بیلت فولادی چیست؟ نقش کلیدی بیلت در زنجیره تولید فولاد
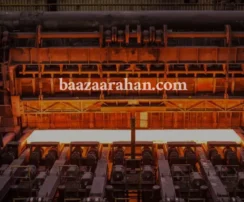
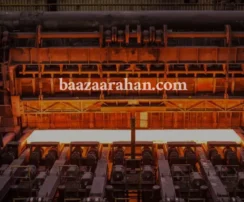
1. جایگاه بیلت در زنجیره تولید فولاد
بیلت (Billet) یک محصول نیمهنهایی فولادی است که در مراحل ابتدایی زنجیره تولید فولاد قرار دارد. این مقطع فلزی بهصورت منشوری چهارضلعی با ابعاد کوچکتر نسبت به بلوم و اسلب تولید میشود. بیلت معمولاً دارای سطح مقطع مربع (معمولاً 100 تا 150 میلیمتر) و طول چند متری است. کارخانهها از آن برای تولید میلگرد، مفتول، پیچ و مهره و قطعات صنعتی سبک استفاده میکنند.
بیلت از طریق فرآیند ریختهگری مداوم (Continuous Casting) یا قالبریزی سنتی تولید میشود. در روش مداوم، فولاد مذاب مستقیماً به شکل نوار جامد منشوری تبدیل میشود. این روش باعث افزایش بهرهوری و کاهش ضایعات میشود. بهدلیل همین مزایا، بیشتر بیلتهای امروزی با این روش تولید میشوند.
از نظر مهندسی، بیلت باید ساختاری همگن، سطحی صاف و ترکیب شیمیایی یکنواخت داشته باشد. این ویژگیها در فرآیندهای بعدی مانند نورد و فورجینگ نقش کلیدی ایفا میکنند. هرگونه نقص در ساختار بیلت میتواند کیفیت محصول نهایی را کاهش دهد.
بیلت یکی از سه شکل اصلی محصولات نیمهنهایی فولاد است:
-
بیلت (Billet): برای نورد میلگرد، مفتول و قطعات سبک
-
بلوم (Bloom): برای ریل، تیرآهن و مقاطع سنگین
-
اسلب (Slab): برای ورقهای گرم و سرد، لوله و کویل
در زنجیره فولاد، بیلت پلی است میان فولاد مذاب و محصولات نهایی ساختمانی یا صنعتی. جایگاه آن استراتژیک است؛ چراکه کیفیت آن، روی عملکرد نهایی محصول اثر مستقیم دارد. به همین دلیل، بیلت نه فقط یک محصول، بلکه معیار کیفیت در زنجیره تولید فولاد بهحساب میآید.
2. فرآیند تولید بیلت: از فولاد مذاب تا محصول نیمهنهایی 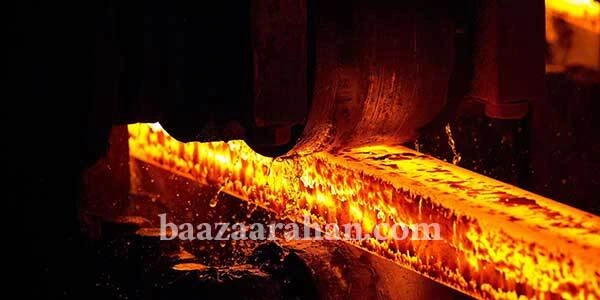
تولید بیلت فولادی از مرحلهای آغاز میشود که فولاد مذاب آماده خروج از کوره است. در این مرحله، دما، ترکیب شیمیایی و پاکیزگی فولاد اهمیت بالایی دارد. برای تولید بیلت با کیفیت بالا، اپراتورها باید شرایط پایدار را در کل فرآیند حفظ کنند.
مراحل اصلی تولید بیلت عبارتاند از:
-
1. تخلیه فولاد مذاب از کوره قوس الکتریکی یا کنورتور
-
2. ریختهگری پیوسته (Continuous Casting) به شکل مقطع مربع
-
3. خنککاری در قالب آبگرد و ناحیه غلتکها
-
4. برش به طولهای استاندارد (معمولاً 6 تا 12 متر)
در واحد ریختهگری مداوم، فولاد مذاب ابتدا وارد تاندیش میشود. تاندیش نقش بافر را دارد و جریان مذاب را یکنواخت به قالب هدایت میکند. سپس، مذاب وارد قالب مسی آبگرد میشود. در این قالب، سطح بیرونی بیلت جامد میشود، در حالیکه مرکز آن هنوز داغ و نیمهمذاب است.
