تولید فولاد و آلیاژسازی: فرآیندها، تکنولوژیها و اهمیت آن در صنایع مختلف
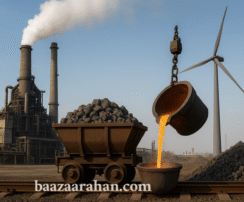
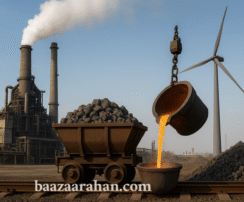
1. تولید فولاد و آلیاژسازی
- تولید فولاد و آلیاژسازی
یکی از فرآیندهای اصلی در صنعت فولاد است که در آن ترکیب فولاد با عناصر آلیاژی مختلف به فولادی با ویژگیهای خاص تبدیل میشود. این فرآیند نهتنها در تولید فولاد معمولی بلکه در تولید فولادهای خاص با خواص ویژه برای استفاده در صنایع مختلف، از جمله خودروسازی، ساخت و ساز، صنایع دریایی، و ساخت ابزارهای صنعتی، اهمیت دارد. در این مقاله، به تفصیل به فرآیند تولید فولاد، آلیاژسازی، و اهمیت آن در صنایع مختلف میپردازیم و همچنین تکنولوژیهای نوین در این زمینه را بررسی میکنیم.
- فرآیند آلیاژسازی: افزودن عناصر برای بهبود خواص فولاد
آلیاژسازی فرآیندی است که در آن فلزات مختلف به فولاد افزوده میشود تا ویژگیهای فیزیکی، شیمیایی و مکانیکی آن بهبود یابد. آلیاژسازی فولاد میتواند بهمنظور افزایش مقاومت به خوردگی، سختی، استحکام کششی، یا انعطافپذیری انجام شود. در این فرآیند، موادی مانند کروم، نیکل، منگنز، وانادیوم و مولیبدن به فولاد اضافه میشوند.
- فولاد ضد زنگ
یکی از معروفترین آلیاژهای فولادی است که با اضافه کردن کروم به فولاد تولید میشود. کروم در این فرآیند نهتنها باعث افزایش مقاومت به خوردگی میشود بلکه به فولاد خاصیت ضد زنگ زدگی نیز میدهد. همچنین، فولادهای منگنز دار برای افزایش استحکام و مقاومت به سایش استفاده میشوند، و فولادهایی که با نیکل آلیاژ شدهاند، معمولاً برای تولید قطعاتی که به انعطافپذیری بالا نیاز دارند، استفاده میشوند.
آلیاژسازی میتواند در مراحل مختلف تولید فولاد انجام شود. این فرآیند به دو روش اصلی انجام میشود: آلیاژسازی پیشرفته (در آن عناصر آلیاژی در ابتدا به فولاد اضافه میشوند) و آلیاژسازی پس از ریختهگری (که بعد از شکلدهی اولیه فولاد، به آن مواد آلیاژی اضافه میشود). این روشها به تولید فولادهایی با خواص منحصر به فرد کمک میکنند که در صنایع مختلف کاربرد دارند.
کورههای نورد: شبیهسازی ویژگیهای فولاد در دماهای بالا
یکی از مراحل کلیدی در فرآیند تولید فولاد، نورد فولاد است که در آن فولاد مذاب از کورههای نورد عبور داده میشود تا به محصولات مختلف تبدیل گردد. این فرآیند در دماهای بالا انجام میشود و برای تولید محصولاتی مانند ورق، میلگرد، و تیرآهن ضروری است. کورههای نورد از مهمترین تجهیزات در فرآیند تولید فولاد هستند که میتوانند به دو دسته اصلی تقسیم شوند: نورد گرم و نورد سرد.
در فرآیند نورد گرم، فولاد به دماهایی بالاتر از دمای تبلور خود میرسد (معمولاً بالاتر از 1000 درجه سانتیگراد). در این دما، فولاد بسیار انعطافپذیر میشود و به راحتی به اشکال مختلف مانند ورق، میلگرد و تیرآهن تبدیل میشود. نورد گرم معمولاً برای تولید فولادهایی با ضخامت بیشتر استفاده میشود. این فرآیند نهتنها به شکلدهی فولاد کمک میکند بلکه به بهبود خواص مکانیکی آن نیز میانجامد.
در نورد سرد، فولاد در دماهای پایینتری از دمای تبلور خود قرار میگیرد، که باعث افزایش دقت ابعادی و استحکام فولاد میشود. این فرآیند برای تولید محصولات فولادی نازک، مانند ورقهای فولادی نازک یا قطعات خاص صنعتی که نیاز به دقت بالا دارند، استفاده میشود. نورد سرد باعث افزایش استحکام فولاد و بهبود خواص سطحی آن میشود.
