میلگرد در زنجیره فولاد (بخش اول): فرآیند تولید، انواع و ویژگیهای فنی
1. مقدمه
میلگرد؛ ستون فقرات سازههای مدرن
میلگرد یکی از مهمترین محصولات پاییندستی در زنجیره فولاد است که نقش کلیدی در صنعت ساختوساز ایفا میکند. این محصول فلزی، با افزایش مقاومت کششی بتن، امنیت سازهها را در برابر بارهای فشاری، کششی و لرزهای تضمین میکند.
در زنجیره فولاد، میلگرد پلی ارتباطی میان تولید شمش و کاربردهای عمرانی به شمار میرود. این ارتباط، میلگرد را به محصولی راهبردی در پروژههای عمرانی، صنعتی و زیربنایی بدل کرده است.
دلایل اهمیت میلگرد در زنجیره فولاد:
-
تقویت بتن و افزایش دوام سازهها
-
مصرف گسترده در ساختمانسازی، پلها، سدها و تونلها
-
ایجاد ارزش افزوده بالا نسبت به شمش فولاد
با توجه به رشد تقاضای زیرساختی و توسعه شهری، بررسی دقیق میلگرد از منظر تولید، ویژگیهای فنی و کاربرد، ضرورتی اجتنابناپذیر است. این مقاله، بخش اول از بررسی جامع میلگرد در زنجیره فولاد است و به جنبههای فنی و مهندسی این محصول خواهد پرداخت.
2. زنجیره تأمین فولاد تا میلگرد
مسیر تولید میلگرد از معدن تا کاربرد نهایی
در زنجیره فولاد، میلگرد بهعنوان یکی از محصولات نهایی، پس از طی چند مرحله حیاتی تولید میشود. این زنجیره از استخراج سنگآهن آغاز میشود و به شکلگیری میلگرد در نوردهای گرم ختم میشود. شناخت این مسیر برای درک موقعیت میلگرد در ساختار صنعتی فولاد اهمیت بالایی دارد.
مراحل اصلی زنجیره تأمین میلگرد:
-
استخراج سنگآهن:
فرآیند از معادن آغاز میشود. سنگآهن بهعنوان ماده اولیه اصلی، از معادن روباز یا زیرزمینی استخراج میشود. -
تبدیل به گندله و آهن اسفنجی (DRI):
سنگآهن پس از خردایش، در کارخانههای گندلهسازی آماده احیا میشود. سپس در کورههای احیای مستقیم، به آهن اسفنجی تبدیل میشود. -
تولید شمش فولادی:
آهن اسفنجی همراه با قراضه، وارد کوره القایی یا قوس الکتریکی شده و ذوب میشود. در مرحله بعد، فولاد مذاب به شمش (بیلت) تبدیل میشود. -
نورد گرم و تولید میلگرد:
شمش فولادی در خطوط نورد گرم حرارت میبیند و تحت فشار غلطکها به میلگرد تبدیل میشود. در این مرحله، مشخصات فیزیکی و مکانیکی میلگرد تعیین میشود.
جایگاه میلگرد در زنجیره فولاد:
میلگرد آخرین حلقه از فرآیند نورد طولی است و نقش آن در ارزشآفرینی بسیار حیاتی است. با تبدیل شمش به میلگرد، فولاد به شکلی آمادهبهکار برای صنایع عمرانی، ساختمانی و زیرساختی درمیآید.
این فرآیند، میلگرد را به محصولی استراتژیک در زنجیره فولاد و محور اتصال صنعت فولاد با صنعت ساختمان تبدیل کرده است.
