اسلب فولادی چیست؟ صفر تا صد تولید، کاربرد و بازار اسلب در زنجیره فولاد
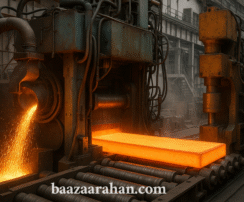
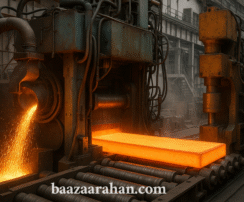
1. اسلب فولادی چیست؟ 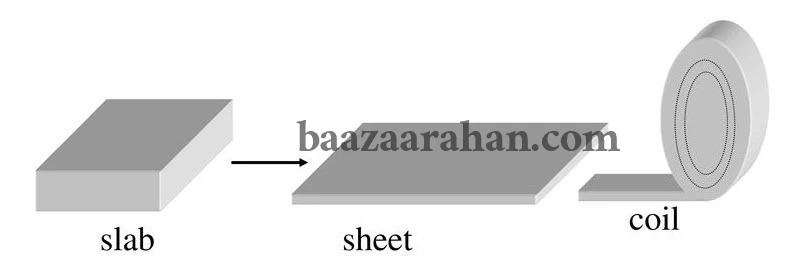
اسلب فولادی (Slab) یکی از محصولات نیمهنهایی در زنجیره تولید فولاد است. این قطعه فولادی به شکل مستطیل ضخیم و پهن تولید میشود و در ادامه زنجیره به ورق، کویل یا سایر محصولات فولادی تخت تبدیل میگردد. به زبان ساده، اسلب نقطهی اتصال بین فولاد مذاب و محصولات تخت نوردشده است.
اسلب معمولاً در فرآیند ریختهگری مداوم تولید میشود. ابعاد معمول آن بهصورت زیر است:
-
ضخامت: بین ۱۵۰ تا ۲۵۰ میلیمتر
-
عرض: بین ۷۰۰ تا ۲۰۰۰ میلیمتر
-
طول: معمولاً تا ۱۲ متر
در مقایسه با دیگر محصولات نیمهنهایی مانند بیلت (Billet) و بلوم (Bloom)، اسلب برای تولید محصولات تخت استفاده میشود، در حالی که بیلت و بلوم برای محصولات طویل مثل میلگرد یا تیرآهن کاربرد دارند. این تفاوت در شکل و کاربرد باعث شده اسلب بخش حیاتی صنعت نورد گرم باشد.
ویژگیهای اصلی اسلب فولادی شامل موارد زیر است:
-
تراکم بالا و سطح صاف برای نورد مستقیم
-
قابلیت آلیاژسازی جهت کاربردهای خاص
-
قابلیت برش و شکلدهی آسان
تولید اسلب اولین گام برای ساخت بسیاری از محصولات صنعتی از جمله ورق گرم، ورق سرد، ورق گالوانیزه و ورق رنگی است. بنابراین نقش آن در صنایع پاییندستی فولاد حیاتی است. بدون تولید اسلب با کیفیت، چرخه نورد تخت مختل میشود.
در بازار فولاد، اسلب یکی از شاخصترین کالاهای پایه به شمار میرود. قیمت اسلب معمولاً بر اساس قیمت جهانی سنگ آهن، هزینه انرژی، کیفیت تولید و میزان تقاضا در صنایع پاییندستی تعیین میشود. به همین دلیل، آشنایی با مفهوم اسلب برای فعالان این حوزه الزامی است.
2. فرآیند تولید اسلب چگونه است؟
تولید اسلب فولادی از مراحل ابتدایی تبدیل مواد خام تا رسیدن به محصول نیمهنهایی انجام میشود. ابتدا سنگ آهن یا گندلههای آن وارد کورههای صنعتی میشوند. این مواد در کوره بلند یا کوره قوس الکتریکی (EAF) ذوب میشوند تا چدن مذاب یا فولاد مذاب تولید شود.