در مرحله بعد، غلتکهای هادی و سیستمهای خنککننده باعث شکلگیری نهایی بیلت میشوند. این بیلتهای تازهسختشده، به کمک برشگرهای اتوماتیک به قطعاتی با طول مشخص تقسیم میشوند. این قطعات بهسرعت به سمت نورد گرم یا سرد هدایت میشوند، یا در انبار نگهداری میشوند.
کیفیت تولید بیلت به موارد زیادی بستگی دارد؛ از جمله:
-
دمای دقیق مذاب
-
سرعت ریختهگری
-
خنککاری مؤثر
-
ترکیب شیمیایی آلیاژ
-
یکنواختی انجماد و پوستهسازی
در صورتیکه هر یک از این فاکتورها دچار اختلال شود، محصول نهایی ممکن است ترکدار، پوستهپوسته یا دچار جدایش ساختاری شود.
در مجموع، تولید بیلت نیازمند هماهنگی کامل بین فناوری، نیروی انسانی و کنترل کیفیت است. کارخانههایی که این هماهنگی را بهخوبی اجرا میکنند، محصولاتی با ساختار همگن و استحکام بالا به بازار عرضه میکنند.
3. انواع بیلت فولادی و ویژگیهای فنی آنها
بیلتها در ظاهر مشابه بهنظر میرسند، اما از نظر ترکیب شیمیایی، کاربرد صنعتی و خواص مکانیکی تفاوتهای اساسی دارند. این تفاوتها باعث شده که انواع گوناگونی از بیلت فولادی در بازار تولید شود، هر کدام برای کاربری خاص طراحی شدهاند.
انواع رایج بیلت فولادی بر اساس کاربرد و ترکیب عبارتاند از:
-
بیلت کربنی ساده (Plain Carbon Steel Billet):
برای ساخت میلگرد، مفتول و قطعات ساختمانی معمولی -
بیلت کمآلیاژ (Low Alloy Billet):
دارای عناصر آلیاژی محدود مثل منگنز یا سیلیسیوم – مناسب برای قطعات مقاومتر -
بیلت آلیاژی (Alloy Steel Billet):
شامل کروم، نیکل یا مولیبدن – مناسب قطعات تحت فشار و شرایط سخت -
بیلت ضدزنگ (Stainless Steel Billet):
با درصد بالای کروم و نیکل – برای صنایع غذایی، دارویی و شیمیایی -
بیلت مخصوص فورجینگ (Forging Billet):
مناسب ماشینکاری و قطعات دقیق صنعتی
از نظر فنی، بیلتها باید دارای ویژگیهای مشخصی باشند. برخی از مهمترین ویژگیهای فنی شامل موارد زیر است:
-
ترکیب شیمیایی دقیق: باید مطابق با استانداردهای بینالمللی مانند ASTM یا DIN باشد.
-
میکروساختار یکنواخت: ساختار درونی بیلت باید فاقد درز، حفره یا جدایش باشد.
-
استحکام کششی مناسب: برای تحمل فشار نورد و کار مکانیکی
-
چقرمگی بالا: بهویژه در کاربردهایی که ضربه یا خمش در کار است
-
سطح صاف و بدون ترک: برای جلوگیری از نقص در مراحل بعدی تولید
برای مثال، بیلت مورد استفاده در ساخت پیچ و مهره باید خاصیت ماشینکاری خوبی داشته باشد. درحالیکه بیلت مورد استفاده برای میلگرد باید فرمپذیری و انعطاف خوبی داشته باشد. بنابراین، تولیدکنندهها بسته به نیاز مشتری، بیلت با ترکیب خاص تولید میکنند.
در نهایت، انتخاب نوع بیلت به نوع محصول نهایی، شرایط کاری آن، و فرآیند نورد بستگی دارد. شناخت انواع بیلت، به مهندسان و صنایع کمک میکند تا مواد اولیه مناسبی را انتخاب کرده و از مشکلات بعدی جلوگیری کنند.