3. فرآیند تولید میلگرد 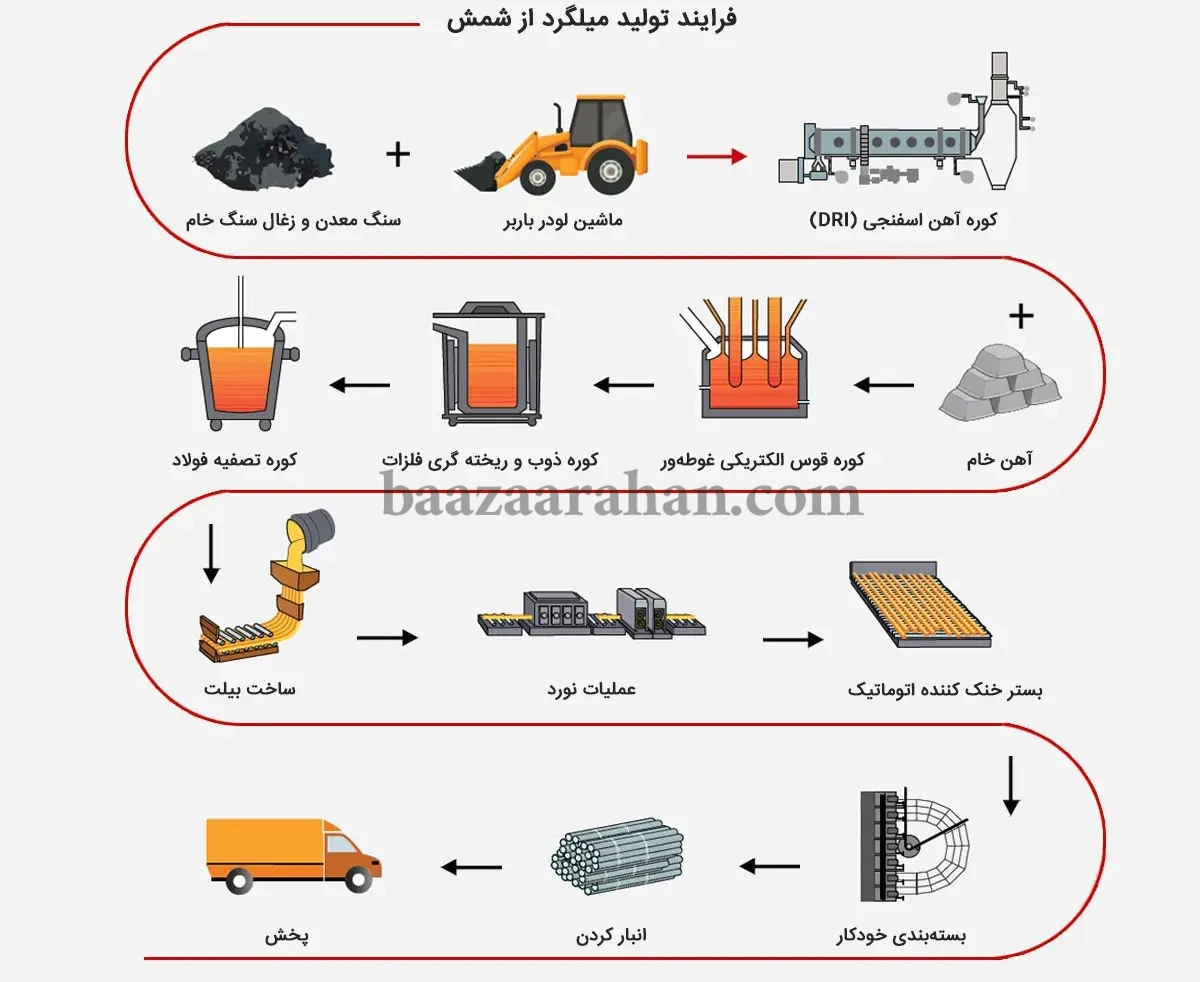
از شمش تا میلگرد نهایی؛ مسیر شکلگیری فولاد ساختمانی
فرآیند تولید میلگرد یکی از اصلیترین مراحل در زنجیره فولاد است که از شمش فولادی آغاز شده و با عبور از خطوط نورد گرم، به میلگرد آماده مصرف در صنعت ساختوساز تبدیل میشود. کیفیت نهایی میلگرد تا حد زیادی به دقت در این فرآیند بستگی دارد.
مراحل اصلی تولید میلگرد در نورد گرم:
-
پیشگرم کردن شمش فولادی:
شمشها (بیلتها) در کورههای نورد تا دمای حدود ۱۱۰۰ درجه سانتیگراد گرم میشوند تا برای شکلدهی آماده شوند. -
نورد اولیه و میانی:
شمش داغشده وارد قفسههای نورد میشود و بهتدریج قطر آن کاهش و طول آن افزایش مییابد. این تغییرات باعث بهدست آمدن قطر اولیه میلگرد میشود. -
نورد نهایی و آجزنی:
در مرحله پایانی، میلگرد به اندازه و فرم نهایی میرسد. برای میلگردهای آجدار، شیارها با قالبهای مخصوص روی سطح ایجاد میشود. -
خنککاری کنترلشده (TMT):
میلگردها بلافاصله پس از نورد وارد سیستم خنککاری حرارتی-مکانیکی میشوند. این فرآیند به افزایش استحکام و انعطافپذیری کمک میکند. -
برش، دستهبندی و بستهبندی:
میلگردهای تولیدشده با طول مشخص برش میخورند، بررسی کیفیت میشوند و سپس به شکل دستههای استاندارد بستهبندی میگردند.
