را افزایش میدهد.
- افزایش بازدهی فرآیند ذوب: ترکیب شیمیایی کنترلشده گندله، باعث کاهش میزان عناصر مضر مانند فسفر (P) و گوگرد (S) شده و تأثیر مثبتی بر کیفیت چدن مذاب دارد.
سهم استفاده از گندله در کوره بلند:
- در برخی کورههای بلند پیشرفته، ترکیبی از گندله (30-50%)، آگلومره و سنگ آهن دانهبندیشده برای بهینهسازی فرآیند احیا مورد استفاده قرار میگیرد.
- در کشورهایی که منابع سنگآهن دانهبندی شده محدود است، نسبت استفاده از گندله افزایش مییابد.
2. استفاده در فرآیند احیای مستقیم (DRI)
روشهای احیای مستقیم شامل:
✅ میدرکس (MIDREX)
✅ HYL
✅ پروسسهای قائمشکل و افقیشکل (Shaft Furnace & Rotary Kiln)
مزایای استفاده از گندله در احیای مستقیم:
- افزایش راندمان احیا: گندلههای مورد استفاده در DRI دارای تخلخل بالا (حدود 25-30%) هستند که موجب بهبود نفوذ گازهای احیاکننده (CO و H₂) میشود.
- کاهش مصرف گاز طبیعی: به دلیل احیاپذیری بهتر گندله، مصرف گاز طبیعی در واحدهای احیای مستقیم کاهش مییابد.
- تأمین ماده اولیه برای فولادسازی الکتریکی: آهن اسفنجی (DRI) تولید شده از گندله، خوراک اصلی کورههای قوس الکتریکی (EAF) است.
درصد استفاده از گندله در احیای مستقیم:
- در فرآیندهای میدرکس و HYL، گندله معمولاً بیش از 80% از خوراک ورودی را تشکیل میدهد.
- در برخی واحدها، ترکیب گندله و لامپ اور (Lump Ore) به کار میرود، اما کیفیت گندله باعث ارجحیت آن میشود.
3. تولید چدن مذاب و فولاد در روشهای ترکیبی
در برخی واحدهای فولادسازی که از روشهای ترکیبی استفاده میکنند، گندله بهعنوان خوراک اولیه به کار میرود. برای مثال:
✅ روش کوره بلند + مبدل اکسیژنی (BOF):
- گندله ابتدا در کوره بلند احیا شده و چدن مذاب حاصل به فولادسازی BOF منتقل میشود.
- کاهش ناخالصیها و تنظیم ترکیب شیمیایی، کیفیت فولاد را بهبود میبخشد.
✅ روش احیای مستقیم + کوره القایی:
- گندله در فرآیند احیای مستقیم به آهن اسفنجی تبدیل شده و در کوره القایی ذوب میشود.
✅ روش ترکیبی DRI + EAF:
- واحدهای فولادسازی که از آهن اسفنجی در کورههای قوس الکتریکی استفاده میکنند، معمولاً گندله را بهعنوان ماده اولیه اصلی به کار میبرند.
4. تولید بریکتهای آهنی (Hot Briquetted Iron – HBI)
چرا از گندله برای تولید HBI استفاده میشود؟
- برخی واحدهای فولادسازی برای جلوگیری از مشکلات حملونقل آهن اسفنجی (که بسیار فعال و مستعد اکسیداسیون است)، آن را به بریکت داغ (HBI) تبدیل میکنند.
- در فرآیند HBI، گندلهها پس از احیا در دمای بالا فشرده شده و بهصورت بلوکهای متراکم درآمده که حملونقل و ذخیرهسازی آنها ایمنتر است.
- مزیت HBI: پایداری بیشتر، عدم اشتعالپذیری، کاهش هدررفت مواد.
5. استفاده در صنایع ریختهگری و تولید قطعات آهنی
در برخی صنایع، از گندلههای خاصی برای تولید قطعات آهنی و چدنی در واحدهای ریختهگری استفاده میشود.
✅ ویژگیهای موردنیاز برای گندلههای ریختهگری:
- درصد بالای Fe (بیش از 67%)
- حداقل ناخالصیها (P، S، SiO₂)
- استحکام مکانیکی بالا برای جلوگیری از شکستن در حین ذوب
6. استفاده در آزمایشگاهها و تحقیقات متالورژی
برخی از گندلههای خاص بهعنوان نمونههای استاندارد در تحقیقات دانشگاهی، آزمایشگاههای متالورژی و صنایع فولادسازی برای بررسی رفتار احیای سنگ آهن و ارزیابی فرآیندهای جدید مورد استفاده قرار میگیرند.
✅ مطالعات شامل:
- بررسی نرخ احیاپذیری گندلهها در دماهای مختلف
- تحلیل تأثیر ترکیب شیمیایی بر عملکرد کوره بلند و DRI
- توسعه روشهای بهینهسازی فرآیند گندلهسازی و پخت
7. استفاده در ذخیرهسازی و حملونقل بینالمللی
ویژگیهای گندله برای حملونقل:
- استحکام بالا: برخلاف سنگ آهن دانهبندیشده که در حملونقل خرد میشود، گندله مقاومت بالایی دارد.
- کاهش هزینههای حملونقل: چگالی بالاتر گندله در مقایسه با کنسانتره، موجب کاهش هزینههای جابهجایی و ذخیرهسازی میشود.
- عدم جذب رطوبت زیاد: برخلاف کنسانتره که در تماس با آب سخت شده و مشکلات تخلیه ایجاد میکند، گندلهها کمتر تحت تأثیر رطوبت قرار میگیرند.
✅ نقش کلیدی در زنجیره تأمین جهانی فولاد:
- بسیاری از کشورها مانند هند، برزیل، ایران و روسیه، گندله را بهعنوان یک محصول صادراتی به واحدهای فولادسازی در چین، اروپا و آمریکا ارسال میکنند.
بازار جهانی گندله آهن
بازار جهانی گندله آهن به دلیل تقاضای بالای صنعت فولاد در حال رشد است. کشورهایی مانند چین، هند و ایران از تولیدکنندگان اصلی گندله در جهان محسوب میشوند.
برای استعلام قیمت، خرید آهن آلات و تمامی محصولات زنجیره فولاد با بازار آهن در تماس باشید.
چالشهای تولید گندله
- هزینههای بالای تولید
- دسترسی محدود به مواد اولیه
- مشکلات زیستمحیطی
- توسعه فناوریهای جدید
تأثیر گندله بر محیط زیست
استفاده از گندله در تولید فولاد موجب کاهش گازهای گلخانهای و بهینهسازی مصرف انرژی میشود که این امر تأثیر مثبتی بر محیط زیست دارد.
آینده گندلهسازی در ایران و جهان
با توجه به رشد صنعت فولاد، آینده گندلهسازی بسیار روشن است. توسعه فناوریهای جدید میتواند بهرهوری را افزایش داده و اثرات زیستمحیطی را کاهش دهد.
جمعبندی
گندله آهن یکی از مهمترین مواد اولیه در صنعت فولاد است که با فرآیندهای مختلفی تولید میشود. این ماده دارای مزایای زیادی از جمله افزایش راندمان کورهها، کاهش هزینهها و کاهش آلودگی محیط زیست است. با رشد بازار فولاد، اهمیت گندلهسازی بیش از پیش افزایش مییابد.