4. استانداردهای بینالمللی تولید بیلت: از ترکیب شیمیایی تا خواص مکانیکی
تولید بیلت فولادی، تنها وابسته به فناوری و تجهیزات نیست. رعایت استانداردهای دقیق، بخش جداییناپذیر از کیفیت نهایی محصول است. استانداردها تضمین میکنند که بیلتها در تمام شرایط، قابل اطمینان و مناسب کاربرد صنعتی باشند.
مهمترین استانداردهای جهانی تولید بیلت عبارتاند از:
-
ASTM A615 و ASTM A29 (آمریکا): برای میلگرد و بیلتهای کربنی
-
DIN EN 10025 (اروپا): برای بیلتهای ساختمانی و سازهای
-
JIS G4051 (ژاپن): برای بیلتهای آلیاژی و خودرویی
-
ISIRI 3132 (ایران): معادل استانداردهای بینالمللی برای تولید داخلی
این استانداردها مشخصاتی چون ترکیب شیمیایی مجاز، محدوده استحکام کششی و تسلیم، درصد کربن، منگنز، گوگرد، فسفر، و حتی ابعاد دقیق بیلت را تعیین میکنند.
بهعنوان مثال، در استاندارد ASTM A615:
-
حداکثر مقدار کربن باید ۰٫۳۵٪ باشد
-
گوگرد و فسفر نباید از ۰٫۰۵٪ بیشتر باشند
-
مقاومت کششی باید حداقل ۴۰۰ مگاپاسکال باشد
ویژگیهای مکانیکی که تحت این استانداردها کنترل میشوند، شامل موارد زیر است:
-
مقاومت به کشش (Tensile Strength)
-
نقطه تسلیم (Yield Strength)
-
سختی (Hardness)
-
انعطافپذیری (Ductility)
-
ضربهپذیری (Impact Toughness)
کارخانههای تولید بیلت موظفاند نمونههایی از هر ذوب را آزمایش کنند. این آزمایشها شامل طیفسنجی برای آنالیز شیمیایی، تست کشش، و بررسی ساختار داخلی با متالوگرافی است.
همچنین، بیلتها باید از نظر کیفیت سطحی نیز بررسی شوند. وجود ترک، تاول، پوسته یا آخال غیرمجاز، طبق استانداردها مردود محسوب میشود. در صورت مغایرت، محصول یا اصلاح میشود یا به عنوان ضایعات خارج میگردد.
در نهایت، پیروی از این استانداردها نهتنها کیفیت را تضمین میکند، بلکه امکان صادرات بیلت به بازارهای جهانی را فراهم میسازد. مشتریان بزرگ جهانی، فقط از تولیدکنندگانی خرید میکنند که استانداردهای رسمی را رعایت میکنند.
5. کاربردهای صنعتی بیلت فولادی: از میلگرد تا قطعات خودرو
بیلت فولادی یک محصول نیمهنهایی است، اما نقش نهایی آن در صنایع بسیار متنوع و حیاتی است. بسته به نوع ترکیب و خواص مکانیکی، بیلتها در صنایع مختلف به شکلهای گوناگون مورد استفاده قرار میگیرند. درواقع، بسیاری از محصولات فولادی اطراف ما از بیلت آغاز میشوند.
رایجترین کاربردهای بیلت فولادی عبارتاند از:
-
تولید میلگرد ساختمانی:
پرکاربردترین مصرف بیلت در ایران و جهان. میلگردها برای بتن مسلح، پلها، سدها و برجها استفاده میشوند. -
ساخت مفتول فولادی (Wire Rod):
برای تولید سیم، کابل، فنر، توری فلزی و قطعات صنعتی ظریف -
قطعات خودرو:
مثل شفت، چرخدنده، توپی چرخ و پین – مخصوصاً از بیلتهای آلیاژی -
تولید پیچ و مهره و ابزارآلات صنعتی:
با ماشینکاری دقیق روی بیلتهای با دقت بالا -
صنایع نفت و گاز:
بیلتهای ضدزنگ برای ساخت اتصالات، فلنجها و تجهیزات مقاوم به خوردگی
از نظر فرآیندی، بیلتها ابتدا به واحد نورد منتقل میشوند. آنجا بسته به نیاز، به مقاطع مختلف مثل میلگرد، تیرآهن یا تسمه تبدیل میشوند. برای قطعات ماشینکاریشده، بیلتها پس از برش و عملیات حرارتی، وارد خطوط تولید تراشکاری یا فورج میشوند.