نکات مهم در کیفیت تولید میلگرد:
-
یکنواختی دما در کوره نورد
-
دقت در آجزنی (مطابق استاندارد)
-
کنترل خنککاری برای استحکام نهایی
-
آزمون کشش، خمش و آنالیز شیمیایی
فرآیند نورد گرم با کنترلهای دقیق، محصولی تولید میکند که هم از نظر فیزیکی و هم مکانیکی آماده استفاده در انواع پروژههای عمرانی باشد. این بخش، نقطه اتصال تولید فولاد خام با نیاز مهندسی سازه است.
4. انواع میلگرد
دستهبندی میلگرد بر اساس شکل، کاربرد و استاندارد
در زنجیره فولاد، میلگردها به انواع مختلفی تقسیم میشوند که هر کدام بسته به نیاز پروژه، ویژگیهای خاصی دارند. شناخت این تنوع به مهندسان و مجریان پروژه کمک میکند تا انتخاب دقیقی برای شرایط سازهای داشته باشند.
بر اساس شکل سطح:
-
میلگرد ساده (Plain):
سطحی صاف و بدون آج دارد. معمولاً برای خاموتگذاری یا در بتنهایی با نیروهای کم استفاده میشود. -
میلگرد آجدار (Deformed):
دارای شیار یا آج روی سطح است. این طراحی باعث چسبندگی بهتر به بتن و عملکرد سازهای مؤثرتر میشود.
انواع میلگرد آجدار در ایران (طبق استاندارد 3132):
-
A1: میلگرد نرم، بدون آج
-
A2: آجدار مارپیچ، نیمهسخت
-
A3: آجدار جناقی، سخت
-
A4: آجدار مرکب، فوقسخت برای سازههای ضدزلزله
بر اساس جنس و آلیاژ:
-
فولاد کربنی: پرکاربردترین نوع، با مقاومت خوب و قیمت مناسب
-
میلگرد ضدزنگ (Stainless): مقاوم در برابر خوردگی، مناسب محیطهای خورنده
-
میلگرد گالوانیزه: پوشش روی برای محافظت در برابر رطوبت
-
میلگرد اپوکسی: با روکش رنگی پودری، کاربرد در مناطق ساحلی یا مرطوب
-
میلگرد کامپوزیتی (FRP, GFRP): غیرمغناطیسی، سبک، مقاوم به خوردگی، مناسب سازههای خاص
بر اساس استانداردهای فنی:
-
استاندارد ملی ایران 3132 (طبقهبندی A1 تا A4)
-
ASTM A615/A706 (آمریکا)
-
DIN 488 (آلمان)
-
BS 4449 (بریتانیا)
هر استاندارد، پارامترهایی چون مقاومت کششی، تسلیم، ترکیب شیمیایی و قابلیت جوشکاری را تعریف میکند.
نتیجه:
تنوع میلگردها در زنجیره فولاد پاسخگوی نیازهای متنوع پروژههای عمرانی، صنعتی و زیرساختی است. انتخاب صحیح نوع میلگرد، هم از نظر فنی و هم اقتصادی، تأثیر مستقیمی بر دوام و عملکرد سازه دارد.