در مرحله بعد، فولاد مذاب به واحد ریختهگری مداوم (Continuous Casting) منتقل میشود. در این مرحله، فولاد مذاب داخل قالبهای خنکشونده ریخته میشود و به صورت پیوسته به شکل اسلب جامد درمیآید. ریختهگری مداوم سرعت تولید را افزایش میدهد و کیفیت سطح اسلب را بهبود میبخشد.
ابعاد اسلب در این مرحله کنترل میشود و معمولاً ضخامت بین ۱۵۰ تا ۲۵۰ میلیمتر و عرض بین ۷۰۰ تا ۲۰۰۰ میلیمتر است. پس از سرد شدن اولیه، اسلبها به صورت بلوکهای بزرگ برش داده شده و برای مراحل بعدی ذخیره میشوند.
در برخی کارخانهها، اسلبها تحت عملیات حرارتی کنترل شده قرار میگیرند تا خواص مکانیکی بهتری پیدا کنند. همچنین، آزمایشهای کیفی مانند تست ترکخوردگی و بررسی ترکیب شیمیایی انجام میشود تا از کیفیت محصول اطمینان حاصل شود.
فرآیند تولید اسلب به شدت به تأمین مواد اولیه، تجهیزات پیشرفته و کنترل دقیق دما و سرعت ریختهگری وابسته است. هرگونه خطا در این مراحل میتواند منجر به عیوب سطحی، ترکهای داخلی یا ناپیوستگی در اسلب شود.
به طور خلاصه، فرآیند تولید اسلب ترکیبی از ذوب مواد خام، ریختهگری مداوم، برش و کنترل کیفیت است که پایه و اساس تولید ورقهای فولادی و دیگر محصولات تخت را شکل میدهد. به همین دلیل، توجه ویژه به هر مرحله، کیفیت و عملکرد زنجیره فولاد را تضمین میکند.
3. انواع اسلب فولادی
اسلب فولادی انواع مختلفی دارد که هرکدام با توجه به ترکیب شیمیایی و کاربرد نهاییشان دستهبندی میشوند. این تنوع، تولید فولاد را برای کاربردهای گوناگون صنعتی ممکن میسازد.
اولین دسته، اسلب کربنی است. این نوع اسلب حاوی درصد کمی کربن بوده و بیشتر در تولید ورقهای ساختمانی و صنعتی استفاده میشود. اسلب کربنی به دلیل هزینه تولید پایین، بیشترین سهم را در بازار اسلب دارد.
دسته دوم، اسلب آلیاژی است. این نوع شامل عناصر اضافهشدهای مانند کروم، نیکل، مولیبدن یا وانادیم است که خواص مکانیکی و مقاومتی فولاد را افزایش میدهد. اسلب آلیاژی معمولاً در صنایع خودروسازی، هوافضا و ساخت قطعات حساس کاربرد دارد.
سومین نوع، اسلب فولاد ضدزنگ (Stainless Steel Slab) است. این اسلبها ترکیبی از کروم و نیکل دارند که مقاومت بسیار بالایی در برابر خوردگی و اکسیداسیون به آنها میدهد. تولید این اسلبها به تجهیزات خاص و فرایندهای کنترل شده نیاز دارد.
در نهایت، اسلبهای خاص برای کاربردهای استراتژیک وجود دارند، مانند اسلبهای API (American Petroleum Institute) که برای ساخت لولههای نفت و گاز به کار میروند. این اسلبها استانداردهای فنی بسیار دقیق و مقاومت مکانیکی بالا دارند.
استانداردهای بینالمللی مانند ASTM، EN و JIS دستهبندی و مشخصات هر نوع اسلب را تعیین میکنند. رعایت این استانداردها برای تضمین کیفیت و پذیرش محصولات در بازارهای جهانی ضروری است.
در کل، شناخت انواع اسلب و ویژگیهای آنها برای انتخاب صحیح در تولید فولاد و محصولات پاییندستی اهمیت زیادی دارد. این تنوع باعث شده صنعت فولاد بتواند به نیازهای مختلف بازار پاسخ دهد و کیفیت مطلوب را حفظ کند.