مثال ملموس: در کارخانه خودروسازی، از بیلت آلیاژی با درصد خاص منگنز و کروم برای ساخت شفت گیربکس استفاده میشود. درحالیکه در پروژههای ساختمانی، بیلت ساده کربنی تبدیل به میلگرد A3 میشود.
مزیت مهم بیلتها، قابلیت شکلدهی بالا و تنوع کاربرد است. یک خط ریختهگری، میتواند برای چند صنعت مختلف بیلت تولید کند. این موضوع برای کارخانهها بهصرفه و برای مشتریها اطمینانبخش است.
در پایان، کاربردهای بیلت بهقدری گسترده است که میتوان گفت هر صنعتی که به فولاد نیاز دارد، به نحوی با بیلت سر و کار دارد. شناخت این کاربردها به تصمیمگیری فنی و اقتصادی صنایع کمک میکند.
6. مزایا و معایب بیلت در مقایسه با سایر محصولات نیمهنهایی (اسلب و بلوم) 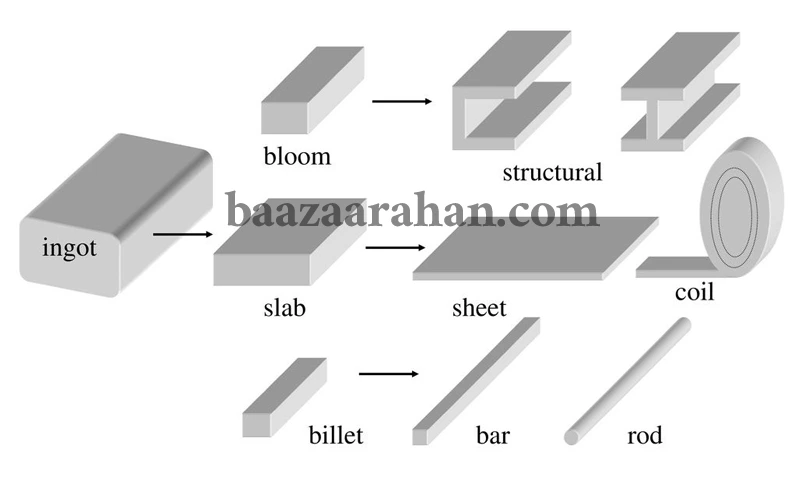
بیلت، اسلب (Slab) و بلوم (Bloom) سه محصول نیمهنهایی کلیدی در صنعت فولاد هستند. هرکدام ویژگیها و کاربردهای خاص خود را دارند. شناخت مزایا و معایب هرکدام، به انتخاب صحیح در زنجیره تولید کمک میکند.
مزایای بیلت نسبت به اسلب و بلوم:
-
ابعاد کوچکتر و وزن کمتر: بیلتها معمولاً مقطع مربع یا مستطیل با ابعاد کوچکتر دارند که فرآیند نورد را برای تولید میلگرد و مفتول آسانتر میکند.
-
قابلیت شکلدهی بهتر: به دلیل ابعاد کوچکتر، بیلتها راحتتر به مقاطع پیچیده تبدیل میشوند.
-
انعطافپذیری کاربردی: بیلتها در صنایع مختلف، از ساختمانی تا خودروسازی، کاربرد گستردهای دارند.
-
سرعت تولید بالاتر: فرآیند نورد بیلتها به نسبت اسلبها سریعتر است و مصرف انرژی کمتری دارد.
-
کاهش ضایعات: ابعاد مناسب بیلت، پرت مواد را کاهش میدهد.
معایب بیلت نسبت به اسلب و بلوم:
-
محدودیت در ساخت محصولات تخت: بیلتها برای تولید ورق و کویل مناسب نیستند. در این موارد اسلبها بهتر عمل میکنند.
-
ابعاد کمتر برای محصولات بزرگ: در تولید مقاطع حجیم و بزرگ، بلومها اولویت دارند.
-
هزینه بیشتر در برخی کاربردها: برای تولید مقاطع تخت، تبدیل بیلت نیازمند مراحل اضافی است که هزینه را بالا میبرد.