5. خواص مکانیکی و فنی میلگرد 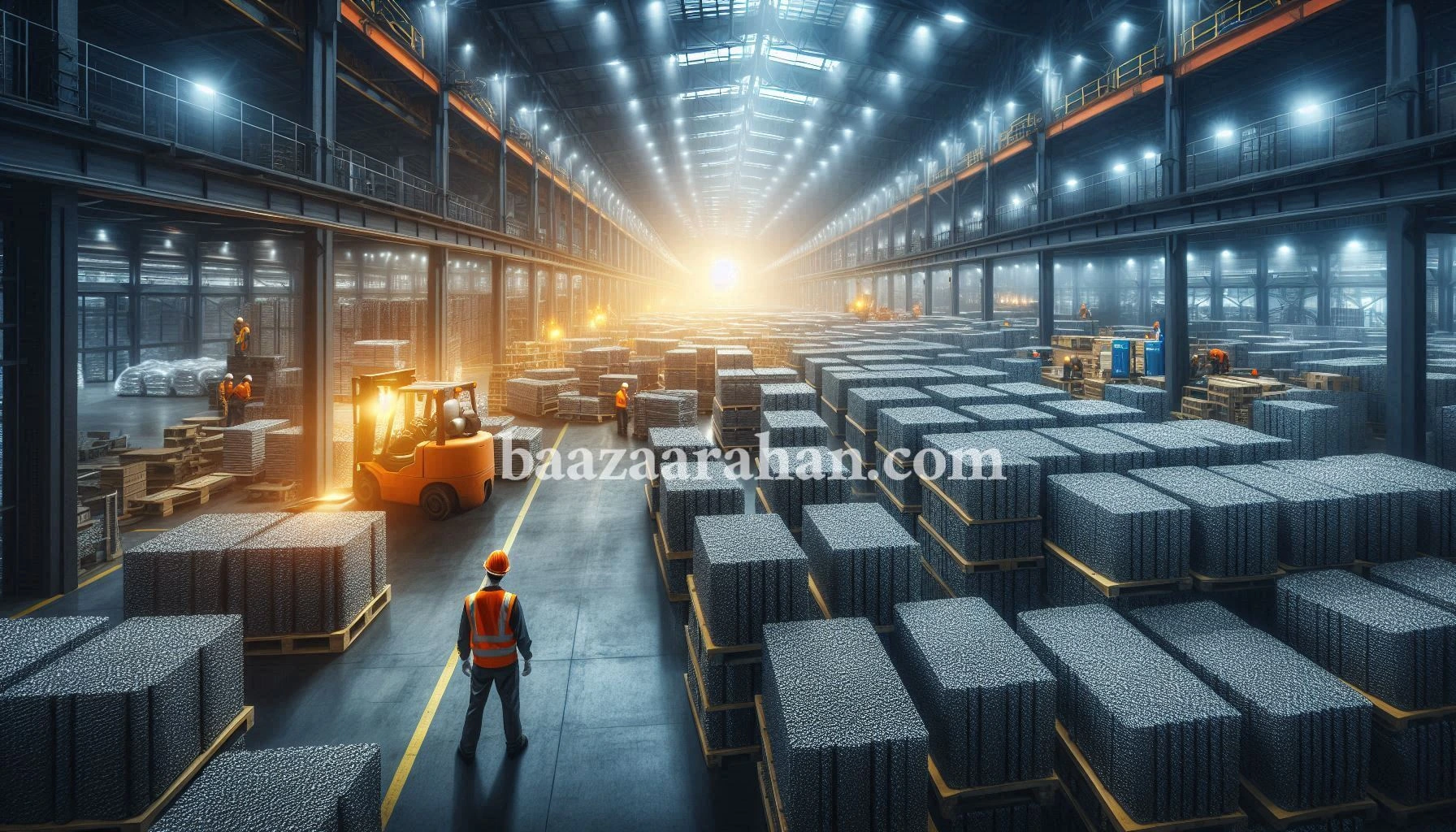
بررسی ویژگیهای عملکردی میلگرد در زنجیره فولاد
میلگرد در زنجیره فولاد تنها یک محصول نهایی نیست؛ بلکه باید مجموعهای از خواص مکانیکی مشخص را دارا باشد تا بتواند در شرایط سخت سازهای عملکرد مطلوبی ارائه دهد. این خواص در طول فرآیند تولید و با استفاده از کنترل کیفی دقیق بهدست میآید.
مهمترین خواص مکانیکی میلگرد:
-
مقاومت کششی (Ultimate Strength):
نیرویی که میلگرد میتواند قبل از گسست تحمل کند. این ویژگی برای تحمل بارهای وارده در سازهها حیاتی است. -
مقاومت تسلیم (Yield Strength):
نقطهای که میلگرد تحت فشار تغییر شکل دائمی میدهد. میلگردهایی با تسلیم بالا برای سازههای مقاوم در برابر زلزله کاربرد دارند. -
ازدیاد طول (Ductility):
توانایی میلگرد برای کش آمدن بدون شکست. هرچه انعطافپذیری بالاتر باشد، عملکرد سازه در برابر لرزش و تغییر شکل بهتر خواهد بود. -
خمشپذیری (Bendability):
میلگرد باید بدون ترک خوردگی یا شکست تا زاویه مشخصی خم شود. این ویژگی در مراحل نصب و شکلدهی اهمیت دارد.