تکنولوژیهای نوین در تولید فولاد: نورد مداوم و کورههای قوس الکتریکی
با پیشرفتهای فناوری در صنعت فولاد، بسیاری از فرآیندهای تولید فولاد بهبود یافته و کارآمدتر شدهاند. یکی از این پیشرفتها، استفاده از نورد مداوم است که بهویژه در تولید فولادهای با کیفیت و کمهزینه مورد استفاده قرار میگیرد. در این فرآیند، فولاد بهطور مداوم از قالبها عبور کرده و به شکلهای مختلفی مانند شمش، بیلت، و اسلب تبدیل میشود. نورد مداوم میتواند سرعت تولید را افزایش داده و هزینهها را کاهش دهد.
کورههای قوس الکتریکی نیز یکی دیگر از تکنولوژیهای پیشرفته در آلیاژسازی فولاد هستند. این کورهها از برق برای ذوب فولاد و ترکیب آن با عناصر آلیاژی استفاده میکنند. استفاده از این کورهها به کاهش مصرف انرژی و افزایش دقت ترکیبهای شیمیایی کمک میکند. همچنین، این کورهها برای تولید فولادهای خاص با ویژگیهای منحصر به فرد بسیار مناسب هستند.
در کنار این تکنولوژیها، استفاده از کورههای القایی و فرآیندهای ریختهگری مداوم نیز به تولید فولاد با کیفیت کمک کرده است. این تکنولوژیها امکان تولید فولادهایی با خواص خاص و بدون ضایعات زیاد را فراهم میآورند.
اهمیت تولید فولاد و آلیاژسازی در صنایع مختلف
این دو مورد در بسیاری از صنایع پایهای و حیاتی است. این فرآیندها نهتنها به تولید فولادهایی با خواص ویژه کمک میکنند بلکه به بهبود کیفیت و بهرهوری در صنایع مختلف میانجامند. از فولاد ضد زنگ در صنایع ساختمانی و دریایی گرفته تا فولادهای منگنز دار در تولید قطعات ماشینآلات و خودروها، تولید فولاد و آلیاژسازی به عنوان عاملی کلیدی در توسعه صنایع مختلف شناخته میشود.
همچنین، فولادهای تولید شده با فرآیندهای آلیاژسازی در تجهیزات پزشکی، ابزارهای صنعتی، و تولید لوازم خانگی نیز کاربرد دارند. در نتیجه، آگاهی از فرآیندهای تولید فولاد و آلیاژسازی و استفاده از تکنولوژیهای نوین در این زمینه میتواند به بهرهوری بیشتر، کاهش هزینهها و بهبود کیفیت محصولات نهایی در صنایع مختلف منجر شود.
نتیجهگیری: فرآیندهای پیچیده و ضروری تولید فولاد و آلیاژسازی
در نهایت، تولید فولاد و آلیاژسازی فرآیندهایی پیچیده هستند که بهطور مستقیم بر ویژگیهای نهایی فولاد تأثیر میگذارند. این فرآیندها نهتنها به تولید فولادی با خواص خاص کمک میکنند بلکه با استفاده از تکنولوژیهای نوین مانند نورد مداوم و کورههای قوس الکتریکی، به افزایش کارایی و کاهش هزینهها در صنعت فولاد کمک میکنند. تولید فولاد با ویژگیهای خاص، نقشی اساسی در صنایع مختلف دارد و به همین دلیل آگاهی از فرآیندهای آن برای هر صنعتگری ضروری است.
2. ریختهگری و شکلدهی فولاد: فرآیندها و تکنولوژیهای مدرن
ریختهگری و شکلدهی فولاد از مهمترین مراحل تولید فولاد است که به تبدیل فولاد مذاب به محصولات نهایی میپردازد. این فرآیندها شامل ریختهگری مداوم، ریختهگری دورانی و قالبی، و شکلدهی اولیه فولاد میشوند. در این مقاله، این فرآیندها بهطور کامل توضیح داده میشوند و نقش آنها در تولید فولاد با کیفیت مورد بحث قرار میگیرد.
ریختهگری مداوم: تولید شمش فولادی با کیفیت
یکی از مهمترین فرآیندهای ریختهگری در صنعت فولاد، ریختهگری مداوم است. در این فرآیند، فولاد مذاب بهطور مداوم از کوره به داخل قالبها ریخته میشود تا به شکل شمش فولادی تبدیل شود. این فرآیند به تولید شمشهای فولادی با کیفیت و یکنواخت کمک میکند و در نتیجه هزینهها و زمان تولید کاهش مییابد. در ریختهگری مداوم، مهمترین نکته کنترل دما و سرعت انجماد فولاد است تا از ایجاد ضایعات و عدم یکنواختی در محصولات جلوگیری شود.