در مقابل، اسلبها بهدلیل ابعاد بزرگ و مسطح، برای تولید ورقهای فولادی و کویلها مناسبتر هستند. بلومها معمولاً برای تولید تیرآهن، مقاطع بزرگ ساختمانی و قطعات سنگین استفاده میشوند.
انتخاب بین بیلت، اسلب و بلوم وابسته به محصول نهایی، تکنولوژی موجود در کارخانه و نیاز بازار است. شرکتها معمولاً براساس تقاضا و قابلیتهای خط تولید، محصول نیمهنهایی مناسب را انتخاب میکنند.
در نهایت، بیلت با توجه به ابعاد و خواص خود، یک گزینه ایدهآل برای صنایع ساخت میلگرد، مفتول و قطعات متوسط صنعتی است، اما برای تولید ورق یا مقاطع بسیار بزرگ، گزینههای دیگر ارجحیت دارند.
7. فرآیند تولید بیلت: از ریختهگری مداوم تا نورد
تولید بیلت فولادی با استفاده از فرآیند ریختهگری مداوم شروع میشود. در این مرحله، فولاد مذاب در قالبهای مسی خنک شده شکل گرفته و به صورت پیوسته به بیلتهای جامد تبدیل میشود. کیفیت این مرحله بر کل زنجیره تولید تأثیرگذار است.
پس از شکلگیری بیلتها، آنها وارد واحد نورد گرم میشوند. در این مرحله، بیلتها تحت فشار و حرارت بالا قرار میگیرند تا به شکلهای مورد نظر مانند میلگرد یا مفتول تبدیل شوند. نورد گرم باعث بهبود خواص مکانیکی و ساختار فولاد میشود.
فرآیند نورد معمولاً شامل چندین مرحله با کاهشهای تدریجی در ضخامت است. کنترل دمای بیلت در این مراحل اهمیت بالایی دارد تا از ترک خوردگی و سایر عیوب جلوگیری شود. تجهیزات دقیق و حسگرهای پیشرفته در این بخش استفاده میشوند.
علاوه بر نورد گرم، بیلتها ممکن است تحت عملیات حرارتی مانند آنیلینگ یا نرمالیزه کردن قرار بگیرند تا خواص فیزیکی مطلوبتر و یکنواختتری به دست آید. این عملیات باعث کاهش تنشهای داخلی و افزایش انعطافپذیری فولاد میشود.