خواص فنی مکمل:
-
جوشپذیری:
بسته به درصد کربن، برخی میلگردها بهتر به هم جوش میخورند. برای پروژههای صنعتی، میلگردهای با کربن پایین انتخاب بهتری هستند. -
پایداری در برابر خوردگی:
مقاومت میلگرد در برابر رطوبت، مواد شیمیایی یا نمک اهمیت زیادی دارد؛ مخصوصاً در مناطق ساحلی یا صنعتی. -
پایداری در برابر حرارت:
میلگرد باید در برابر نوسانات دمایی تاب بیاورد. بهخصوص در آتشسوزی یا تابش مستقیم خورشید، این ویژگی حیاتی است.
آزمونهای رایج بررسی کیفیت میلگرد:
-
آزمون کشش: بررسی مقاومت تسلیم و نهایی
-
آزمون خمش: ارزیابی شکلپذیری و انعطاف
-
آنالیز شیمیایی: سنجش ترکیب عناصر آلیاژی
-
تست خستگی (Fatigue): در پروژههای خاص مانند پلها یا سازههای دریایی
جمعبندی:
میلگرد با خواص مکانیکی و فنی مناسب، نهتنها ضامن پایداری سازههاست، بلکه به کاهش هزینههای نگهداری، افزایش عمر مفید ساختمان و ایمنی در برابر بلایای طبیعی منجر میشود. انتخاب صحیح میلگرد در زنجیره فولاد، بهمعنای انتخاب آیندهای ایمنتر است.
6. پوششها و محافظت از میلگرد
افزایش دوام میلگرد در زنجیره فولاد با پوششهای محافظتی
میلگرد در زنجیره فولاد نقش کلیدی در سازههای بتنی ایفا میکند، اما در معرض عوامل مخرب محیطی مانند رطوبت، خوردگی و زلزله است. استفاده از پوششهای محافظتی مختلف، راهکاری مؤثر برای افزایش طول عمر و حفظ کیفیت میلگرد است.
انواع پوششهای میلگرد:
-
گالوانیزه (Galvanized):
پوشش روی بهصورت لایهای محافظ روی سطح میلگرد قرار میگیرد. این پوشش از خوردگی در برابر رطوبت و مواد خورنده جلوگیری میکند. -
اپوکسی (Epoxy-coated):
میلگرد با پوشش رنگ اپوکسی پوشانده میشود. این پوشش برای محیطهای با خوردگی شدید مانند مناطق ساحلی و صنعتی مناسب است. -
میلگرد ضدزنگ (Stainless Steel):
خود میلگرد از فولاد ضدزنگ ساخته میشود و مقاومت بسیار بالایی در برابر زنگزدگی دارد، اما هزینه بالاتری دارد. -
میلگرد کامپوزیتی (Fiber Reinforced Polymer – FRP):
ساخته شده از الیاف کربن یا شیشه با ماتریس پلیمری، این میلگرد غیرمغناطیسی و مقاوم به خوردگی است. مناسب پروژههای خاص مانند تونلها و پلها.
مزایای استفاده از پوششها:
-
جلوگیری از خوردگی و زنگزدگی
-
افزایش عمر مفید سازه
-
کاهش هزینههای تعمیر و نگهداری
-
حفظ خواص مکانیکی میلگرد در شرایط محیطی سخت
نکات کاربردی در انتخاب پوشش میلگرد:
-
نوع پروژه: سازههای ساحلی یا صنعتی پوشش اپوکسی یا ضدزنگ نیاز دارند
-
شرایط محیطی: میزان رطوبت، تماس با مواد شیمیایی و نمک
-
بودجه پروژه: میلگرد گالوانیزه مقرونبهصرفهتر است ولی برای دوام بیشتر، میلگرد ضدزنگ یا کامپوزیتی ترجیح داده میشود
نتیجهگیری:
استفاده از پوششهای محافظتی متناسب با شرایط محیطی، باعث بهبود عملکرد میلگرد در زنجیره فولاد و افزایش امنیت سازه میشود. انتخاب صحیح پوشش، سرمایهگذاری در آینده پایدار سازه است.