فرآیند ریختهگری مداوم، علاوه بر کاهش ضایعات، امکان تولید محصولات با ضخامت و ابعاد دقیق را فراهم میکند. همچنین، این روش میتواند به تولید انواع فولادهای آلیاژی و ضد زنگ که به دقت بالایی نیاز دارند، کمک کند. بهویژه، این فرآیند در تولید فولادهای مورد استفاده در صنایع خودروسازی، ساخت و ساز، و تولید لوازم صنعتی کاربرد دارد.
ریختهگری دورانی و قالبی: تولید با دقت بیشتر
ریختهگری دورانی یکی دیگر از فرآیندهای مهم در صنعت فولاد است که در آن فولاد مذاب در قالبهای دوار ریخته میشود. این فرآیند معمولاً برای تولید لولهها و قطعات خاص فولادی استفاده میشود. در ریختهگری دورانی، قالبها با سرعت مشخصی میچرخند تا فولاد مذاب بهطور یکنواخت در قالب توزیع شود و خواص مطلوبی بهدست آید.
ریختهگری قالبی نیز در بسیاری از موارد برای تولید شمشهای فولادی استفاده میشود. در این روش، فولاد مذاب در قالبهای ثابت ریخته میشود تا پس از سرد شدن به شکل موردنظر تبدیل گردد. این فرآیند برای تولید فولادهای معمولی و غیرآلیاژی که نیاز به دقت کمتری دارند، مناسب است.
شکلدهی اولیه فولاد: از شمش تا محصولات نیمهتمام
پس از اینکه فولاد بهشکل شمش یا بیلت در فرآیند ریختهگری تولید شد، باید این محصول اولیه تحت فرآیند شکلدهی اولیه قرار گیرد. در این مرحله، فولاد مذاب به محصولات نیمهتمامی مانند میلگرد، تیرآهن، و ورق تبدیل میشود. این فرآیند معمولاً از طریق نورد انجام میشود که فولاد را از دمای بالا به شکلهای مختلف تغییر میدهد.
نورد گرم معمولاً برای تولید قطعات ضخیم و بزرگ مانند تیرآهنها و میلگردها استفاده میشود. در این فرآیند، فولاد در دماهای بالا نورد میشود و سپس به اشکال مختلفی همچون لوله، میلگرد، یا ورق تبدیل میگردد. نورد گرم موجب میشود که فولاد بهراحتی شکل بگیرد و خواص مکانیکی آن بهبود یابد.
اهمیت ریختهگری و شکلدهی در تولید فولاد
فرآیندهای ریختهگری و شکلدهی فولاد بهطور مستقیم بر کیفیت و دقت ابعادی محصولات فولادی تأثیر میگذارند. این مراحل به فولاد کمک میکنند تا به شکلها و ابعاد مطلوب برسد و خواص فیزیکی و مکانیکی آن برای استفاده در صنایع مختلف بهبود یابد. به همین دلیل، استفاده از تکنولوژیهای نوین در این بخشها میتواند به تولید فولاد با کیفیت بالاتر و هزینههای کمتر منجر شود.
نتیجهگیری: نقش ریختهگری و شکلدهی فولاد در کیفیت نهایی محصولات
ریختهگری و شکلدهی فولاد نقش حیاتی در فرآیند تولید فولاد دارند. با استفاده از تکنیکهای مدرن و پیشرفته، تولید فولاد با ویژگیهای خاص و دقت بالا امکانپذیر شده است. این فرآیندها به بهبود کیفیت و کاهش هزینههای تولید کمک کرده و در نهایت فولاد با ویژگیهای مطلوب را به دست مصرفکنندگان میرسانند.
3. فرآیندهای تکمیلی فولاد: از نورد گرم تا آلیاژسازی مجدد
فرآیندهای تکمیلی در صنعت فولاد به عملیاتهایی اطلاق میشود که پس از مراحل ابتدایی تولید فولاد انجام میشوند. این فرآیندها شامل نورد گرم، نورد سرد، آلیاژسازی مجدد، و پروفیلسازی هستند و هدف آنها بهبود خواص فولاد و تبدیل آن به محصول نهایی با ویژگیهای خاص است.
نورد گرم: تبدیل فولاد به محصولات نیمهتمام
نورد گرم یکی از فرآیندهای کلیدی در تولید فولاد است که در آن فولاد مذاب به محصولات نیمهتمامی مانند ورق، میلگرد و تیرآهن تبدیل میشود. در این فرآیند، فولاد در دمای بالای 1000 درجه سانتیگراد نورد میشود که این دما باعث میشود فولاد به راحتی شکل بگیرد. نورد گرم موجب کاهش ضخامت فولاد و افزایش سطح مقطع آن میشود.