یکی دیگر از مراحل مهم، برش و آمادهسازی بیلتها برای حمل و نقل و استفاده نهایی است. تیغههای برش دقیق، بیلتها را به طولهای استاندارد برش میدهند تا برای مراحل بعدی فرآوری آماده باشند.
تجهیزات و فناوریهای بهکاررفته در هر یک از این مراحل نقش کلیدی در افزایش کیفیت و کاهش هزینه تولید دارند. به همین دلیل، شرکتهای بزرگ فولادی بهطور مداوم در بهبود این فرآیندها سرمایهگذاری میکنند.
8. کنترل کیفیت و آزمایشهای مهم بیلت فولادی 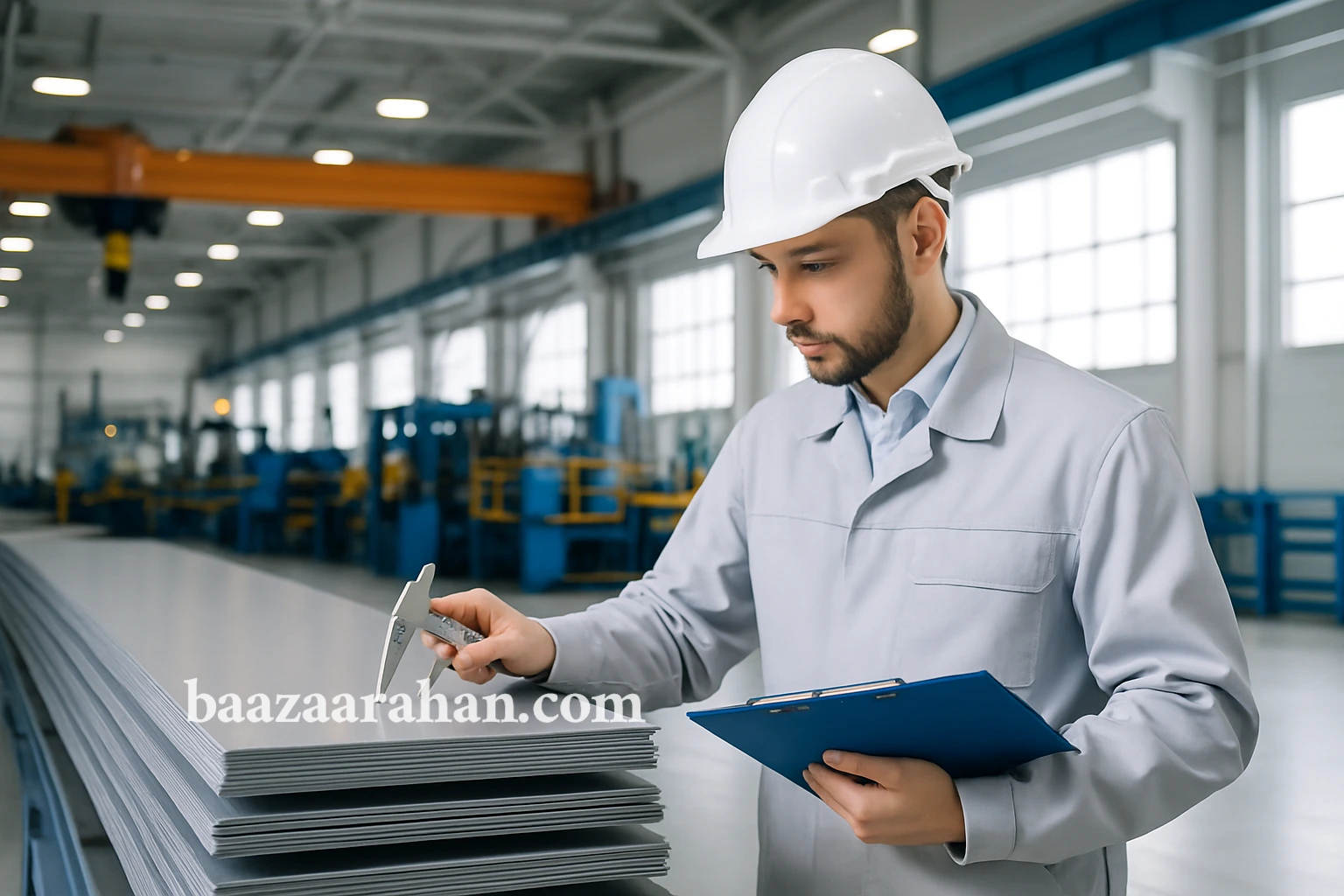
این کار در تولید بیلت اهمیت حیاتی دارد و تضمین میکند که محصول نهایی مطابق استانداردهای صنعتی و نیازهای مشتری باشد. کارخانههای فولادسازی از روشهای مختلف آزمایش و پایش برای اطمینان از کیفیت بیلت استفاده میکنند.
یکی از آزمایشهای متداول، آزمون سختی (Hardness Test) است که برای تعیین مقاومت سطحی بیلت به کار میرود. سختی مناسب، نشاندهنده مقاومت به سایش و استحکام فولاد است.
آزمون کشش (Tensile Test) نیز برای اندازهگیری مقاومت کششی و تغییر شکل پلاستیکی بیلت انجام میشود. این آزمایش پارامترهای مهمی مانند استحکام تسلیم، استحکام نهایی و درصد تغییر طول را مشخص میکند.
آزمایش ناپیوستگیها و ترکها (Non-destructive Testing – NDT) مثل التراسونیک (Ultrasonic Testing) و رادیوگرافی (Radiography) برای شناسایی عیوب داخلی مانند ترکها، حفرهها و ناخالصیها به کار میرود. این روشها بدون آسیب به بیلت، نقصها را تشخیص میدهند.
همچنین، آزمون شیمیایی برای تعیین ترکیب عناصر فولاد ضروری است. دستگاههایی مانند اسپکترو متر (Spectrometer) درصد کربن، منگنز، سیلیکون، کروم و سایر عناصر آلیاژی را اندازهگیری میکنند.
کنترل دما و ابعاد بیلت نیز از طریق حسگرهای دقیق و تجهیزات اتوماسیون انجام میشود. ابعاد استاندارد و یکنواخت بودن ضخامت در کیفیت نهایی محصول نقش مهمی دارند.