4. تأثیر کیفیت اسلب روی محصولات نهایی
کیفیت اسلب فولادی نقش حیاتی در تعیین عملکرد و دوام محصولات نهایی دارد. اسلب به عنوان ماده اولیه، پایه و اساس ورقها، کویلها و سایر محصولات تخت فولادی است؛ بنابراین هر نقص یا ضعف در کیفیت اسلب، مستقیماً روی محصول نهایی تأثیر میگذارد.
اولین نکته، یکنواختی ترکیب شیمیایی اسلب است. اگر میزان کربن، منگنز، کروم یا سایر عناصر آلیاژی به درستی کنترل نشود، خواص مکانیکی ورقها مانند سختی، انعطافپذیری و مقاومت به خوردگی کاهش مییابد. به همین دلیل، کارخانههای فولاد به آزمایش دقیق مواد اولیه اهمیت میدهند.
دوم، عیوب سطحی و داخلی اسلب تأثیر مستقیم روی کیفیت نورد شده دارد. ترکها، حفرهها، و ناپیوستگیهای درونی میتوانند در فرآیند نورد باعث شکستگی یا کاهش استحکام ورق شوند. این عیوب معمولاً ناشی از مشکلات در ریختهگری مداوم یا سرد شدن نامناسب اسلب است.
سوم، تراکم و ساختار دانهبندی اسلب نقش مهمی در شکلدهی و عملیات حرارتی بعدی دارد. ساختار دانه ریز و یکنواخت، ورقهای نهایی را مقاومتر و با کیفیتتر میکند، در حالی که دانههای درشت میتوانند باعث ضعف مکانیکی و ترکهای پنهان شوند.
چهارم، کنترل ضخامت و ابعاد دقیق در اسلب، تضمین میکند که ورقها و کویلهای تولید شده به ابعاد استاندارد و مورد نیاز بازار برسند و نیاز به عملیات سنگین برش و اصلاح نداشته باشند.
در نهایت، پایین بودن کیفیت اسلب باعث افزایش ضایعات، هزینههای تولید و کاهش عمر مفید محصولات نهایی میشود. به همین دلیل، توجه ویژه به فرایند تولید و کنترل کیفیت اسلب فولادی، کلید موفقیت در تولید محصولات فولادی با کیفیت است.
5. کاربردهای اسلب در صنایع مختلف
اسلب فولادی به عنوان ماده اولیه اصلی در تولید محصولات تخت فولادی کاربردهای گستردهای دارد. این کاربردها شامل مراحل و صنایع مختلفی میشود که هرکدام اهمیت ویژهای در زنجیره فولاد دارند.
برخی از مهمترین کاربردهای اسلب عبارتاند از:
-
نورد گرم: اسلب پس از تولید وارد خطوط نورد گرم میشود و به ورقها و کویلهای فولادی تبدیل میگردد. این ورقها پایه بسیاری از محصولات صنعتی هستند.
-
خودروسازی: ورقهای حاصل از اسلب در ساخت بدنه خودرو، قطعات بدنه و شاسی استفاده میشوند که نیازمند کیفیت بالا و مقاومت مناسب هستند.
-
صنایع ساختمانی: اسلبها مبنای تولید ورقهای ساختمانی مانند سقفها، نماها و اسکلت فلزی هستند که مقاومت و استحکام بالایی لازم دارند.
-
ساخت لوله و تانک: ورقهای تولیدشده از اسلب در ساخت لولههای نفت و گاز، مخازن تحت فشار و تانکهای ذخیره کاربرد دارند.
-
صنایع پوششدار: ورقهای گالوانیزه، رنگی و قلعاندود که از اسلب ساخته میشوند، در صنایع لوازم خانگی و بستهبندی کاربرد دارند.
-
نورد معکوس و نورد خاص: برخی اسلبها برای تولید ورقهای بسیار نازک یا خاص که در صنایع دقیق مانند هوافضا استفاده میشوند، طراحی میشوند.
با توجه به این کاربردها، کیفیت و ویژگیهای اسلب فولادی تأثیر مستقیم بر عملکرد و دوام محصولات نهایی دارد. همچنین، میزان مصرف اسلب در هر صنعت نشاندهنده اهمیت آن در چرخه فولاد کشور و جهان است.