نورد سرد: افزایش استحکام و دقت ابعادی
این مورد یکی دیگر از فرآیندهای تکمیلی است که برای افزایش دقت ابعادی و استحکام فولاد به کار میرود. در این فرآیند، فولاد تحت فشار قرار میگیرد و در دماهای پایینتری نسبت به نورد گرم نورد میشود. این باعث افزایش استحکام فولاد و بهبود دقت ابعادی آن میشود. نورد سرد معمولاً برای تولید ورقهای نازک و دقیق با استحکام بالا استفاده میشود.
آلیاژسازی مجدد: بهبود خواص فولاد با افزودن دوباره عناصر آلیاژی
آلیاژسازی مجدد فرآیندی است که در آن مواد آلیاژی به فولاد اضافه میشود تا خواص آن بهبود یابد. این فرآیند میتواند بهمنظور افزایش مقاومت به خوردگی، سختی، یا استحکام فولاد انجام شود. در این مرحله، فولاد به شکلهای مختلفی مانند ورق، میلگرد یا لوله تولید میشود و به آن عناصر آلیاژی اضافه میشود تا به ویژگیهای مطلوب دست یابد.
پروفیلسازی: تولید محصولات فولادی با اشکال خاص
پروفیلسازی فرآیندی است که در آن فولاد به شکلهای خاصی مانند پروفیلهای ساختمانی یا صنعتی تبدیل میشود. این فرآیند معمولاً در دماهای بالا انجام میشود و باعث میشود فولاد به اشکال مختلفی مانند لوله، نبشی، تیرآهن و غیره تبدیل گردد. پروفیلسازی بهویژه در صنایع ساخت و ساز و خودروسازی کاربرد دارد.
نتیجهگیری: اهمیت فرآیندهای تکمیلی در تولید فولاد با خواص خاص
فرآیندهای تکمیلی نقش مهمی در بهبود خواص فولاد و تولید محصولات نهایی با ویژگیهای خاص دارند. این فرآیندها میتوانند به افزایش استحکام، دقت ابعادی، و مقاومت به خوردگی فولاد کمک کنند و در نهایت فولاد با کیفیت و عملکرد بالا به دست مصرفکنندگان برسد.
4. کنترل کیفیت و استانداردها: تضمین کیفیت محصولات فولادی
کنترل کیفیت و استانداردها از اجزای اساسی در تولید در زنجیره فولاد هستند که به اطمینان از کیفیت و عملکرد محصولات کمک میکنند. در این بخش، به روشها و آزمایشهای مختلفی که برای کنترل کیفیت فولاد انجام میشوند، پرداخته میشود.
آزمایشهای کیفیت فولاد: سنجش ویژگیهای فیزیکی و مکانیکی
یکی از مهمترین مراحل در فرآیند تولید فولاد، آزمایشهای کیفیت است که برای سنجش ویژگیهای فیزیکی و مکانیکی فولاد انجام میشود. این آزمایشها شامل آزمونهای استحکام کششی، سختی، انعطافپذیری و مقاومت به خوردگی میشود. آزمایشهای کیفیت به تولید فولاد با ویژگیهای مطلوب کمک میکنند و باعث اطمینان از عملکرد مناسب آن در کاربردهای مختلف میشوند.
استانداردهای جهانی و ملی در تولید فولاد
استانداردهای بینالمللی مانند ASTM و ISO برای تولید فولادهای با کیفیت بالا ضروری هستند. این استانداردها مشخصات دقیق و الزامات عملکردی برای فولادهای تولیدی تعیین میکنند و تضمین میکنند که محصولات نهایی مطابق با نیازهای صنعتی و استفادههای خاص باشند.
کنترل فرآیندها و شیمی فولاد: اطمینان از ترکیب مناسب
این مورد یکی دیگر از جنبههای مهم در تولید فولاد است که به ترکیب دقیق عناصر آلیاژی و فلزات پایه مربوط میشود. کنترل دقیق ترکیب شیمیایی فولاد باعث میشود که محصول نهایی دارای خواص مکانیکی و فیزیکی مطلوب باشد و برای کاربردهای خاصی که نیاز به استحکام و مقاومت بالا دارند، مناسب باشد.
نتیجهگیری: نقش کنترل کیفیت و استانداردها در موفقیت تولید فولاد
کنترل کیفیت و رعایت استانداردها در فرآیند تولید فولاد از اهمیت بالایی برخوردار است. این اقدامات باعث میشوند که فولاد تولیدی با ویژگیهای مطلوب و استانداردهای جهانی تطابق داشته باشد و در نتیجه برای استفاده در صنایع مختلف مناسب باشد.