شرکتهایی مانند فولاد مبارکه و ArcelorMittal برای تضمین کیفیت، برنامههای کنترل دقیق و استانداردهای بینالمللی مانند ISO 9001 را رعایت میکنند. این اقدامات باعث افزایش رضایت مشتری و کاهش هزینههای ناشی از ضایعات میشود.
در نهایت، کنترل کیفیت بیلت نه تنها به تولید محصولات بهتر کمک میکند، بلکه به بهبود عملکرد کل زنجیره تولید فولاد نیز میانجامد.
9. بهینهسازی فرآیند تولید بیلت با فناوریهای نوین
صنعت فولاد همواره به دنبال روشهایی برای افزایش بهرهوری و کاهش هزینهها است. در تولید بیلت، فناوریهای نوین نقش مهمی در بهینهسازی فرآیندها ایفا میکنند.
یکی از پیشرفتهای مهم، استفاده از سیستمهای کنترل هوشمند (Advanced Process Control – APC) است. این سیستمها با بهرهگیری از دادههای واقعی و الگوریتمهای پیشرفته، پارامترهای تولید را بهینه میکنند. به کمک APC، نوسانات دما، سرعت نورد و جریان مذاب بهتر کنترل میشوند.
اتوماسیون و روباتیک در خطوط تولید بیلت، دقت و سرعت عملیات را افزایش داده است. روباتها در حمل و نقل، برش و بررسی محصولات به کار میروند و خطاهای انسانی را کاهش میدهند.
توسعه حسگرهای پیشرفته و اینترنت اشیاء (IoT) نیز امکان پایش لحظهای شرایط تولید را فراهم کرده است. این فناوریها به مدیران و اپراتورها امکان میدهند تا در زمان واقعی مشکلات را شناسایی و رفع کنند.
از طرفی، مدلسازی و شبیهسازی کامپیوتری فرآیند ریختهگری و نورد، به مهندسان اجازه میدهد تا قبل از اجرای عملی، پارامترها را بهینهسازی کنند و عیوب احتمالی را پیشبینی نمایند.
استفاده از مواد افزودنی و آلیاژهای نوین نیز باعث بهبود خواص مکانیکی و فیزیکی بیلت میشود. این نوآوریها به تولید محصولات خاص با ویژگیهای مطلوبتر منجر میگردد.
شرکتهای پیشرو مانند POSCO و Nippon Steel با سرمایهگذاری در فناوریهای نوین، علاوه بر کاهش هزینه، کیفیت محصولات خود را افزایش دادهاند و در بازار جهانی رقابتی باقی ماندهاند.
در مجموع، بهینهسازی فرآیند تولید بیلت با فناوریهای نوین، نه تنها بهرهوری و کیفیت را افزایش میدهد، بلکه اثرات زیستمحیطی را نیز کاهش میدهد و صنعت فولاد را به سمت تولید پایدار هدایت میکند.
10. نقش بیلت در زنجیره تأمین فولاد و بازار جهانی 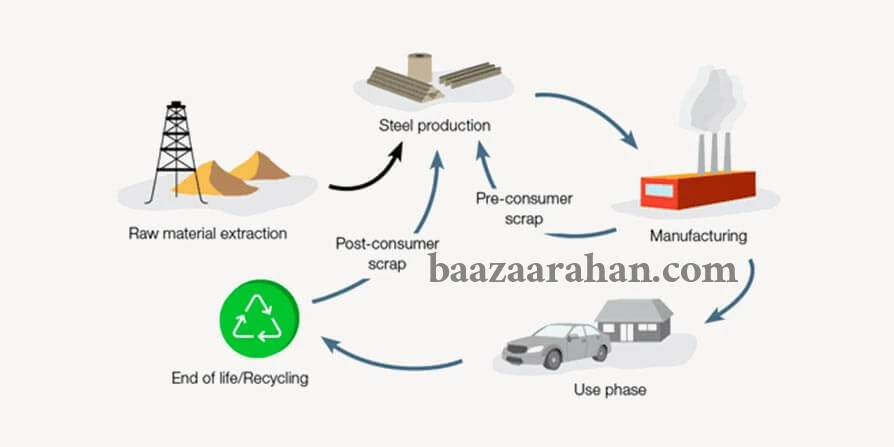
بیلت به عنوان محصول نیمهنهایی در زنجیره فولاد، نقش کلیدی در تأمین مواد اولیه برای تولید محصولات نهایی دارد. این قطعه فولادی به شکل شمشهای کوچکتر و با ابعاد مشخص، به واحدهای نورد و صنایع پاییندستی ارسال میشود.