6. تولیدکنندگان اصلی اسلب در ایران 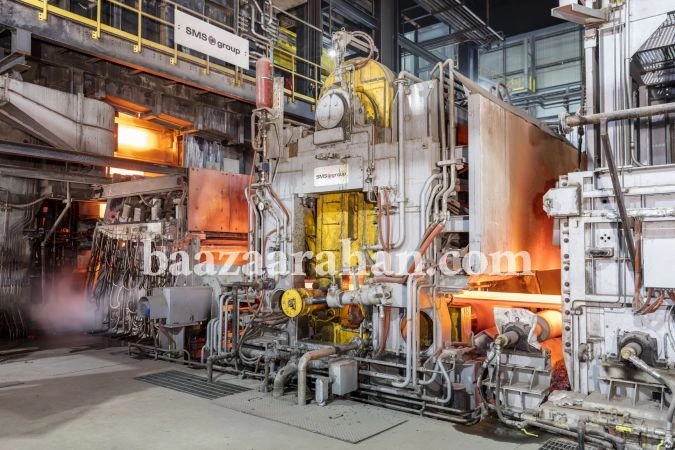
ایران با دارا بودن منابع غنی معدنی و زیرساختهای صنعتی، تولید اسلب فولادی را در چند کارخانه بزرگ انجام میدهد. این تولیدکنندگان نقش حیاتی در تأمین نیاز بازار داخلی و صادرات ایفا میکنند.
از مهمترین تولیدکنندگان اسلب در ایران میتوان به موارد زیر اشاره کرد:
-
فولاد مبارکه اصفهان: بزرگترین تولیدکننده اسلب در کشور است و بخش عمدهای از نیاز داخلی را تأمین میکند. این کارخانه با بهرهگیری از فناوری روز و تجهیزات پیشرفته، اسلبهای با کیفیت بالا تولید میکند.
-
فولاد خوزستان: دومین تولیدکننده بزرگ اسلب در ایران، با ظرفیت قابل توجه و تنوع محصولات آلیاژی برای صنایع مختلف. این شرکت نقش مهمی در تأمین اسلب برای صنایع پاییندستی دارد.
-
فولاد هرمزگان: تولیدکننده اسلب در جنوب کشور که با تمرکز بر بازارهای صادراتی، بخش قابل توجهی از اسلب تولیدی را به کشورهای منطقه صادر میکند.
-
فولاد کاوه جنوب کیش: این کارخانه نیز بهعنوان تولیدکننده نسبتا جدید اسلب، توانسته ظرفیت تولید را افزایش دهد و به بازار داخلی و خارجی خدمترسانی کند.
هر یک از این تولیدکنندگان ویژگیها و مزایای خاص خود را دارند، مانند استفاده از مواد اولیه با کیفیت، بهرهوری انرژی و کنترل کیفیت دقیق. به همین دلیل، کیفیت اسلب تولیدی آنها قابل اعتماد و مطابق با استانداردهای جهانی است.
شناخت و بررسی تولیدکنندگان اسلب در ایران برای فعالان بازار فولاد اهمیت زیادی دارد، چرا که انتخاب تأمینکننده مناسب میتواند تأثیر مستقیم بر کیفیت و هزینه محصولات نهایی داشته باشد.
7. بازار اسلب ایران و جهان
بازار اسلب فولادی یکی از مهمترین بخشهای صنعت فولاد است که تحت تأثیر عوامل مختلف اقتصادی، سیاسی و فنی قرار دارد. تقاضا، عرضه و قیمت اسلب به هم پیوستهاند و نوسانات بازار جهانی تأثیر زیادی روی آن دارد.
در بازار ایران، قیمت اسلب به چند عامل کلیدی وابسته است:
-
قیمت جهانی سنگ آهن که ماده اولیه اصلی است و تغییرات آن قیمت تمامشده اسلب را تغییر میدهد.
-
هزینه انرژی مانند برق و گاز که بخش قابل توجهی از هزینه تولید را شامل میشود.