7. کاربردهای فنی میلگرد
نقش کلیدی میلگرد در پروژههای ساختوساز و زیرساخت
میلگرد، بهعنوان یکی از اصلیترین محصولات زنجیره فولاد، در انواع پروژههای عمرانی و صنعتی کاربرد گستردهای دارد. این محصول فلزی، با افزایش مقاومت کششی و استحکام بتن، به بهبود عملکرد سازهها کمک میکند.
کاربردهای مهم میلگرد در صنعت ساختوساز:
-
بتن مسلح:
میلگرد در بتن بهعنوان عنصر تقویتی استفاده میشود تا مقاومت بتن را در برابر کشش افزایش دهد و از ترکخوردگی جلوگیری کند. -
اسکلتهای بتنی و پیشساخته:
در سازههای پیشساخته و اسکلتهای بتنی، میلگرد به شکلبندی و تثبیت اجزای مختلف کمک میکند و استحکام کلی سازه را بالا میبرد. -
پلها و تونلها:
بهدلیل نیاز به مقاومت بالا و انعطافپذیری، میلگردهای آجدار و خاص در ساخت پلها و تونلها به کار میروند. -
سدها و سازههای هیدرولیکی:
استفاده از میلگرد با مقاومت زیاد، در سدها برای تحمل فشارهای بالا و جلوگیری از ترکهای ناشی از فشار آب ضروری است. -
ساختمانهای ضدزلزله:
میلگردهای خاص با خواص مکانیکی ویژه در سازههای مقاوم در برابر زلزله استفاده میشوند تا ایمنی و پایداری ساختمان تضمین شود.
چرا میلگرد در زنجیره فولاد اینقدر حیاتی است؟
-
افزایش استحکام کششی بتن
-
جلوگیری از آسیبهای محیطی و فیزیکی سازه
-
کاهش هزینههای نگهداری و تعمیر در بلندمدت
-
قابلیت شکلدهی و انطباق با طراحیهای پیچیده ساختمانی
جمعبندی:
میلگرد بهعنوان یکی از ستونهای اصلی زنجیره فولاد، نهتنها در تولید بلکه در کاربردهای مهندسی، نقش بیبدیلی دارد. انتخاب صحیح نوع و کیفیت میلگرد، تضمینکننده دوام و ایمنی سازهها است.
8. جمعبندی و نتیجهگیری
مرور کلی بر نقش و اهمیت میلگرد در زنجیره فولاد
میلگرد بهعنوان یکی از اجزای کلیدی زنجیره فولاد، در همه مراحل از تولید تا مصرف، نقش حیاتی دارد. این محصول نهتنها با فرآیندهای پیشرفته تولید، بلکه با ویژگیهای مکانیکی و تنوع انواعش، سازههای مدرن را مقاوم و پایدار میکند.
در بخشهای قبلی دیدیم که:
-
تولید میلگرد شامل مراحل دقیق نورد گرم و خنککاری کنترلشده است که کیفیت و دوام محصول نهایی را تضمین میکند.
-
انواع مختلف میلگرد با پوششها و استانداردهای متعدد، پاسخگوی نیازهای متفاوت صنعت ساختوساز و پروژههای زیربنایی هستند.
-
خواص مکانیکی مانند مقاومت کششی، تسلیم و انعطافپذیری، اساس عملکرد میلگرد در سازهها را تشکیل میدهند.
-
پوششهای محافظتی و فرآیندهای حفاظتی باعث افزایش طول عمر میلگرد در محیطهای خورنده و سخت میشوند.
-
کاربردهای گسترده میلگرد در بتن مسلح، پلها، سدها و ساختمانهای ضدزلزله، اهمیت استراتژیک این محصول را در زنجیره فولاد برجسته میسازد.
نکته پایانی:
انتخاب و بهکارگیری میلگرد مناسب در هر پروژه، هم از منظر فنی و هم اقتصادی، تضمینکننده موفقیت سازه و بهرهوری سرمایه است. میلگرد، بهعنوان ستون فقرات زنجیره فولاد، پل ارتباطی میان تولید فولاد و توسعه پایدار زیرساختها است.