بازار بیلت، تحت تأثیر عوامل مختلفی قرار دارد؛ از جمله نرخ تولید فولاد خام، تقاضای صنایع نهایی مانند ساختمان، خودروسازی و ساخت ماشینآلات. قیمت جهانی بیلت نیز با نوسانات بازار جهانی فولاد ارتباط مستقیم دارد.
کشورهایی مانند چین، هند، روسیه و برزیل از بزرگترین تولیدکنندگان و صادرکنندگان بیلت هستند. در مقابل، کشورهای صنعتی پیشرفته اغلب بیلت را وارد کرده و آن را در خطوط نورد خود به محصولات خاص تبدیل میکنند.
بیلتهای با کیفیت بالا، استانداردهای بینالمللی مانند ASTM و DIN را رعایت میکنند. این امر به تسهیل تجارت بینالمللی کمک میکند و امکان صادرات به بازارهای متنوع را فراهم میآورد.
یکی از چالشهای بازار بیلت، نوسانات قیمت و تأثیر سیاستهای تعرفهای و محدودیتهای تجاری است. شرکتها برای مدیریت این ریسکها از قراردادهای بلندمدت و قراردادهای آتی استفاده میکنند.
از نظر لجستیکی، بیلت به دلیل وزن و حجم مناسب، حمل و نقل آسانتری نسبت به شمشهای بزرگتر دارد. این ویژگی، انعطافپذیری بیشتری در توزیع و تأمین مواد اولیه ایجاد میکند.
به طور کلی، بیلت نه تنها یک محصول صنعتی است، بلکه یک عنصر حیاتی در زنجیره تأمین فولاد جهانی است که جریان مواد را بهینه و بازارها را پویا نگه میدارد.
11. چشمانداز آینده تولید و مصرف بیلت در صنعت فولاد
صنعت فولاد در حال تجربه تحولات چشمگیر است که بر تولید و مصرف بیلت تأثیرگذار خواهند بود. پیشرفتهای فناوری، تغییرات محیطزیستی و نیاز به محصولات با کیفیت بالاتر، روندهای آینده را شکل میدهند.
یکی از روندهای مهم، تمرکز بر تولید پایدار و کاهش آلایندگی است. فناوریهای جدید مانند بازیابی گرمای اضافی و استفاده از انرژیهای تجدیدپذیر، به کاهش مصرف انرژی در فرآیندهای ریختهگری و نورد کمک میکنند. تولید بیلت با کربن کمتر، به هدفهای زیستمحیطی نزدیکتر میشود.
توسعه آلیاژهای جدید و بهبود خواص مکانیکی بیلت، پاسخ به نیاز صنایع پیشرفته مانند هوافضا و خودروسازی است. این محصولات با وزن کمتر و استحکام بالاتر، جایگزین فولادهای سنتی میشوند.
اتوماسیون و هوشمندسازی خطوط تولید، نقش کلیدی در افزایش بهرهوری و کیفیت دارند. استفاده از دادههای بزرگ (Big Data) و یادگیری ماشین، به بهبود کنترل فرآیند و پیشبینی عیوب کمک میکند.
بازارهای نوظهور نیز تقاضای بیلت را افزایش میدهند. رشد زیرساختها و صنایع سبک در کشورهای در حال توسعه، به افزایش مصرف بیلت منجر خواهد شد.
در مقابل، چالشهایی مانند نوسانات قیمت مواد اولیه و تغییرات قوانین تجاری، همچنان باقی خواهند ماند. شرکتها برای موفقیت در این شرایط، باید انعطافپذیری و نوآوری را در اولویت قرار دهند.
در نهایت، آینده بیلت در صنعت فولاد ترکیبی از فناوری پیشرفته، توجه به پایداری و پاسخگویی به نیازهای متغیر بازار خواهد بود. این روندها، مسیر تولید و مصرف را به سمت بهرهوری بالاتر و اثرات محیطی کمتر هدایت میکنند.