-
هزینه حمل و نقل به دلیل حجم و وزن بالای اسلب، تأثیر مهمی بر قیمت نهایی دارد.
-
محدودیتها و تحریمهای بینالمللی که واردات تجهیزات و صادرات اسلب را تحت تاثیر قرار میدهد.
در بازار جهانی، کشورهایی مانند چین، هند، روسیه و برزیل از بزرگترین تولیدکنندگان و مصرفکنندگان اسلب هستند. چین به عنوان بزرگترین تولیدکننده فولاد جهان، سهم عمدهای در بازار اسلب دارد و نوسانات تقاضای آن باعث تغییرات شدید قیمتها میشود.
ایران با وجود ظرفیت بالای تولید اسلب، در رقابت با بازارهای منطقهای با چالشهایی مانند محدودیت صادرات و نوسانات ارزی روبرو است. با این حال، موقعیت جغرافیایی مناسب در خلیج فارس و دسترسی به بازارهای خاورمیانه و آسیای میانه، فرصتهای صادراتی خوبی ایجاد کرده است.
در مجموع، بازار اسلب فولادی پویا و پر از فرصت است، اما موفقیت در این بازار نیازمند تحلیل دقیق عوامل تأثیرگذار و مدیریت صحیح زنجیره تأمین است.
8. فرصتها و چالشهای صنعت اسلب در ایران
صنعت تولید اسلب فولادی در ایران با فرصتها و چالشهای متعددی روبهرو است که میتواند مسیر توسعه آن را شکل دهد. شناخت این عوامل برای تصمیمگیران و فعالان بازار اهمیت زیادی دارد.
از مهمترین فرصتها میتوان به موارد زیر اشاره کرد:
-
منابع غنی معدنی ایران که تامین سنگآهن با کیفیت و هزینه پایین را ممکن میسازد.
-
بازار رو به رشد داخلی و منطقهای که تقاضا برای محصولات فولادی را افزایش داده است.
-
مزیت جغرافیایی در دسترسی به بازارهای کشورهای خاورمیانه و آسیای میانه.
-
پتانسیل توسعه فناوریهای نوین مانند ریختهگری مداوم پیشرفته و فولاد سبز.
در مقابل، چالشهای مهم نیز وجود دارد که باید به آنها توجه شود:
-
تحریمهای بینالمللی که محدودیت واردات تجهیزات پیشرفته و صادرات محصولات را ایجاد کرده است.
-
کمبود منابع انرژی پایدار، به ویژه نوسانات در تأمین برق و گاز که هزینه تولید را افزایش میدهد.
-
مشکلات زیرساختی و لجستیکی در حملونقل و توزیع مواد اولیه و محصولات نهایی.
-
نیاز به بهبود کیفیت و استانداردها برای رقابت در بازارهای جهانی.
مدیریت درست این فرصتها و چالشها میتواند باعث افزایش ظرفیت تولید، بهبود کیفیت اسلب و ارتقای موقعیت ایران در بازارهای جهانی شود. به همین دلیل، توجه به سرمایهگذاری در فناوری و بهبود زیرساختها ضروری است.
9. مطالعه موردی: بهبود کیفیت اسلب در فولاد مبارکه اصفهان
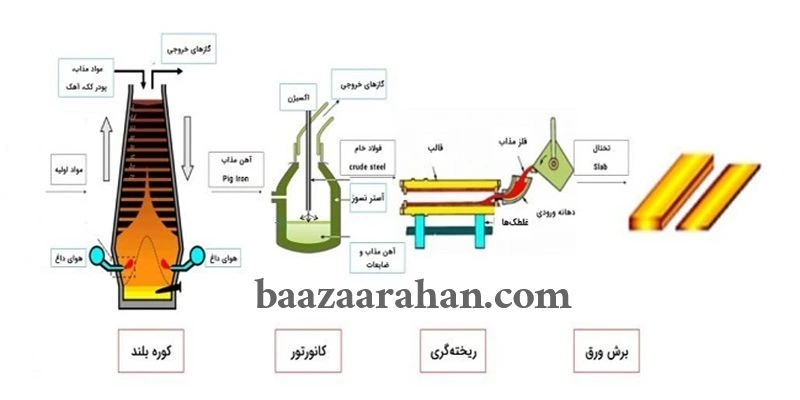
تولید اسلب فولادی با کوره بلند
فولاد مبارکه اصفهان به عنوان بزرگترین تولیدکننده اسلب در ایران، نمونهای عالی برای بررسی تاثیر کیفیت اسلب بر محصولات نهایی است. این کارخانه با تمرکز بر فناوریهای نوین و بهینهسازی فرآیند تولید، توانسته کیفیت اسلب خود را به طور چشمگیری افزایش دهد.
یکی از پروژههای مهم فولاد مبارکه، بهبود فرآیند ریختهگری مداوم (Continuous Casting) بود. این کارخانه با نصب سیستمهای پیشرفته کنترل دما و سرعت ریختهگری، توانست عیوب داخلی مانند ترکها و ناپیوستگیها را کاهش دهد. کاهش این عیوب باعث شد ورقهای تولید شده مقاومت مکانیکی بیشتری داشته باشند و درصد ضایعات در مراحل نورد به شدت کاهش یابد.
علاوه بر این، فولاد مبارکه با کنترل دقیق ترکیب شیمیایی مواد اولیه، توانست اسلبهای آلیاژی با خواص بهتر و مطابق با استانداردهای جهانی تولید کند. این اقدام کیفیت ورقهای فولادی را در صنایع خودرو، لولهسازی و ساختوساز بهبود بخشید.
نتیجه این پروژهها، افزایش رضایت مشتریان داخلی و خارجی بود و کمک کرد فولاد مبارکه موقعیت خود را در بازارهای صادراتی مستحکمتر کند. همچنین، هزینههای تولید کاهش یافت و بهرهوری به طور قابل توجهی افزایش پیدا کرد.
این مطالعه موردی نشان میدهد که سرمایهگذاری در فناوری و کنترل کیفیت، نه تنها کیفیت اسلب بلکه کل زنجیره تولید فولاد را بهبود میبخشد و میتواند مزیت رقابتی مهمی در بازارهای داخلی و جهانی ایجاد کند.
10. آینده صنعت اسلب فولادی
آینده صنعت اسلب فولادی با تحولات فناوری و تغییرات بازار جهانی شکل میگیرد. این صنعت با روندهای نوینی مواجه است که میتواند بهرهوری و کیفیت محصولات را به طور چشمگیری افزایش دهد.
یکی از روندهای مهم، تولید اسلبهای نازکتر و خاصتر است که نیاز بازار به ورقهای دقیق و سبک را برآورده میکند. این تغییرات باعث کاهش مصرف مواد اولیه و افزایش صرفهجویی در انرژی میشود.
دیگر تحول کلیدی، دیجیتالسازی تولید و ورود به عصر صنعت ۴.۰ است. استفاده از دادهکاوی، هوش مصنوعی و کنترل خودکار خط تولید باعث افزایش کیفیت، کاهش ضایعات و بهبود سرعت تولید میشود.
همچنین، حرکت به سمت فولاد سبز و استفاده از انرژیهای تجدیدپذیر و روشهای کاهش کربن، از چالشهای زیستمحیطی صنعت اسلب است. کشورها و شرکتهای فولادی بزرگ به دنبال کاهش اثرات زیستمحیطی و پایدارسازی تولید هستند.
در بازار جهانی، تقاضا برای اسلبهای با کیفیت بالا و استانداردهای ویژه افزایش مییابد. رقابت فزاینده باعث شده تولیدکنندگان به سمت نوآوری، بهبود کیفیت و کاهش هزینهها حرکت کنند.
در نهایت، سرمایهگذاری در فناوریهای جدید، آموزش نیروی انسانی و توسعه زیرساختها کلید موفقیت صنعت اسلب در دهههای آینده است. این روندها میتوانند ایران را در بازارهای جهانی اسلب به جایگاه بالاتری برسانند.